Introduction The polymeric precursor approach to ceramic synthesis has drawn the interest of many scientists since it has the advantage of easy of preparation using polymeric precursors at low processing temperatures [1-6]. The derived microstructure and chemical composition are strongly dependent on the composition of the polymer precursors. Polycarbosilane is the most typical polymeric precursor for SiC ceramic and has been widely used since the pioneering work done by Yajima et al. on SiC fiber [7-10]. In general, polycarbosilane is synthesized by thermal decomposition under high pressure of polydimethylsilane in an autoclave [1]. The preparation of polycarbosilane from polydimethylsilane is carried out by the “Kumada rearrangement” [1]. For the reaction, Si radicals have to be formed in the initial step of the reaction. The Kumada rearrangement of polydimethylsilane to polycarbosilane has been mostly studied by thermal decomposition at high temperature. However, this method poses significant operational problems such as generating gaseous by-products including CH4, Me3SiH, SiH4, etc. The gaseous byproducts create extremely high pressure inside the autoclave, which renders the operation inconvenient and unsafe. To overcome these problems in the thermal decomposition process, Yajima et al. adopted a catalytic process in which polycarbosilane was synthesized at normal pressure by adding small amounts of polyborodimethylsiloxane to polydimethylsilane as a catalyst [7]. Also, Hasegawa et al. developed solid acid catalysts for this reaction such as AlCl3, MnCl3, CrCl3, VCl3, TiCl3 and GaCl3 etc. [11]. However, using these catalysts, the molecular weight of the produced polycarbosilane is too low and doesn’t result in good spinnablity to produce pcs fiber. This might be due to the strong acidity of metal chloride catalysts. It is suggestive that an efficient solid acid catalyst for the Kumada rearrangement can be achieved if the solid acid catalyst is designed to have controllable acidity. In our study, a new method of synthesizing polycarbosilane at normal pressure is proposed using zeolite (Si/Al=30) as a catalyst. The synthesized polycarbosilane was used in drawing a pcs fiber by the melt spinning method and was pyrolyzed at 1200oC to obtain a SiC fiber. Experimental Preparation of Polydimethylsilane Polydimethylsilane was synthesized by the reaction of dimethyldichlorosilane with sodium metal in xylene solvent at 130oC [7]. Metallic sodium was chopped into small pieces and transferred into xylene under an inert atmosphere. After the sodium was entirely dispersed within the xylene solvent, dimethyldichlorosilane was added dropwise and refluxed for 7 h. After the reaction, the remaining sodium metal was removed by adding methanol. To remove NaCl and low molecular weight polydimethylsilane, the solid product was washed thoroughly with deionized water and acetone. The final product of white precipitate was dried under vacuum. Preparation of ZSM-5 Catalyst ZSM-5 catalyst (Si/Al=30) was synthesized hydrothermally using tetrapropylammonium bromide (TPABr) as a structure-directing agent with a chemical composition 0.1TPABr: 0.1Na2O: 0.017Al2O3: 1.0SiO2: 35H2O [12]. The gel was transferred into a stainless-steel autoclave and heated at 150oC for 6 days without stirring. The resultant solid product was recovered by filtration, washed with deionized water and dried at 100oC. The sample was calcined in ambient air at 550oC for 12 h to remove the template. To prepare the proton form of ZSM-5, the calcined sample was ammonium ion-exchanged by refluxing in 1.0 M NH4NO3 solution for 12 h. After refluxing, the sample was filtered, dried and calcined in air at 500oC for 4 h. Preparation of Polycarbosilane For the preparation of polycarbosilane, the mixture of 20 g of polydimethylsilane and 0.1 g of catalyst was loaded into a reaction vessel. After purging the sample with nitrogen gas, the temperature was increased to 350oC and maintained for 6-10 hours, and the temperature was further increased to 400oC and held constant for 6-10 hours. After the reaction, either yellow viscous solid or white-brown solid product was obtained depending on reaction time. The yellow viscous solid product was dissolved in hexane and filtered to remove insoluble products, and the solvent was evaporated using a rotary evaporator. A yellow-brown viscous product was produced. It was heated under a nitrogen atmosphere at 250oC for 30 min to remove low molecular weight polycarbosilane. However, white-brown solid product was not dissolved in hexane. Characterization Solid state 29Si MAS NMR spectra were obtained using a Varian Unity Inova 200 MHz spectrometer. Fourier transform infrared spectroscopy (FT-IR) spectra were obtained using a FTS-175C spectrometer in the range of 4000 to 400 cm-1. Molecular weight distribution of polycarbosilane was determined by Gel Permeation Chromatography (Waters) with a Styragel column using tetrahydrofuran as a solvent. A polystyrene standard was used for calibration. Thermal decomposition of the polycarbosilane up to 1200°C was measured by a STA-MS-Skimmer Thermal Gravimetric Analysis (TGA) instrument under a nitrogen atmosphere. UV spectra were obtained using a drift UV method (JASCO V550 model). The obtained SiC fiber was observed by SEM and TEM (JEOL 4010). The crystallinity of the fiber was also checked by X-ray diffraction after crushing the fiber into powder form. Results and Disscusion Preparation of Polycarbosilane Using Catalysts The results of the catalytic reaction of polydimethylsilane in the presense of ZSM-5 (Si/Al=30) and AlCl3 as catalysts are presented in Table 1. ZSM-5 (Si/Al=30) shows better catalytic activities than AlCl3 under atmosphere pressure for Kumada rearrangement of polydimethylsilane into polycarbosilane. The initial yield of polycarbosilane from ZSM-5 (Si/Al=30) and AlCl3 reaches 50% and 35% respectively. To remove polycarbosilane of low molecular weight, yellow-brown viscous products were heated under a nitrogen atmosphere at 250oC for 30 min. Then, the yield reduced to 45% for ZSM-5 and 9% for AlCl3 after purification. The reduction in yields is due to evaporation of the polycarbosilane of low molecular weight and confirms that polycarbosilane prepared using AlCl3 as a catalyst contains a high proportion of low molecular weight material. Although the exact role of the ZSM-5 catalyst is not fully understood, it can be speculated that the acid strength of the hydroxyl group (Brǿnsted acid site), present on the surface of ZSM-5 crystallite, is adequate to catalyze the polydimethylsilane to form polycarbosilane of high molecular weight. Table 1. Preparation of PCS using various catalysts. | ZSM-5 (Si/Al=30) | Yellow viscous solid | 50 % | 250oC, 0.5h | 45 % | AlCl3 | Yellow viscous solid | 35 % | 250oC, 0.5h | 9 % | The results for various synthesis conditions in the presence of ZSM-5 (Si/Al=30) as a catalyst are presented in Table 2. Samples T1 and T2 produced using a relatively long reaction time were the white- brown solid. Average molecular weight (Mn) was higher than 2,500 and the samples were not dissolved in hexane. Melt spinning of these samples was not feasible because the samples did not melt even up to 350oC. Meanwhile, samples T3 was viscous and yellow-brown at the beginning. It was heated under a nitrogen atmosphere at 250oC for 30 min to remove polycarbosilane of low molecular weight. Purification of T3 samples enabled us to do melt spinning at 210oC to form continuous pcs fiber. Table 2.Preparation of PCS using various synthetic conditions. | KICET-T1 | 350oC, 10 h 400oC, 10 h | 2,800 | White-brown solid not melted at 350oC | KICET-T2 | 350oC, 7 h 400oC, 7 h | 2,900 | White-brown solid not melted at 350oC | KICET-T3 | 350oC, 6 h 400oC, 6 h | 2,430 | Yellow viscous product Melt spinning at 210oC | 29Si MAS NMR Analysis Figure 1 shows the 29Si MAS NMR spectra of the products in terms of the reaction time of polydimethylsilane in the presence of ZSM-5 catalyst. The peaks at 0 and -17 ppm are assigned to SiC4 and SiC3H, respectively. The SiC4 peak shows a shoulder at about 7 ppm, suggesting the presence of C3SiO species [8]. This result might be due to the oxidation of some SiC4 species by oxygen introduced during the reaction process. Figure 1 also exhibits small peak at –37 ppm for residual polydimethylsilane. 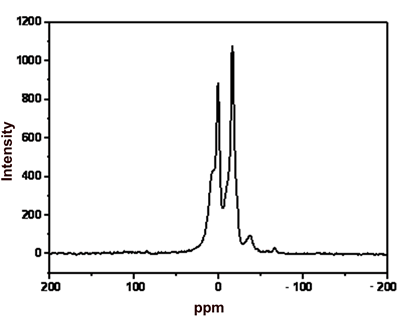 | Figure 1. 29Si MAS NMR data on polycarbosilane (KICET-T3). | FT-IR Analysis The formation of the polycarbosilane is also confirmed by FT-IR spectrometery. As shown in Figure 2, a FT-IR spectrum of the polycarbosilane synthesized by the catalytic reaction exhibits vibration bands corresponding to the functional groups of polycarbosilane. In particular, the band at around 1035 cm-1 is very strong and is assigned to CH2 bending vibration in the Si-CH2-Si group, indicating the formation of polycarbosilane. FT-IR data of prepared polycarbosilane are in agreement with those reported in the literature [8]. 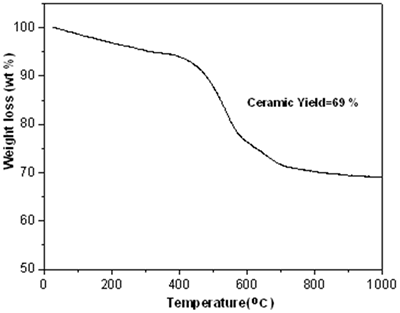 | Figure 2. FT-IR data on polycarbosilane (KICET-T3). | TGA Analysis The TGA curve (Figure 3) exhibits a large amount of weight loss up to 700oC. This means that the organic groups of the polycarbosilane decompose in this temperature range. The weight loss of the polycarbosilane occurs in two steps, which are below and above about 400°C respectively. Up to 400oC, the gradual weight loss, which is relatively small, may be due to the desorption of low molecular weight polycarbosilane. The rapid weight loss above 400oC is due to pyrolysis of polycarbosilane to SiC ceramic (Figure 4). The ceramic yield calculated from TGA is about 69 %. 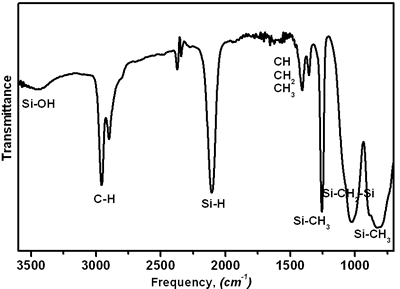 | Figure 3. A data on polycarbosilane (KICET-T3). | 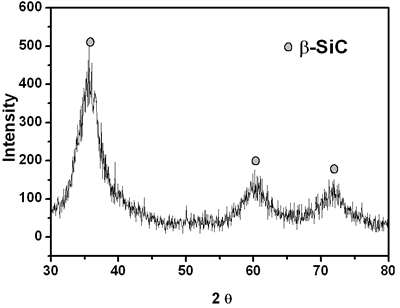 | Figure 4. X-ray diffraction pattern of crushed SiC fiber after heat treated at 1200oC for 1 h in an argon atmosphere. | Conclusions In conclusion, we report the synthesis and characterization of polycarbosilane that is a suitable precursor for SiC fiber in the presence of a ZSM-5 catalyst. ZSM-5 can be a very effective catalyst for synthesizing polycarbosilane at 350oC under normal pressure. The acidic strength of the hydroxyl group (Brǿnsted acid site), which is present on the surface of the ZSM-5 (Si/Al=30) crystallite, is adequate to catalyze the conversion of polydimethylsilane to polycarbosilane. The resultant polycarbosilane, providing a good spinnability, is a suitable precursor for melt spinning to produce SiC fiber. Acknowledgements Financial support of this work was provided by the Next Generation Project of the Ministry of Commerce, Industry and Energy, Korea. The authors would like to thank Dr. Duk-Young Han of the Korea Basic Science Institute, Seoul Branch, for his assistance in data collection from the samples using a Solid NMR, 200B instrument. References 1. M. Birot, J. P. Pillot and J. Dunogues, “Comprehensive chemistry of polycarbosilanes, Polysilazane, and Polycarbosilazanes as Precursors of Ceramics”, Chem. Rev., 95 (1995)1443-1447. 2. P. P. Loh, X. Bao, M. R. Nangrejo, and M. J. Edirisinghe, “Coatong with amorphous silicon carbide using polymeric precursors”, J. of Materials Science Letters, 19 (2000) 587-589. 3. P. P. Loh, X. Bao, M. R. Nangrejo and M.J. Edirisinghe, “Preparation of silicon carbide foams using polymeric precursor solutions”, J. of Materials Science Letters, 35 (2000) 4365-4372. 4. F. XIaolin, F.Chunxiang, S. Yongcai and L. Xiaodong, “Preparation of Si-C-O-N-B ceramic fibers from polycarbosilane”, J. of Materials Science Letters, 18 (1999) 629-630. 5. P. Colombo and M. Modesti, “Silicon oxycarbide ceramic foams from a preceramic polymer”, J. of Am. Ceram. Soc., 82 [3] (1999) 573-578. 6. I. Hasegawa, Y. Fukuda and M. Kajiwara, “Inorganic-organic hybrid route to synthesis of ZrC and Si-Zr-C fibres”, Ceram. Internationalc, 25 (1999) 523-527. 7. S. Yajima, Y. Hasegawa, K. Okamura and T. Matsuzawa, “Development of high tensile strength silicon carbide fibre using an organosilicon polymer precursor”, Nature, 273 (1978) 525-527. 8. H.Q. LY, R. Taylor, R. J. Day and F. Heatley, “Conversion of polycarbosilane (PCS) to SiC-based ceramic part I, Characterization of PCS and Curing product”, J. Mater. Sci., 36 (2001) 4037-4043. 9. T. Shimoo, I. Tsukada, M. Narisawa, T. Seguchi and T. Okamura, “Change in Properties of Polycarbosilane-Derived SiC Fibers at High Temperatures,” J. Ceram. Soc. Jpn., 105 [7] (1997) 559-563. 10. S. T. Taylor, Y. T. Zhu, W. R. Blumenthal, M. G. Stout, D. P. Butt and T. C. Lowe, “Characterization of Nicalon Fibres with varying diameters: Part I Strength and Fracture Studies,” J. Mater. Sci., 33 (1998) 1465-1473. 11. Y. Hasegawa, T. Kobori and K. Fukuda, “Organosilicon Polymer and Process for Production Thereof”, U.S. Pat. No. 4,590,253 (1986). 12. R. Kumar, P. Mukherjee, R. K. Pundey, P. Rajmohanan and A. Bhaumik, “Role of Oxyanions as Promotor for Enhancing Nucleation and Crystallization in the Synthesis of MFI-type Microporous Materials”, Microporous and Mesoporous Mater., 22 (1998) 26-31. Contact Details |