Precision metal stamping is one of the most frequently used metalworking techniques employed by several industries to transform sheet metal into custom parts.
Progressive metal stamping uses a tool called a progressive die, which incorporates several stamping stations to carry out simultaneous operations on a strip of sheet metal. A feeding system unravels the strip from its coil, and it is then passed through each of the die’s various workstations until the final part is constructed.
This process uses a variety of materials and techniques, making it essential to consider all influencing factors and fully comprehend the options available before getting started.
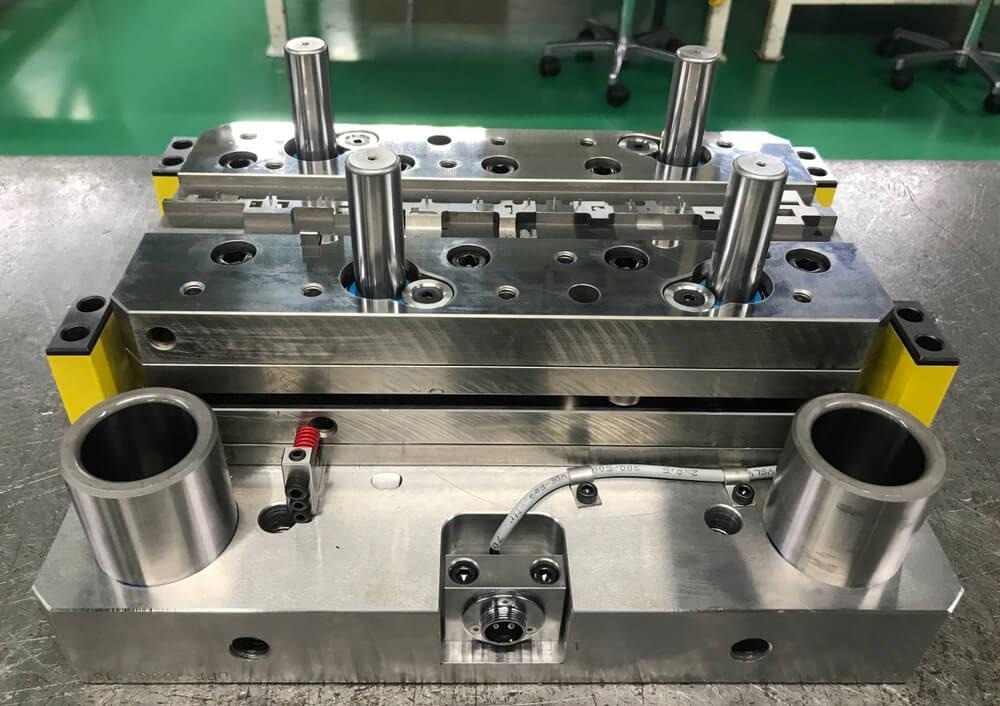
A progressive stamping die on the repair table. Image Credit: Ulbrich Stainless Steels & Special Metals, Inc.
Precision Metal Stamping Challenges
A Research and Markets report claims that by 2027 the global metal stamping market will have grown to $250 billion. With demand increasing and evolving tools and new materials for precision metal stamping, the industry must equally adjust to meet the demand. Today’s metal rolling techniques are more progressive than conventional hand processes, but manufacturers face recurring problems during production.
A recurring problem includes metal cracking, typically seen along the edges during hot and cold rolling. This may be due to uneven heating or rolling, but other metallurgical factors should also be considered.
Austenitic stainless steel is a meta-stable type, which will alter deformation, initiating a martensitic phase. Austenitic stainless steel also has a high cold hardening index (0.34% for SS). The martensite phase is brittle and prone to cracking.
Throughout plasticity deformation, with the increase of extension, the martensitic content will expand, and the residual stress will also be enhanced. The greater the relationship between residual stress and martensite content, the greater the residual stress, making it more likely that cracking will occur during processing.
Like most challenges that arise during precision metal stamping, the most significant way to negotiate cracking is to establish and tackle the root cause. Partnering with a precision reroll mill with metallurgical expertise can be a massive help for stampers in evaluating the root cause and resolving these issues.
Types of Steel Used for Precision Metal Stamping
Manufacturers can employ a range of metals in precision metal stampings. However, some processes and types of metals are likely to perform better during the precision metal stamping process or may be a more appropriate fit for a specific application use.
Hot rolled steel is cooled quickly after being roll-pressed at high temperatures, resulting in a rough surface. For applications that demand closer dimensional tolerances and accuracy, sheet metal is further processed at room temperature using cold finishing techniques.
When the metal is put under mechanical stress during the cold rolling process, it leads to a permanent change to the metal’s crystalline structure. This increases strength and typically leads to better corrosion resistance.
A cold-rolled stainless steel coil can be precision manufactured, enabling the metal to be fabricated within extremely tight tolerances. Precision stamping itself utilizes stamping dies to form metal. This process is generally performed at room temperature, making it a cold process.
When compared to hot-rolled steel, cold-rolled steel has characteristics that make it ideal for the ever-expanding needs of precision metal stampers. These are:
- Dimensional uniformity (width, thickness)
- Greater strength and hardness
- Precise edges and flatness
- Smooth finished surfaces
- Uniform and predictable material properties
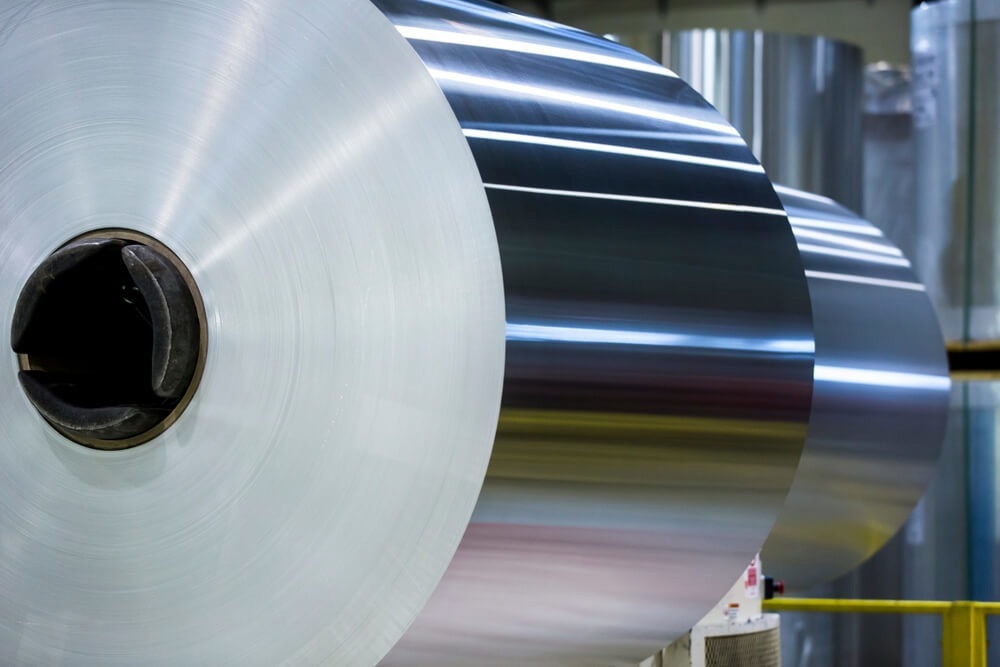
Image Credit: Ulbrich Stainless Steels & Special Metals, Inc.
When considering what metal to use, the benefits and limitations of each and the requirements for the part should be carefully considered. For instance, aluminum is softer and lighter than stainless steel, and a good conductor of electricity. But stainless steel has the capacity to endure much higher temperatures and be exposed to more corrosive environments.
On the other hand, titanium is light but much stronger and more durable than aluminum. This makes titanium well-suited for aerospace, military, and defense applications, where a high strength to weight ratio is needed.
Titanium is corrosion-resistant and also safe to use as a medical implant within the human body. Fundamentally, it comes down to matching the alloy and its properties with the specific requirements of the application use.
Alloys Used in Precision Metal Stamping:
- 300 Series Stainless
- Type 301
- Type 302
- Type 305
- 400 Series Stainless
- Grade 410
- Grade 420
- Grade 440A
- Precipitation-Hardening
- Titanium
- Grade 1
- Grade 2
- Grade 4
- Grade 9
- 6AL4V
Key Factors to Consider When Choosing a Material for Precision Metal Stamping
Some of the main factors to take into account when selecting a material for precision metal stamping are ductility and formability, tensile strength, machinability, and work hardening rate of a metal.
Ductility and Formability
Forming occurs at a certain point between the yield strength and tensile strength of the material. If yield is not surpassed, forming does not occur. However, going beyond the tensile strength results in a material fracture. The window between yield and tensile can be extremely small in higher-strength materials.
The grain size of a material is frequently applied to signal its formability, and consistent grain size is particularly desirable for forming operations. Grain size can be manipulated by a rerolling mill within an extremely close range by closely observing the temperature of the annealing furnace and the speed at which the strip moves through the line.
Tensile Strength
Tensile strength is the measurement of the force a material can endure without breaking. Some metals are naturally stronger than others, and the variability in strength depends on the component materials that comprise a metal alloy. The tensile strength of the metal chosen should be considered to ensure that it can endure the amount of force applied during manufacturing and application use.
Machinability
Machinability measures how easy it is to cut or shape the material. Properties that enhance a material’s performance generally reduce its machinability, meaning manufacturers should take into account the machinability of the metal selected after meeting other key requirements for your part.
A readily machinable material can be readily cut with a good finish, limiting costs. However, it is essential to select a material that meets part requirements, rather than selecting a machinable material.
Work Hardening Rate
During the working or stamping of metal, the temper changes, meaning the metal becomes harder or more brittle. The rate that this occurs is work hardening. Depending on how much the metal needs to be deformed and the amount of work performed during a particular operation, the metal may require annealing to reset its properties to avoid any cracking, breaks, and other material defects.
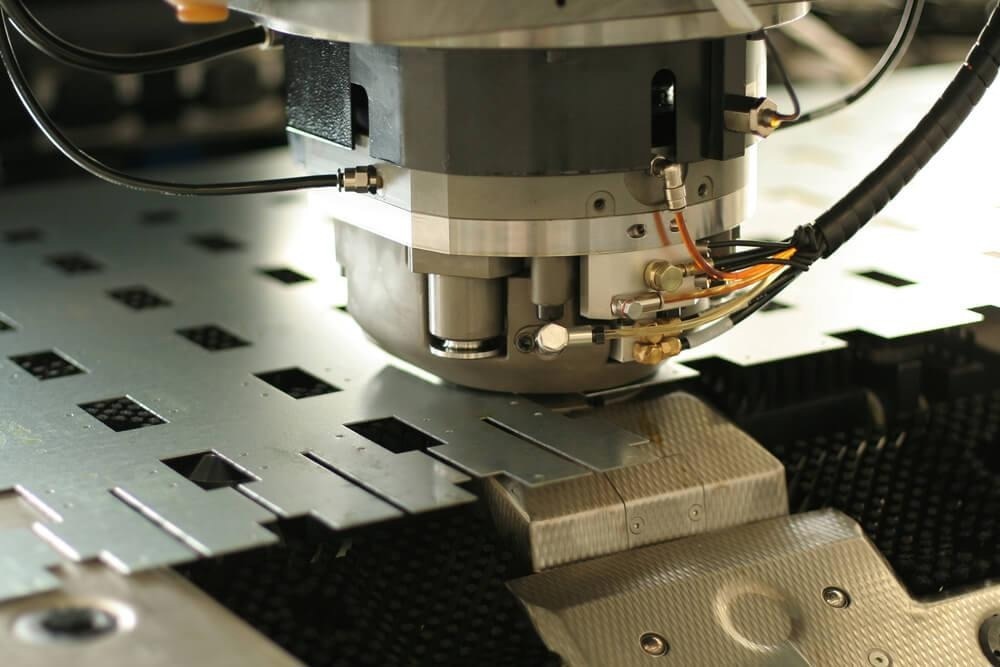
Precision CNC sheet metal stamping. Image Credit: Ulbrich Stainless Steels & Special Metals, Inc.
Forming Operations in Precision Metal Stamping
In precision metal stampings, manufacturers employ metal forming operations to fabricate parts from metal and metal alloys. It is extremely versatile and can be employed to fabricate complex, and intricate components with a high degree of accuracy and repeatability.
Deep-drawn parts are particularly strong due to the extreme compression limits exerted on the metal throughout the forming process. The fundamental structure of deep-drawn metals is usually highly compressed into a exceptionally hard crystalline structure.
A design guideline can help manufacturers make the right decision when choosing optimal materials and processes.
A list of the most common forming operations used in precision metal stamping is shown below:
- Beads
- Bulging
- Coining
- Curling
- Dimpling
- Embossing
- Extruding
- Flanges
- Holes
- Ironing
- Marking
- Necking
- Notches
- Ribs
- Threading
- Trimming
Options That Fit Your Needs
Engineer-to-engineer collaboration between stampers and precision re-rollers is extremely beneficial, particularly during the development of new products and processes.
Ulbrich’s metallurgical experts and wide alloy selection are able to match precision metal stampers with the appropriate material for a given application and specific equipment. Contact Ulblrich today and discover the solutions that could help you reduce scrap and die wear.
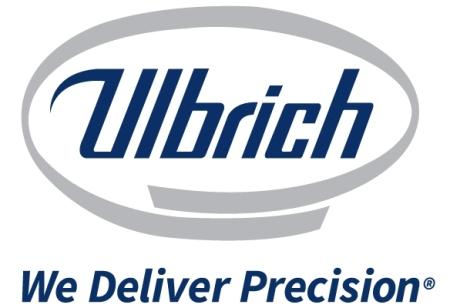
This information has been sourced, reviewed and adapted from materials provided by Ulbrich Stainless Steels & Special Metals, Inc.
For more information on this source, please visit Ulbrich Stainless Steels & Special Metals, Inc.