Interview conducted by Mychealla RiceJun 21 2017
The composites industry is making incredibly advanced products but it is developing these products with technology that is behind the times. Dielectric Cure Monitoring is a solution that can bring this industry forward.
In this interview, Huan L. Lee, co-founder of Lambient Technologies, talks to AZoM about using Dielectric Cure Monitoring to prevent wind turbine failures, for building large composite structures for space applications, and many other applications.
What is dielectric cure monitoring (DEA) and how is it used now in Quality Assurance and Quality Control?
Dielectric cure monitoring came to be called DEA, meaning Di-Electric Analysis, in the late 1980s to place it in the family of standard thermal analytical techniques, which happen to also be identified with three letters: DMA—Dynamic Mechanical Analysis, DSC—Differential Scanning Calorimetry, TGA—Thermal Gravimetric Analysis, and others.
Dielectric cure monitoring measures the AC electrical properties of polymers, thermosets and composites to determine their cure behavior. Of the two properties—permittivity and resistivity—it turns out that resistivity (more specifically, frequency independent resistivity) is related to mechanical viscosity before gelation and modulus after gelation.
As a result the term ion viscosity was coined as an alternative to resistivity to emphasize the connection between mechanical viscosity and electrical resistivity.
Before I go on, I’d like to define QA/QC as testing of the curing behavior of resin or composite stock before it is made into an end product. Of course manufacturing of an end product involves quality control, but for our purposes it is convenient to identify QA/QC with materials testing.
Since ion viscosity does indicate cure state, many companies now use DEA to track how a material cures in routine QA/QC tests. For example, several manufacturers of sheet molding compound, or SMC, test each batch every day at a standard process temperature.
By recording the times of what we call Critical Points—minimum ion viscosity, peak slope of ion viscosity and a chosen slope to indicate cure time—they can monitor whether a batch cures according to specification.
.png)
Figure 1. Typical cure information from dielectric cure monitoring
If any parameter drifts outside set limits, a possible problem may be the cause. The company has gained visibility to the material’s cure and can investigate the source of the deviation.
Maybe the material is too old, the formulation is off or the mix ratio is incorrect. Maybe the door to the warehouse had been left open on a hot day in Texas. Consistency in behavior can be tracked statistically and DEA gives insight into cure and quality in real time and under real conditions—something that other thermal analytical techniques can’t do.
Given the growth in composite manufacturing, what areas could benefit from using dielectric cure monitoring?
Research and development can use dielectric cure monitoring to facilitate the study of new resin formulations. How does a development lab measure the cure time or cure rate of their thermosets? Today, the typical testing approach is labor intensive, crude, and inexact.
Typically users will laboriously cure materials to a certain point, then test with DMA or DSC to determine the degree of cure or glass transition temperature.
They then repeat this process with the material cured to a subsequent point. They repeat these steps many times to get a crude curve of the cure. By contrast, dielectric cure monitoring can do this in a single step, reducing time and effort, and in the end reducing cost.
Keep in mind that DEA doesn’t replace DMA or DSC. DEA is complementary to DMA or DSC, and many studies have shown correlations among all three methods.
Quality assurance/quality control processes can also benefit. A resin manufacturer can test outgoing material to assure its customers of a consistent product—one that cures as specified.
A company that takes these pure resins and adds fillers like carbon fibers or fiberglass, or one that makes prepreg, sheet molding compound (SMC), bulk molding compound (BMC) or epoxy molding compound (EMC), for example, can test their outgoing product to guarantee that it cures as specified.
DEA has unique advantages in manufacturing. Dielectric cure monitoring is the only thermal analysis technique that can be applied without change in both the lab and in a press or mold. Manufacturing benefits from having the ability to document cure in a way that can be traced directly back to laboratory results.
In addition, DEA gives the end user the ability to know how a part is curing. Imagine being able see the cure state of a wind turbine blade in real time.
With this capability, you could demold it when it is ready, not before and not after. If you guess and remove it from the mold too soon, it isn’t rigid enough to handle. If you leave it in the mold longer than necessary, you reduce throughput and efficiency.
.jpg)
Stockr/shutterstock.com
Why should companies migrate to incorporating dielectric cure monitoring in QA/QC and manufacturing?
I think the biggest benefit is increased efficiency and product consistency. The end result is cost savings.
A study conducted 25 years ago tested closed loop control of an SMC molding process. (Day, D.R. and Lee, H.L., “Analysis and Control of SMC Part to Part Variations,” Session 13-C of Proceedings of the 17th Annual Conference, Composites Institute, the Society of the Plastics Industry, Inc., Feb 3-6, 1992.)
This was an advanced concept then and I think it’s still an advanced concept now. In that study a dielectric cure monitor measured the cure state of a large part in its mold. When DEA determined that the part had reached a defined end of cure, the dielectric cure monitor issued a signal to automatically open the mold and eject the part.
Normally a timer would open the mold after 60 seconds, a period determined to guarantee all parts were cured to an acceptable point, even if some parts were cured past that point.
When DEA determined mold opening, the average press cycle time fell to 50 seconds, saving an average of 10 seconds compared to the timer. This reduction would have saved $70,000 per year per press in labor costs alone, not counting the increased productivity and throughput.
Even without closed loop control, manufacturing benefits from the use of DEA by being able to see problems in the cure as they occur, by having the additional data to solve those problems, and by having data to show that a part is curing as it should.
What is the usual migration path of DEA through R&D, QA/QC and manufacturing?
We’ve actually seen over the last thirty years the natural migration of DEA through these arenas. My original company was Micromet Instruments, which thirty years ago commercialized DEA technology developed at the Massachusetts Institute of Technology. Our customers for the first decade were almost exclusively involved in R&D and materials development. The early adopters were military labs and resin manufacturers.
Researchers had to show that dielectric cure monitoring could characterize cure of epoxies, polyurethanes, acrylics and other thermosets used in the manufacture of composites.
The continual publication of papers about DEA, even now, shows that dielectric cure monitoring is still a fertile line of research. Only after validation, supported more and more by results, is R&D able to recommend DEA for the next stage down the line.
The current growth in acceptance is now in QA/QC. As I mentioned earlier, I mean this to encompass testing of how stock materials cure, not testing of end product quality.
So QA/QC as I have defined it, concerns the routine, sometimes daily, use of dielectric cure monitoring for batch testing. In this way a company can confirm that feed stock such as pure resins, SMC, BMC, EMC, prepregs or filled resins, meet specifications for curing behavior before being made into the end product.
Identifying and fixing a cure problem earlier in the supply chain is easier and less expensive than later with the end product. For some companies the increased emphasis on statistical quality control, Six Sigma programs and the like is driving implementation of DEA in QA/QC.
What are the impediments to incorporating DEA in manufacturing?
I think manufacturing has the greatest new potential to use DEA, but it is also the hardest area for DEA to break into. This is because manufacturing engineers have already developed a process to make their product—and it works, or it wouldn’t have been implemented in the first place. The question is: “Can the process work better?”
Manufacturing managers understandably are reluctant to change a process that works well enough. Any change is usually incremental and comes only after much testing and validation—usually by someone else.
Having said that, companies in Japan are more receptive to incorporating DEA in manufacturing applications than in the United States or Europe.
The composites industry is making incredible advancements but the technologies used to test these materials are behind the times. How can dielectric cure monitoring bring this industry forward?
Products made with composites have an incredible strength to weight ratio compared to steel, for example. The existence of certain aircraft and spacecraft components, and wind turbine blades sometimes are only possible because of composites.
Despite sophisticated materials like sheet molding compound, epoxy molding compound and epoxy-graphite prepreg, to name a few; and manufacturing techniques such as filament winding, resin transfer molding and the like, cure testing is often stuck 50 years in the past.
A common method to determine the gelation time, often a proxy for cure time, is a simple stir test. This test uses a technician or machine to stir a sample of liquid resin with a stick.
.jpg)
HAKINMHAN/shutterstock.com
The technician records when the resin thickens enough to adhere to the stick or to form a string when the stick is lifted from the sample. Timing is very imprecise and the result highly depends on the amount of sample and the consistency and technique of the person stirring the sample.
Another crude way to determine cure time is the spiral flow test, which must be used for materials that are not fluid enough to stir, such as SMC, BMC or EMC. Here a mold with a spiral channel is heated to the test temperature.
The material under test is injected into the mold, where it flows until it hardens enough to stop moving. The distance the material has flowed indicates something about the cure time, but provides no information at all about the rest of the cure process or reaction.
This test requires a special mold as well as the machinery to inject the material under a fixed pressure.
Like the stir test, the spiral flow test can’t account for how cure behavior may change under real manufacturing conditions. Also, neither the stir test nor the spiral flow test can be used on prepregs, which are at the core of the many advanced products.
Dielectric cure monitoring, in contrast, uses simple sensors and a simple technique to show how a material cures. DEA can be used with liquid resins, filled materials and prepregs.
Data, like that represented schematically in Figure 1, indicates what happens during the entire cure, including the changing material viscosity and reaction rate. DEA is easy and reproducible, and can be used in the manufacturing environment as well as the lab.
In 2016, several wind turbine blades broke, suggesting better quality control is needed. How can DEA prevent this?
Without knowing how these wind turbine blades failed, I can only speculate. It is certainly possible that the problem was in some component like the hub that has nothing to do with the manufacture of the blade.
However the installation of turbines to tap wind energy is rapidly increasing, and there is great pressure to produce more and more blades with greater and greater length. Some wind turbine blades are 50 meters long or more.
Are the mold times being rushed to increase throughput? Are the post-cure times being rushed? Are there weak spots due to incomplete cure at some point along the length of the blade? I don’t know, but DEA can provide additional information about the state of cure in the actual manufacturing process.
In fact, newly available, cost effective dielectric cure monitors can be connected on a single communications line to measure material state every few meters along a large part such as a wind turbine blade. Certainly in the development of a cure process—that is, definition of time and temperature—and possibly in the manufacture of each blade—DEA provides valuable information to produce a consistent product.
.jpg)
3Dsculptor/shutterstock.com
How can commercial space ventures benefit from incorporating DEA in the manufacturing process? Can you give any examples?
Commercial space flight is an application much like aircraft manufacture, only much more demanding in requirements for light, strong materials. Phenolic-carbon fiber composites make up the heat shields for SpaceX’s Dragon capsules, and recently SpaceX revealed successful testing of a huge, 40-foot wide carbon fiber fuel tank planned for an ambitious Mars spacecraft.
During his September 27 International Astronomical Congress (IAC) talk Elon Musk of SpaceX specifically mentioned cure of carbon fiber prepreg as one of the challenges in making the tank.
Here is an example of a critical application where every means to assure success should be present during manufacture. For a large, single-piece component such as this fuel tank, non-uniform or incomplete cure could cause a weak spot. The surface area of a 40-foot, roughly spherical tank is about 5,000 square feet—that’s a lot of area for potential failure.
I’m sure that after cure SpaceX will inspect every square foot to check for defects, but using DEA during cure would provide documentation of correct processing that is traceable to a method validated in the lab. In addition, feedback about cure state would allow adjustment or correction of the cure in real time, possibly avoiding the scrapping of a part this large and expensive.
Of course for a part this large many dielectric sensors would have to be distributed across representative areas, but that would still be far less costly than throwing away a defective tank.
What is the future of DEA in manufacturing?
Companies making high value items like composite airplane wings and fuselages, or spacecraft components, seem more likely to investigate the use of DEA in manufacturing.
For them failure has catastrophic consequences in terms of human safety and material cost. Mitigating that risk is paramount, so I think aerospace firms will lead in the incorporation of dielectric cure monitoring in their processes.
Airbus is investigating or using DEA. So is Bombardier. Boeing has in the past, though I don’t know what they are doing now. I would like to see Scaled Composites, which makes the Virgin Galactic space craft, and SpaceX use DEA.
Where can our readers go to find out more?
More information about dielectric cure monitoring may be found at the web site for Lambient Technologies: www.lambient.com.
About Huan Lee
Huan Lee is an electronics engineer with more than 30 years experience designing instrumentation for the composites industry.
Huan has graduate degrees from the Massachusetts Institute of Technology, where he was part of a research group that worked on dielectric cure monitoring under contracts from NASA and other government agencies.
Huan is also a co-founder of Micromet Instruments, which first commercialized the technology developed at MIT.
In 2008 he co-founded Lambient Technologies LLC with Stephen Pomeroy to advance the use of dielectric cure monitoring for thermosets and composites.
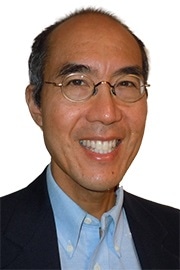
Disclaimer: The views expressed here are those of the interviewee and do not necessarily represent the views of AZoM.com Limited (T/A) AZoNetwork, the owner and operator of this website. This disclaimer forms part of the Terms and Conditions of use of this website.