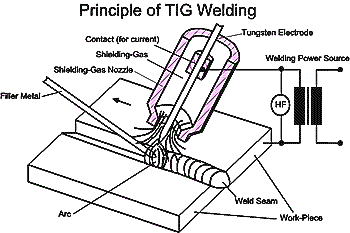 | Figure 1. Schematic of the TIG welding process. |
In the tungsten inert gas (TIG) welding process, an electric arc is struck between a refractory electrode made of tungsten and the work piece, while a shroud of inert gas, usually argon, shields the electrode and protects the molten pool against oxidation. Generally, a high frequency stabilised alternative current power source is used. The oxide film (alumina) is removed during the negative phase, while the positive phase ensures penetration and cooling of the electrode. TIG welding is suitable for metal thickness between 1 and 6 mm. Manual TIG Welding This process can be used for relatively thin components, small or circular welds. Depending on the weld preparation and the work piece thickness, it is possible to work with or without a filler. The filler can be introduced manually or half mechanically without current or only half mechanically under current. Compact and light TIG welding machines (less than 20kg) are available on the market. Easy to use, and to carry, they are ideal for small and localised repairs of commercial vehicles (breach in the skin of a tank, etc…). 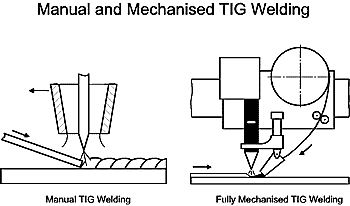 | Figure 2. The manual and fully mechanised TIG welding processes. | Automatic TIG Welding Here, the welding torch is automatically guided, and if a filler is used, it is fed automatically from a reel. This process is attractive for large production runs, i.e. for vehicle manufacturers, especially when there is no access to the back of the weld. There is also a TIG version where helium is used as shielding gas, which helps to achieve a high temperature in the arc. Here, direct current with straight polarity is used instead of alternative current. Thickness from 0.2 up to 10 mm can be welded. This process is strictly for automatic welding. |