The surface finish of stainless steel impacts more than aesthetics as performance, reliability, and other important factors also come into play.
Regardless of the application or end-use of the stainless steel, the surface finish should be selected to best meet the requirements at hand. This is because, as well as possessing the right aesthetic look, the choice of finish impacts corrosion resistance and characteristics such as electrical properties. The finish impacts weldability, manufacturing operations, and contributes to various cost concerns.
Some applications, such as superconductor components or flexible metal hoses, require stainless steel to have a specific finish for the end-use product to function as designed.
It is also crucial to note that terminology referring to finish may vary from supplier to supplier. In this article, we outline the subtle differences between each finish to help better understand how suppliers may differ.
What is a Stainless-Steel Surface Finish?
Surface finish refers to the metal’s visual appearance. It is produced by various processing methods, including rolling, polishing, and blasting. These finishes extend from dull to bright and may include specific textures that may be applied mechanically for highly specialized applications.
Various factors can influence surface finish, such as the material thickness, production route, the surface finish of the rolls, cleanliness, and mechanical abrading.
The majority of melt mills can fabricate all sheet and strip finishes. While some finishes (BA and polished) demand specialized lines, most mills have access to these or a third-party processing partner. However, not all melt mills will address each customer's specific Ra (surface roughness) requirements, and a precision re-roller may be necessary.
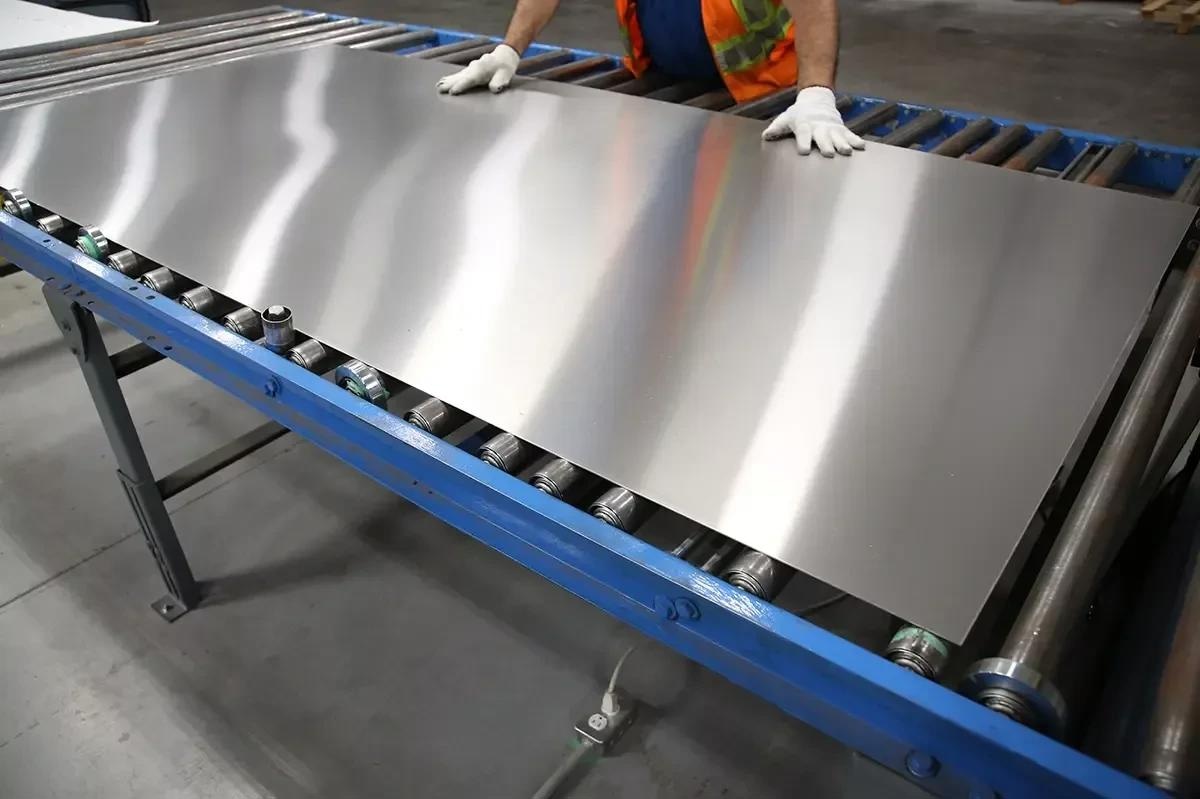
Image Credit: Ulbrich Stainless Steels & Special Metals, Inc.
What Are the Different Types of Stainless-Steel Surface Finishes?
Surface finishes are frequently identified by standard industry designations based on process routing (not appearance) and differ for sheet (greater than 24 in wide) and strip (less than 24 in wide). However, as mentioned before, some suppliers may use proprietary designations or different industry standards.
Ulbrich's surface finish designations are predicated on ASTM A480 specifications. An overview of the types of finishes available can be found on all of Ulbrich’s sheet products.
Mill Finishes
Whether hot or cold rolled, these finishes represent the fundamental supply condition for all stainless-steel sheet products. They are used universally for a number of different applications and serve as the origin point for mechanical polishing and other finishing processes. To optimize corrosion resistance, the majority are cleaned with acid (pickled) to eradicate any scale that forms during hot rolling and annealing (a bright annealed finish being the exception).
NO. 1 Finish
A No. 1 Finish is achieved via hot rolling. Annealing and pickling the material in acid is then carried out. This produces a dull finish and is normally used when a smooth decorative finish is not crucial, for instance, in high temperature applications.
NO. 2D Finish
A No. 2D Finish is created via cold rolling, followed by annealing and pickling the material in acid. The result is a smooth, non-reflective, and dull finish. This is ideal for deep drawing applications and is used for auto chemical equipment, exhaust components, and hardware.
NO. 2B Finish
A No. 2B Finish is cold rolled, annealed, and pickled. It is then subjected to a light temper pass utilizing polished rolls. This produces a smooth, somewhat reflective, and bright finish. It is a general-purpose cold-rolled finish for use in cookware, small tanks, and pharmaceutical equipment.
Bright Annealed (BA) Finish
A Bright Annealed Finish is cold rolled, then moved to a protective and controlled environment atmosphere for annealing to prevent scale forming during this process. This finish is not pickled in acid as a thin oxide film forms during annealing, preventing the need for pickling. This finish is used for trim appliances, surgical instruments, and cookware.
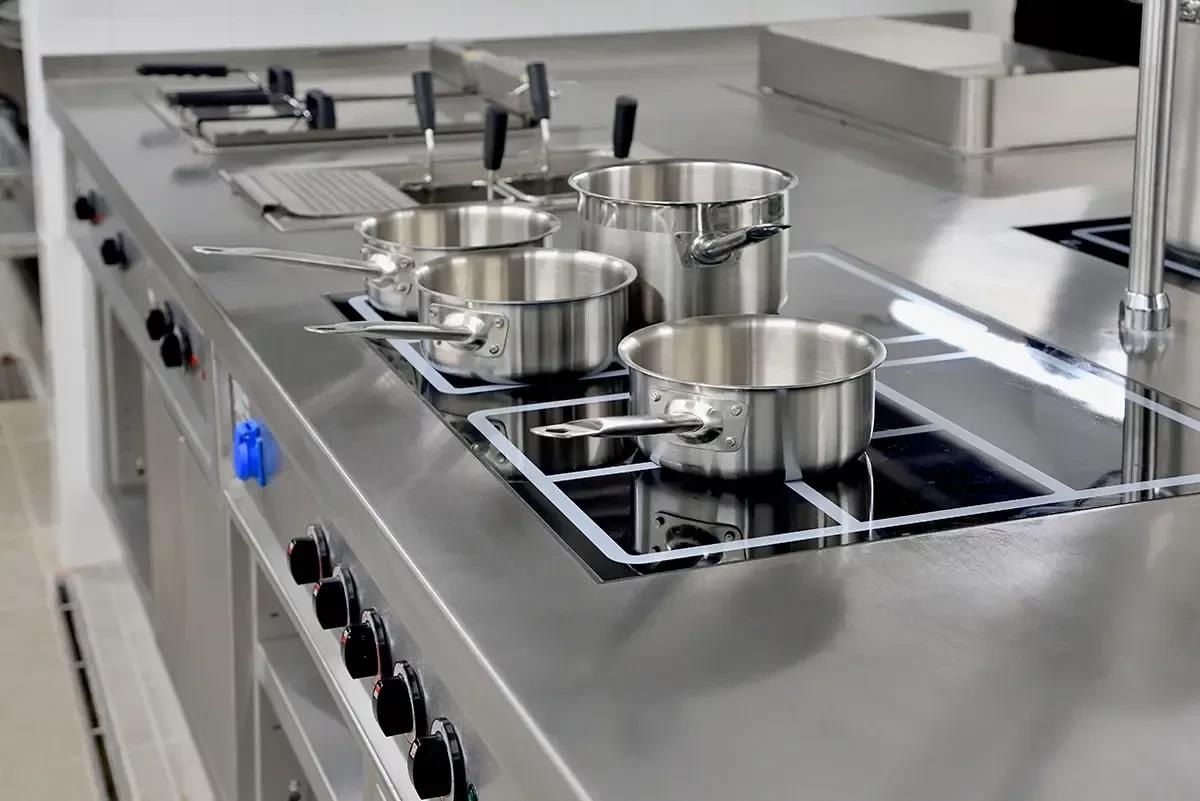
Image Credit: Ulbrich Stainless Steels & Special Metals, Inc.
Mechanically Polished Finishes
These finishes use abrasive materials that efficiently cut the steel's surface.
NO. 3 & NO. 4 Finishes
No. 3 and No. 4 finishes are achieved by polishing a No. 2B finish substrate mechanically. These finishes demonstrate uniform appearances that are created by applying an emery cloth belt when polishing. Each finish has a relative grit to generate the required surface texture.
These finishes are among the most commonly used in stainless steel.
Applications that make use of No. 3 finishes include architectural and food processing components. Applications in which No. 4 finishes are used include architectural wall panels, elevators, sinks, and restaurant equipment.
NO. 6 Finish
A No. 6 finish is achieved by Tampico brushing a No. 4 finish, but is less reflective than a No. 4 finish; it is typically dull and silver-white. This finish was found in common use on stainless steel architectural components until the 1980s but is used less frequently today.
NO. 7 Finish
A No. 7 finish is achieved by buffing a finely ground surface. The high luster finish has grit lines still visible on the final material. The result is an extremely reflective, almost mirror-like product. No. 7 finishes are commonly found on column covers, ornament trim, and wall panels.
NO. 8 Finish
By ATSM standards, a No. 8 finish is the most reflective of all finishes. This is achieved by polishing with successively higher grit abrasives and then buffing for a final mirror finish.
Dure to their high reflectivity, No. 8 finishes are found in a series of notable everyday applications, including press plates, signs, and wall panels. Most famously, Chicago’s “Bean” stainless steel sculpture’s highly reflective appearance was achieved with a No. 8 finish.
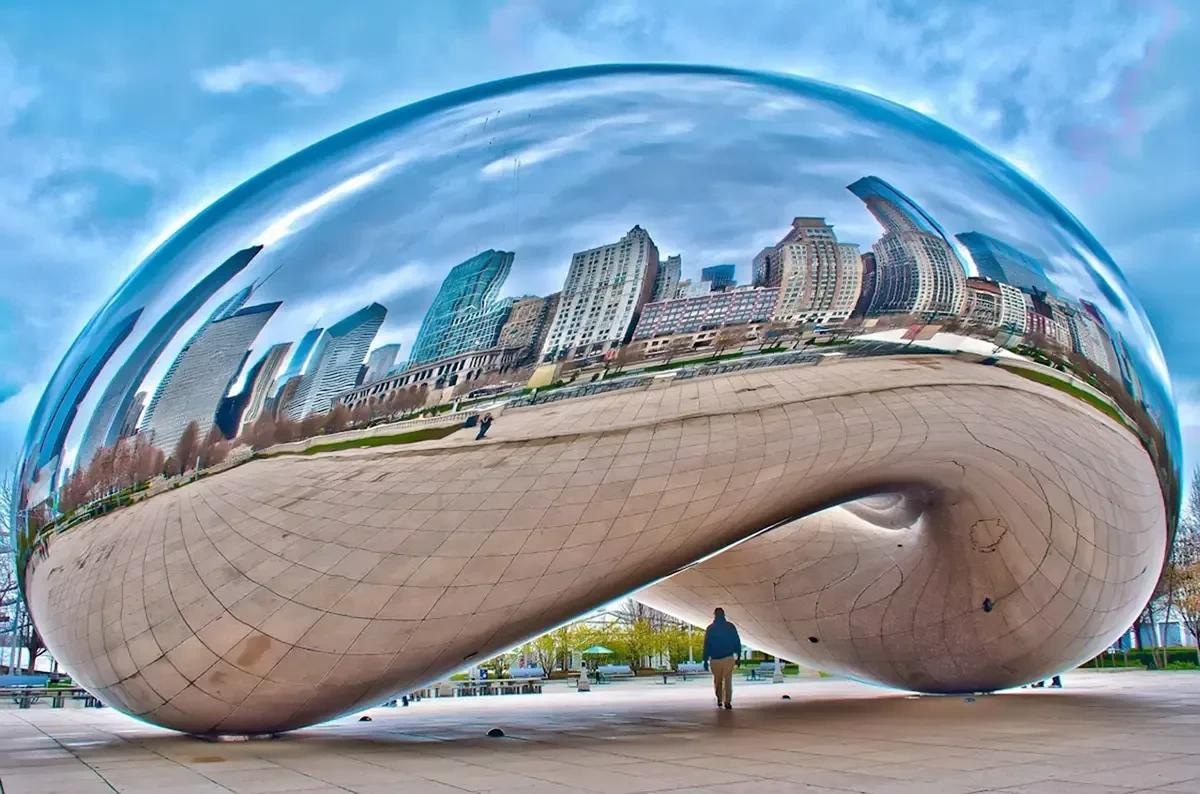
Image Credit: Ulbrich Stainless Steels & Special Metals, Inc.
Other Finishes
Custom Finishes
Custom metal surface finishes unlock characteristics that are not readily available in standard finishes. Engineers for advanced and new applications indicate the surface roughness in Ra or Rz (see below) that they need to achieve their objectives.
For custom surface finishes not mentioned in this article, contact Ulbrich to directly connect with a metallurgical engineer who can assist.
TR (TEMPER ROLLED) Finish
A TR finish is achieved when an annealed surface is cold rolled to acquire mechanical properties. The appearance can differ based on the alloy and the amount of cold work. Quarter hard, half hard, and full hard are commonplace examples of temper-rolled finishes. This finish is used frequently and is one of the largest categories of stainless steel that Ulbrich offer.
Architectural Finish
An architectural finish can be produced through a series of special finishes at the temper mill, special pickle processes, the final reduction stand, or a combination of all. These are usually agreed in advance between buyer and producer.
Abel Black
Abel Black™ stainless steel is produced using a proprietary coloring method that conserves its metallic texture (unlike painting or plating). Electricity and chemicals are used to produce an oxide film that interferes with light, making the stainless-steel surface appear black. Since the oxide film is amalgamated with the base metal, there is no likelihood of peeling while offering a greater durability and weather resistance than untreated stainless steel.
XL Blend S
XL Blend "S" is an innovative stainless steel finish. It has the capacity to repair surface damage, producing a clean, smooth, and uniform exterior. It is less reflective and less receptive to foreign substances due to the fine grain structure, resulting in a surface that is easy to clean and maintain. Common applications include food service appliances, escalators, and transportation.
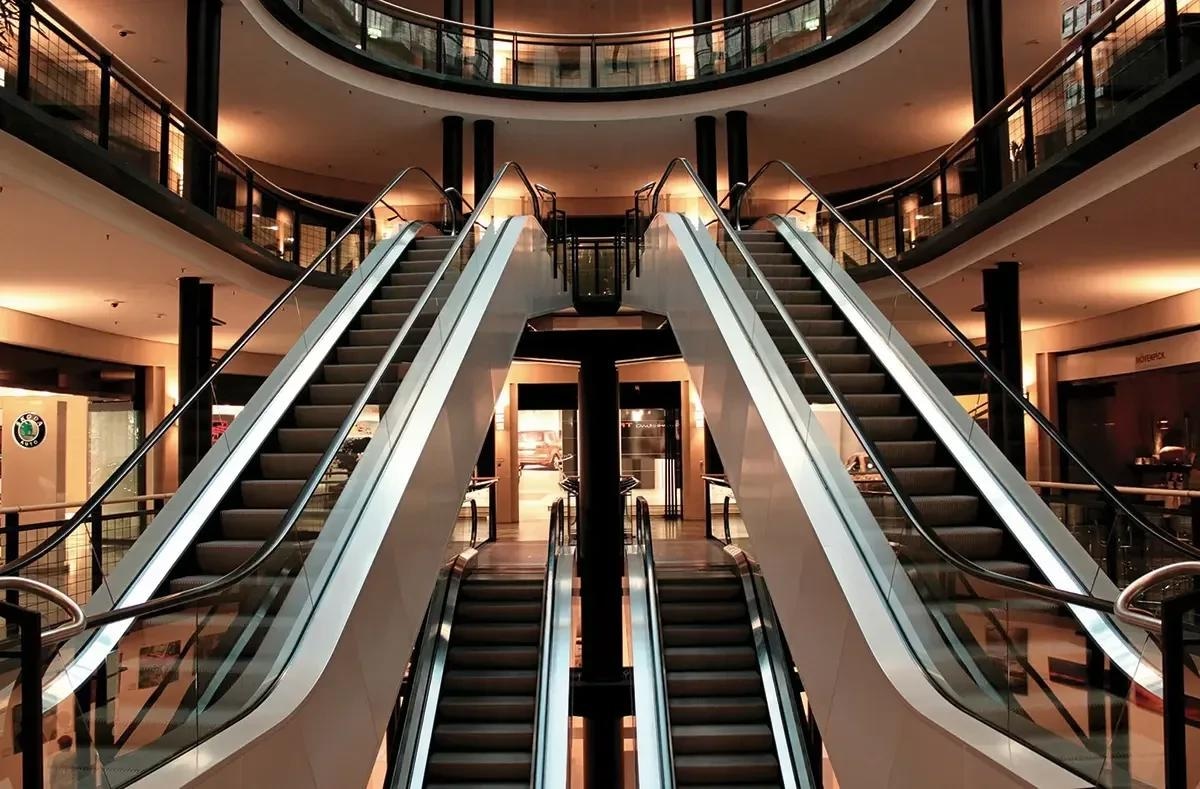
Abel Black and XL Blend S are both available from Diversified UIbrich!. Image Credit: Ulbrich Stainless Steels & Special Metals, Inc.
What is the Surface Roughness of Stainless Steel?
Surface roughness is a measure of the texture of a manufactured surface, and no discussion of surface finish would be complete without making reference to it. RA or Average roughness is most frequently applied in North America. It is the average of the peaks and valleys across a surface over a specific sampling length. Values are generally stated in microinches or micrometers.
Mean roughness depth (Rz) is most frequently applied throughout Europe and is the average of the highest peak to the lowest valley over five sampling lengths.
Surface roughness can have a significant impact on the performance and durability of the material and must also be examined closely and controlled.
Ulbrich offers a range of additional custom finishes to accommodate advanced and emerging applications, such as superconductors.
To find out more about which finish is right for your application, contact Ulbrich today and speak with a member of the metallurgy or product development team.
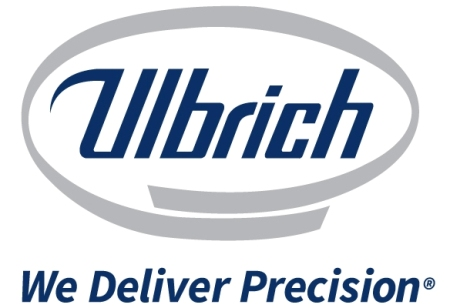
This information has been sourced, reviewed and adapted from materials provided by Ulbrich Stainless Steels & Special Metals, Inc.
For more information on this source, please visit Ulbrich Stainless Steels & Special Metals, Inc.