Jan 21 2002
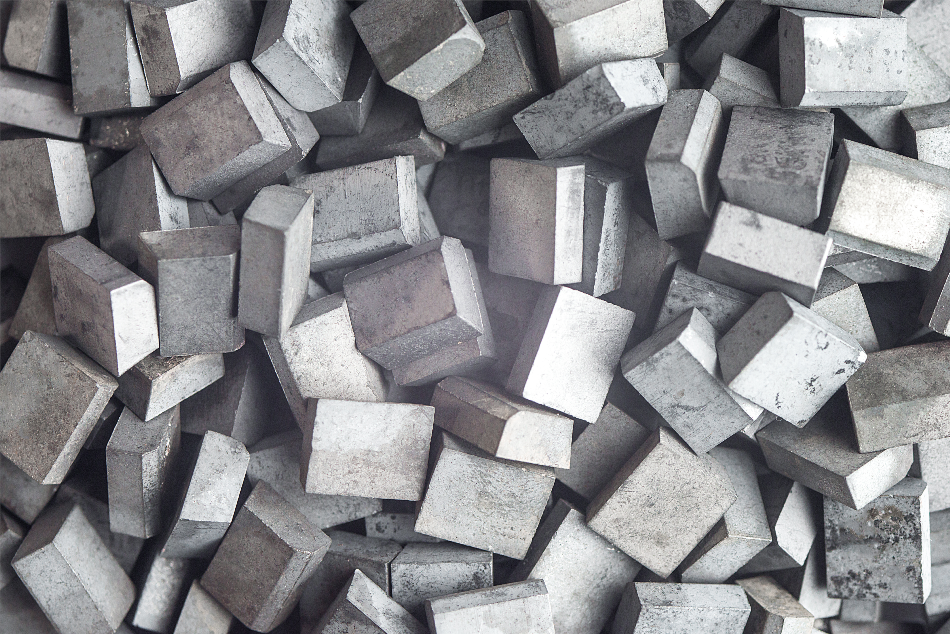
AkulininaOlga / Shutterstock
Scheele discovered “Tungsten” in 1781; however, it took 150 years more before the efforts of Scheele and his successors led to the use of tungsten carbide in the industry.
Cemented Carbide
At present, tungsten in the form of tungsten carbide is mainly used in the production of cemented carbide. Cemented carbide, (also referred to as hard metal), is a material created by “cementing” very hard tungsten monocarbide (WC) grains in a binder matrix of tough cobalt metal, using the liquid phase sintering process.
The combination of WC and metallic cobalt as a binder is a well-modified system not only relating to its properties, but also to its sintering behavior.
At high temperatures, WC is highly soluble in cobalt and the liquid cobalt binder also enables excellent wetting of WC. These properties lead to excellent densification during liquid phase sintering, and in a pore-free structure. Due to this reason, a material that integrates toughness, high strength, and excellent hardness are obtained.
History
The production of tungsten carbide can be traced back to the early 1920s when the German electrical bulb company, Osram, looked for substitutes to the costly diamond drawing dies used in the manufacture of tungsten wire.
These efforts led to the invention of cemented carbide, which was soon manufactured and marketed by numerous companies for several applications, where its high wear resistance was especially crucial.
The first tungsten carbide-cobalt grades were soon effectively applied in the cutting and milling of cast iron. In the early 1930s, pioneering cemented carbide companies introduced the first steel-milling grades which, besides cobalt and tungsten carbide, also contained carbides of tantalum and titanium.
By incorporating tantalum carbide and titanium carbide, the hot hardness, the high temperature wear resistance, and the oxidation stability of hard metals have been significantly enhanced. The WC-TiC-(Ta, Nb)C-Co hard metals are exceptional cutting tools for the machining of steel.
Compared to high-speed steel, the cutting speed improved from 25 to 50 m/minutes to 250 m/minutes for turning and milling of steel, which transformed productivity in a number of industries.
Soon afterward, the revolution in mining tools commenced. The first mining tools with cemented carbide tips extended the lifetime of rock drills by a factor of at least 10 when compared to a steel-based drilling tool.
Consumption
The consumption of cemented carbide has been continuous in all these applications from a yearly global total of 10 tons in 1930 to 100 tons around 1935; 1,000 tons in the early 1940s; 10,000 tons in the early 1960s, and up to approximately 30,000 tons at present.
The growth of metal cutting tools has been quite rapid over the last 40 years, having been considerably stimulated by better design and manufacturing methods, for example, the addition of indexable inserts in the 1950s and the invention of coated grades in 1970.
Coatings
The first coating was a thin layer (~5 µm thick) of titanium carbide developed using a chemical vapor deposition (CVD) process. It increased the service life of tools by a factor of 2 to 5. This method has since been enhanced by multilayer coatings, where layers of titanium nitride alumina and other materials have been added, which have further enhanced the service life by 5 to 10 times.
New Methods
However, coating and better design are just one side of the coin. Constant improvement of manufacturing methods and intermediates resulted in better performance of hard metals and opened new fields of applications. The advent of solvent extraction in tungsten chemistry—new methods in hydrogen reduction and carburization—enhanced the uniformity and purity of tungsten and tungsten carbide powder.
Correspondingly, new spray drying, milling, and sintering methods improved the properties and performance of the hardmetal. In particular, the continuous development of vacuum sintering technology and, beginning from the late 1980s, hot isostatic pressure sintering led to new quality standards in hardmetal.
Grain Size
The history of tungsten powder metallurgy, and particularly that of the hard metal industry, is marked by a progressively widening range of available grain sizes for processing in the industry; while, simultaneously, the grain size distribution for each grade of WC powder became increasingly narrower.
The most significant reason for this widening of the spectrum of available WC grades is that in addition to those differences attained by cobalt contents and certain carbide additives, the properties of WC-Co hard metals such as abrasion resistance, hardness, strength, toughness, and thermal conductivity can be extensively differed by means of the WC grain size.
The scale of the available WC grain sizes extended from 2.0 to 5.0 µm in the mid-1920s, during the early days of the hard metal industry. Presently, the grain sizes of WC powders used in hard metals range from 0.5 to 50 µm, or even 150 µm for certain special applications.
Applications
Based on a wide variety of grain sizes currently available, which include very hard and abrasion-resistant versions and very tough versions, hard metals can be manufactured for extensive applications in high-tech tools, mining tools, and wear parts as well as in numerous sectors of the engineering industry.
Mining and Cutting Tools
Mining and stone cutting tools have experienced rapid development, with better performance that has resulted in the increasing replacement of steel tools by cemented carbide tools, especially in the oil sector. In particular, the use of very coarse-grained hard metals is expanding in this application field.
Wear Parts
A large percentage of the tungsten volume in cemented carbide is currently used in wear part applications, where there is a wide variety of products from the very small (such as balls for ball-point pens) to large and heavy products, such as dies, punches, or hot rolls for rolling mills in the steel sector.
Many of these wear parts and mining tools are composed of straight WC-Co hardmetals without any incorporation of other carbides.
Both fine and ultrafine-grained WC hardmetals have become increasingly crucial today in tools for chipless forming, the field of wear parts, and cutting tools for non-ferrous alloys, cast iron, and wood.
The first submicron hardmetals were commercially introduced in the late 1970s and, since then, the micro-structures of such hardmetals have become very fine. The key interest in hardmetals with such finer grain sizes comes from the understanding that wear resistance and hardness increase with diminishing WC grain size.
Fine Drills
A unique application for fine or ultrafine WC hardmetals, involving huge amounts of cemented carbide, is in drills for drilling very fine holes in printed circuit boards for the electronics and computer industries. To that end, new cemented carbide compositions, based on very fine-grained carbide, have been launched.