Introduction Softness and intelligence will be the trend of human-machine interfaces in the near future. For example, robots and related equipment that are designed to support people in a variety of living environments should be covered with soft materials like human skin. In addition, robots and related equipment need to be given a capacity for sensing information from external environments. Therefore, the skin of such equipment becomes a kind of electronic device containing many sensors and integrated circuits [1, 2], not just a simple cover. As a milestone project for realizing human-machine interfaces that combine softness and intelligence, the present authors are developing a novel artificial skin containing the self-organized network of large numbers of sensors and data processors for humanoid robots and related equipment. In order to develop such artificial skin, advanced electronic packaging technology based on soft matter science must be established. As the first step of our study, we have developed super-flexible wires, electrodes and interconnections using conductive adhesives composed of a silicone-based binder [3]. Although we have successfully fabricated prototype sensor sheet containing organic piezoelectric sensors, several problems such as electrical properties of super-flexible adhesives and thermal stability of the sensors still remain. In the present work, improvement of the electrical properties of super-flexible adhesives and the thermal stability of the organic sensors was studied in order to fabricate sensor sheets with high performance. Experimental Procedure A conductive adhesive containing Ag filler particles (flake-shaped particles) dispersed in a silicone-based binder was used as the material for wires and interconnections formed on a silicone substrate. The conductive adhesives were modified with some additives such as non-reactive diluents and Ag colloidal solutions according to requirements. The electrical conductivity of the adhesives was measured by the four-point probe method after the curing process. In addition, the variation in electrical resistance of the specimens was monitored (by the two-probe electrical method) during the tensile test under a cross-head speed of 8.33 μm s-1 at ambient temperatures [3]. Piezoelectric films (with printed Ag electrodes) composed of poly(vinylidene fluoride) (PVDF) [4] were employed as the sensor. The piezoelectric coefficient (d33) of the films was measured using a piezometer system (test frequency: 110 Hz, test force: 0.25 N) at ambient temperatures. The constituent phases of the PVDF films were identified by X-ray diffraction (XRD) analysis. The flowchart of the fabrication process of the sensor sheets (artificial skin) is shown in Figure 1. Prior to the assembly process, a primer treatment of the silicone substrates (100 mm x 100 mm x 2 mm) was conducted in order to improve the adhesive property of the surface [3]. The wires of conductive adhesives with a silicone-based binder were formed on the silicone substrate by using a dispenser robot. Before the assembly process, the piezoelectric PVDF films were annealed at 60 or 125° for 1 h in an electric furnace. During the annealing process, the films were put between metal blocks in order to keep their planarity. When the curing temperature after the assembly process was set to above 100°, the PVDF films were always annealed at 125°. After formation of the wires and assembly of the PVDF films (4 mm x 4 mm x 28 μm), the conductive adhesives were cured under appropriate conditions. Finally, the sensor sheets were covered with a silicone rubber. The performance of the sensor sheet was checked using an A/D converter. 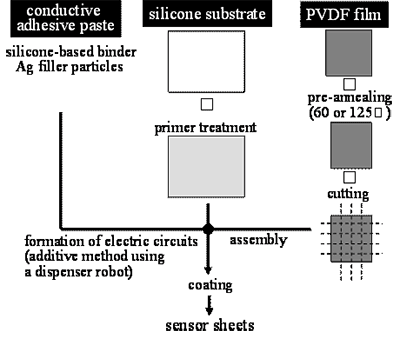 Figure 1. Flowchart of fabrication process of the sensor sheets (artificial skin). Results and Discussion Conductive Adhesives for Super-Flexible Wires and Interconnections Conductive adhesives composed of a silicone-based binder that are cured sufficiently on the silicone substrates can be elongated significantly, as shown in Figure 2. Figure 3 shows the variation in electrical resistance of the conductive adhesive specimens composed of a silicone-based binder cured at 100° for 5 h during the tensile test. The experimental result for a typical conductive adhesive with an epoxy-based binder is also shown in this figure. The epoxy-based adhesive specimen fractured when the elongation reached only a few %, due to its brittleness. By contrast, electrical conduction in the silicone-based adhesive specimens was observed until the elongation reached 100-180%. The silicone-based adhesives that are cured sufficiently are found to exhibit significant flexibility. 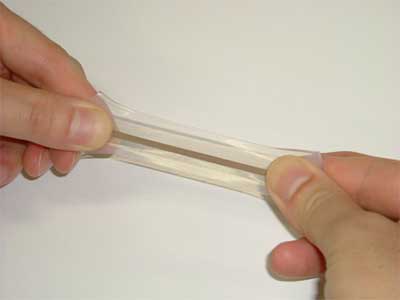 Figure 2. Photograph of conductive adhesive composed of a silicone-based binder. 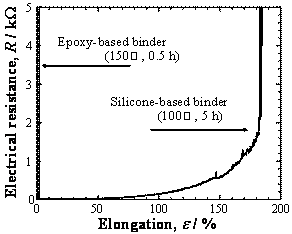 Figure 3. Variation in electric resistance of the conductive adhesives composed of an epoxy- and of a silicone-based binder during the tensile test. However, the conductive adhesives composed of a silicone based binder exhibit relatively high electrical resistivity compared to other conductive adhesives such as epoxy-based ones [3]. The electrical conduction in conductive adhesives originates from the formation of a percolation network of the filler particles. In order to increase the contact area between the filler particles, we used Ag particles with a flake shape, as shown in Figure 4. In addition, the electrical resistivity of the conductive adhesives depends on the internal stress that relates to the shrinkage of the adhesive binder [5]. In the case of silicone binders, relaxation of the internal stress is considered to prevent the electrical resistivity decreasing. Furthermore, the present authors considered a working hypothesis that the electric resistivity can be decreased by filling Ag nanoparticles between the flake particles. 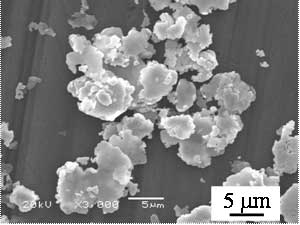 Figure 4. SEM micrograph of the Ag filler particles. In the present work, an Ag colloidal solution with non-reactive diluents was mixed into the adhesive paste containing the flake particles. Before the addition of Ag nanoparticles, the mass fraction of Ag flake particles in the adhesive paste was ~80 mass%. Figure 5 shows the electrical resistivity of the conductive adhesives cured at 130° for 1 h as a function of mass fraction of Ag particles. The resistivity of the conductive adhesive specimens apparently decreases with the addition of Ag nanoparticles. The resisitivity reaches a minimum value at ~80.5 mass% of total particle content. When the total particle content is below ~81 mass%, the conductive adhesive specimens exhibit significant flexibility. However, the mechanical properties of the conductive adhesive specimens deteriorate significantly when the total particle content is increased above ~81 mass% due to insufficient curing of the binder (inhibition of curing). In order to exactly clarify the effect of Ag nanoparticles on decreasing the resistivity, microstructural observation of the adhesives needs to be performed in detail. 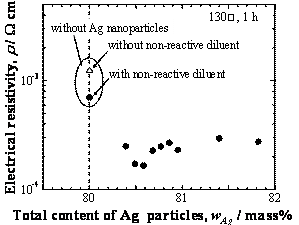 Figure 5. Resistivity of the conductive adhesives composed of a silicone-based binder before and after mixing Ag nanoparticles. Improvement of Thermal Stability of Piezoelectric PVDF Films In some cases, the curing temperature of the conductive adhesives is limited to a low temperature due to the heat-resistance of the components such as sensors but the conductive adhesives are required to be cured sufficiently. In the present case, the heat-resistance of the piezoelectric polymer films composed of PVDF is a serious problem. The piezoelectricity of PVDF films depends on the content of ferroelectric β-phase [4]. In order to obtain piezoelectric films containing the β-phase of PVDF, the films need to be drawn uniaxially or biaxially. In the present work, we used a uniaxially drawn film that had been pre-annealed at 60°. The XRD analysis indicated that the film contains the β-phase as the main constituent although a small amount of paraelectric α-phase coexists [3]. When the films are annealed above 100°, shrinkage of the films in the stretch direction occurs significantly (as shown in Figure 6) although it is to be desired that the curing process is performed at 130-150° from the viewpoint of productivity. During the curing process of the sensor sheet, the shrinkage of the films results in breaking wires and interconnections between the films and the conductive adhesives. Furthermore, Kolbeck [6, 7] has pointed out that the decay of the piezoelectricity of the PVDF films correlates with the thermal shrinkage of the films. In fact, the piezoelectric coefficient (d33) of the films decreases drastically when they are exposed to high temperature environments, as shown in Figure 7. 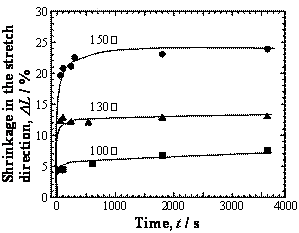 Figure 6. Shrinkage behavior of the PVDF films (pre-annealed at 60°) in the stretch direction during annealing process above 100°. 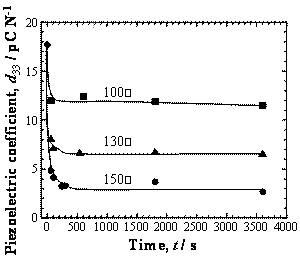 Figure 7. Variation in the piezoelectric coefficient of the PVDF films (pre-annealed at 60°) during annealing process above 100°. In order to resolve the problem of shrinkage and deterioration of the PVDF films, the films were annealed at 125° prior to the assembly process. Because the films already shrank during the pre-annealing process, they barely shrank in the subsequent curing process. Hence, we can avoid breakage of the wires and interconnections during the curing process of the sensor sheet even at 150°. Figure 8 shows the variation in piezoelectric coefficient of the films pre-annealed at 60 and 125° during the subsequent annealing at 150°. The films pre-annealed at 125° exhibit a low d33 value before annealing at 150°. However, the films pre-annealed at 125° exhibit higher d33 compared with the films pre-annealed at 60° after annealing at 150°. Therefore, pre-annealing at 125° of the PVDF films was employed in the present work, in order to avoid breakage of the wires and interconnections during the curing process. 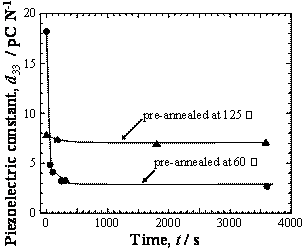 Figure 8. Variation in piezoelectric coefficient of the PVDF films pre-annealed at 60 and 125° during the subsequent annealing at 150°. Fabrication of Prototype Sensor Sheet A prototype sensor sheet was fabricated using the conductive adhesives modified with the Ag nanoparticles and the pre-annealed PVDF films. Curing of the sensor sheet was conducted at 130° for 1 h. The sensor sheet was successfully fabricated as shown in Figure 9. When we touched the sensor sheet, the piezoelectric response from each sensor was measured simultaneously using an A/D converter as shown in Figure 10. The deformation profile of the sensor sheets can be analyzed by the data processing (time integration of the piezoelectric response) of these piezoelectric responses [3]. 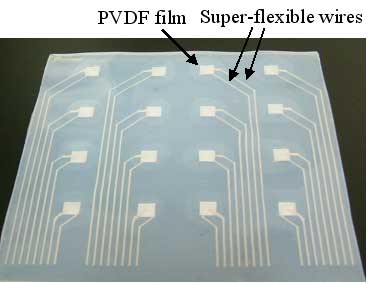 Figure 9. Photograph of the sensor sheet. 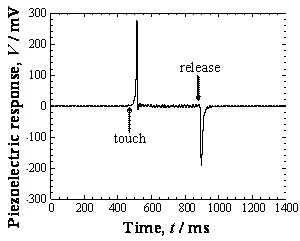 Figure 10. An example of the piezoelectric responses from the PVDF films embedded into the silicone sheet. In the present work, the problems that are related to the electrical properties of conductive adhesives for super-flexible wires and interconnects, and to the thermal stability of the piezoelectric polymer films, were examined. However, the material designs for conductive adhesives with super-flexibility (e.g., particle size distribution of the fillers, rheological properties of the pastes, fatigue resistance of the adhesive binder) must be reconsidered in order to form minute circuits with high reliability. The establishment of material designs for advanced conductive adhesives with super-flexibility will be one of the most important problems for the development of novel human-machine interfaces containing various components such as IC chips for data processing as well as in various sensor devices. Conclusions In the present work, super-flexible wires and interconnections were used to fabricate a prototype sensor sheet containing piezoelectric PVDF films on a silicone rubber. 1. The electrical resistivity of conductive adhesives with a silicone-based binder (super-flexible conductive adhesives) can be decreased by the addition of a correct fraction of Ag nanoparticles. However, the mechanical properties of the conductive adhesives are adversely affected when an excess fraction of Ag nanoparticles is added. 2. Pre-annealing of the PVDF films at 125° is effective in improving their stability in the temperature range 130-150°. 3. A prototype sensor sheet was fabricated successfully using the conductive adhesives with a silicone-based binder. Super-flexible wires and interconnections are expected to be a key technology for realizing novel human-machine interfaces installed in robots and related equipment. Acknowledgements This work was supported by a grant from the Kansai Bureau of Economy, Trade and Industry (METI-Kansai). The authors wish to acknowledge Mr. Y. Bando, Mr. Y. Kawahito, Mr. Y. Yoshino, Mr. S. Tsuda, and Mr. Y. Yamasaki for their cooperation in experiment and for many helpful suggestions. References 1. T. Someya, T. Sakurai, H. Kawaguchi and T. Sekitani, “Large-area, flexible sensors for electronic artificial skins”, Oyo Buturi (The Japan Society of Applied Physics), 73 (2004) 610-614. (in Japanese). 2. H. Shinoda, “Contact Sensing, a State of the Art”, J. Robotics Soc. Jpn., 20 (2002) 385-388. (in Japanese). 3. M. Inoue, Y. Yamasaki, K. Suganuma, T. Kawasaki, T. Rokuhara, T. Miyashita and H. Ishiguro, “Development of super-flexible wires using conductive adhesives for artificial skin applications in robots and related equipments”, Proc. Polytronic 2005 (5th International Conference on Polymers and Adhesives in Microelectronics and Photonics) (2005) pp. 90-95. 4. V. V. Kochervinskiĭ, “Piezoelectricity in Crystallizing Ferroelectric Polymers: Poly(vinylidene fluoride) and Its Copolymers”, Crystall. Reports, 48 (2003) 649-675. 5. M. Inoue and K. Suganuma, “Effect of curing conditions on the electrical properties of isotropic conductive adhesives composed of an epoxy-based binder”, Solder and Surface Mount Technology, 18 (2006) 40-46 A. G. Kolbeck, “Failuer Modes in Piezoelectric Poly(Vinylidene Fluoride)”, Polymer Eng. Sci., 22 (1982) 444-450. 6. G. Kolbeck, “Aging of Piezoelectricity in Poly(vinylidene fluoride)”, J. Polymer Sci., 20 (1982) 1987-2001. Contact Details |