The powder injection moulding (PIM) process is an efficient method for the high volume production of shaped components from powders. PIM is a derivative of polymer injection moulding and uses much of the same technology, along with batch sintering processes used in powder metallurgy and ceramic processing. The PIM Process In PIM, polymeric binders are pre-mixed with metal or ceramic powders. The mixture is heated in a screw-fed barrel and forced under pressure into a die cavity, where it cools and is subsequently ejected. The polymer is then removed and the component sintered to the required density, figure 1. 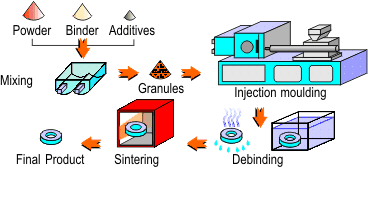 | Figure1. The powder injection moulding process. | The debinding stage, during which polymer is removed, can greatly influence the mechanical properties of the sintered component. A typical PIM injection moulding mix contains 35 to 50 vol% of polymer. This must be removed without causing swelling of the component, surface blistering, or the formation of large pores, which cannot be removed during sintering and so reduce the final density and compromise mechanical properties. Multicomponent binder systems, where the polymers are removed by solvents or degrade at different points of a thermal debinding cycle, have shown considerable potential for minimising debinding defects. Though the component shrinks whilst sintering it retains the shape of the mould. Providing this shrinkage is taken into account in the mould design, the final sintered component can be made to near-net shape. Tolerances of 0.2-0.3% of nominal dimensions can be achieved. Surface finish is typically 30 µm Ra, but this can be reduced to 15 µm Ra when finer powders are utilised. However, where special material properties are required, post sinter operations are sometimes necessary, for example in the production of hard surfaces on ductile Fe-2Ni and Fe-7Ni structural materials. Market Outlook In recent years this technology has moved from the laboratory to commercial production in the electronic, computer, medical and chemical industries. The PIM industry is forecasting an average growth rate of between 20 and 40% over the next few years, on present total sales of $200 million. It is estimated that the American market takes approximately 40% of PIM parts, Japan 30%, whilst Europe lags behind at 15%. This is reflected in the number of companies specialising in PIM - the US has twice the number operating in Europe. What is the PIM Process Suited to? PIM is especially competitive in the production of small intricately shaped components. Examples are as diverse as silicon carbide turbochargers and radial rotors for heat engines, alumina thread guides, rare earth magnet pole pieces for hard disk drives, and stainless steel gear wheels for electric tooth brushes. Raw Material Influences The maturing of this technology can be seen in two recent commercial developments - the production of metal and ceramic powders specifically tailored to PIM and the marketing of multicomponent binder systems which claim further reductions in defect rates and debinding times. A choice between commercial systems which allow catalytic debinding, thermal debinding or a mixture of thermal and solvent debinding is now available. The commercialisation of the process would be further improved if the component properties could be optimised during PIM rather than by post-production steps. This applies equally to those properties governed by the nature of the surface, e.g. wear and corrosion resistance, and bulk properties such as toughness. Two recent developments at Cranfield University have concentrated on these areas. Powder Co-Injection Moulding To produce components which are surface engineered in situ, powder co-injection moulding (PCM) has been introduced. Instead of a single barrel in which the powder and binder are heated, the system uses two barrels connected to a single nozzle via a pneumatic valve, fig 2. 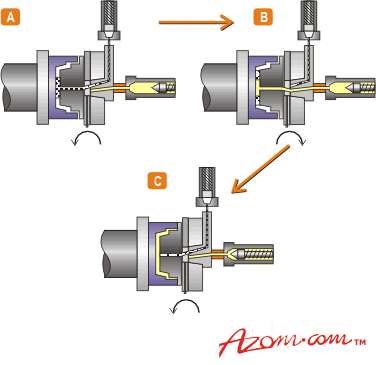 | Figure 2. Sequential injection process in powder co-injection moulding (PCM). (a) Injection of the skin, (b) injection of the core and (c) injection of a short shot to complete the skin. | Binder and powder are injected from the barrels sequentially so that in the mould the binder/powder mix from the first barrel forms the skin of the component, and that from the second barrel forms the core. A short shot of the skin material then completes the encapsulation of the core. The powders in each barrel can be completely different, e.g. the surface of a component can be something like 316L stainless steel and the core, carbonyl iron. The difference in the price of the two powders is a factor of three, allowing cost savings via the use of cheaper core materials. By varying the ratio of material injected from each barrel, the ratio of skin to core in the component can be altered, allowing the production of thick or thin surface engineered coatings. Further surface engineering can be performed by the addition of a secondary phase into the component surface. This is simply done by introducing it only into the binder/powder system in the first barrel. In the model system, an alumina particulate phase has been introduced to give improved wear resistance on the surface. Sintering rate control is crucial to the success of PCM. The core and skin of the sandwich must sinter at similar rates and at similar positions in the sintering temperature profile to avoid delamination. The mechanical keying of a faster sintering material to a slower one can reduce densification, giving the component a ‘built in’ tendency to equalise the densification rates. However, for materials with highly dissimilar sintering profiles, other methods of equalisation are required. The sintering behaviour can be altered by lowering the powder content of one mix and hence its green density, or by the addition of a second non-sintering composite phase. The liquid phase sintering of PIM materials is under investigation. Fibre Reinforced Ceramics The net shape manufacture of small ceramic components is also being achieved through PIM using thermoplastic-base binder systems. Particular attention is being given to the development of shop fibre reinforced ceramics. The addition of short fibres provides a potential mechanism for the improvement of properties such toughness, and the injection moulding process enables the control of both the distribution and orientation of the fibres. Component behaviour is influenced significantly by the fibre orientation distribution and it is therefore essential that this can be predicted. Work at Cranfield University (UK) has started to identify the relationship between fibre orientation distribution and mould geometry, processing conditions, fibre aspect ratio and composite formulation. Finite element flow analysis packages such as Moldflow have been developed to simulate the processing of short fibre reinforced thermoplastics, and this analysis capability has recently been used to predict successfully fibre orientation in injection-moulded ceramics which use a polypropylene-based binder system. The introduction of short fibres into ceramics retards densification, but the consolidation process must provide the necessary control of the fibre/matrix interfacial morphology. Following the successful debinding of the ceramic composite, full consolidation can be achieved by a sinter-HIP cycle. The initial low pressure sintering part of the cycle is designed to achieve a theoretical density of typically 92-95%, leaving closed porosity. This is followed by a high pressure sinter to achieve near full density. HIPing pressures of 200 MNm-2 or greater are now readily available. These can be used to offset the lower processing temperatures that are desirable in order to control the fibre/matrix interaction and ensure increased toughness. Conclusions With the increased awareness and use of PIM, major growth of this technology is envisaged. Factors that are presently limiting its application are currently being addressed, with the aim of increasing the cost-effectiveness of the process. To this end, the ability to manufacture components to net shape and. to surface engineer in a single process cycle by powder co-injection moulding, should provide further incentive for additional exploitation. |