Introduction The large change of resistivity of a magnetic conductor under application of an external magnetic field caused by spin-dependent scattering of conduction electrons is called Giant Magnetoresistance effect (GMR). This effect was first observed in multilayered structures in 1988 [1] and later in magnetically heterogeneous granular alloys in 1992 [2,3]. These alloys consist of nano-particles of ferromagnetic (FM) phase (Fe, Co or Ni) embedded in non-ferromagnetic (NF) matrix (Cu, Ag or Au) [4]. Under the application of an external magnetic field the orientation of magnetic moments of the ferromagnetic particles are changed and the magnetic moments are aligned parallel. It leads to the change of scattering mechanism of conduction electrons and results in decrease of resistivity of the magnetic conductor. GMR effect observed in granular Cu-3d alloys is a simple instance of spintronics where spins of electrons are used for controlling the conductivity. Various theories and models have been proposed to explain the magneto-transport properties of these structures [5]. According to these theories the structural parameters such as the size and the concentration of magnetic particles, the average distance between them, the electron mean free paths, the interface of the FM and NF phases are the factors controlling the magnitude of GMR effect [6]. The predominant contributions coming from RKKY or dipole-dipole interactions are determined by the distribution of magnetic particles [7]. In this paper the heat treatment conditions for obtaining high GMR effect of the melt-spun Cu-Co alloys are studied. The samples with high GMR ratios are used for making GMR sensors for magnetic measurement. Experimental Metastable Co10Cu90, Co8Cu92 and alloys Co20Cu80 were rapidly solidified by using planar flow casting in air. The samples in the shape ribbons of about 25 μm in thickness were obtained. The ribbons were annealed in a vacuum at the temperature range of 400 - 550˚C for 30 - 60 min. The magnetoresistance effect of the samples was measured by 4-point in a magnetic field up to 1.3 T generated by controllable electro-magnets. The GMR ratio (%) is described as:   Where RH and RH=0 are the resistance of the sample with and without application of an external magnetic field. Results and Discussion The hysteresis loops of the samples measured at room temperature are shown in Figure 1. The magnetization is far from saturation for the field of 1.3 T (Figure 1, curves a and b). It indicates the superparamagnetic behavior of the samples consisting of nanosized ferromagnetic particles. The magnetic saturation related to the ferromagnetic property is clearly evidenced in the sample annealed at higher temperature of nearly 550oC (Figure 1, curve c) [8] and it is explained by intensive precipitation of Co from the homogeneous Cu-Co alloys while increasing annealing temperature. The influence of annealing temperature on precipitation of Co in Cu-Co alloys was investigated by X-ray diffraction technique and reported in [9]. 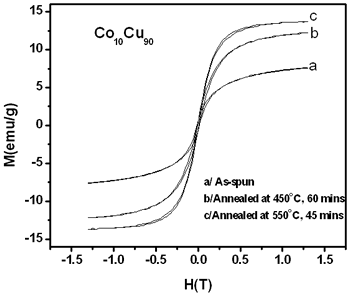 | Figure 1. The magnetization curves of Co10Cu90 samples annealed at different temperatures. | GMR ratios of the Co10Cu90 samples are shown in the Figures 2 (a) and (b). Before annealing the sample shows a small GMR ratio of about 2.0% under an applied field of 1.3T. The GMR ratio of the ribbons after annealing drastically enhances. 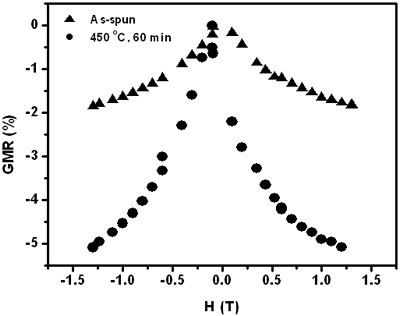 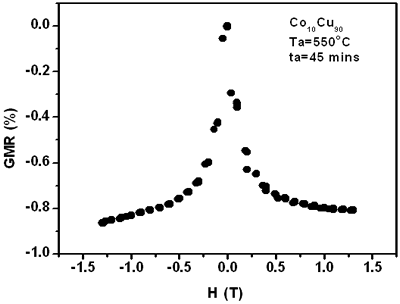 | Figure 2. GMR ratio of Co10Cu90 samples vs Magnetic field. (a: as-spun and annealed at 450oC, 60 minutes samples, b: annealed at 550oC, 45 minutes sample). | The maximum GMR ratio of 5.5% is obtained for Co10Cu90 sample annealed at 450oC for 60 min. Upon further increase of the annealing temperature, the magnitude of ΔR/R decreases due to the growth of Co particles (Figure 2 (b)). The GMR ratio monotonously decreases from 5.5% to nearly 1.0% with the increase of annealing temperatures from 400oC to 550oC for 60 min (Figure 3). After annealing at higher temperature (550oC) the GMR curve becomes sharper, that is, GMR ratio is very sensitive to the change of the field although the magnetoresistance decreases [9] (Figure 2(b)). 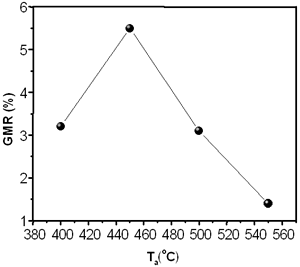 | Figure 3. Temperature dependence of GMR ratios of Co10Cu90 samples annealed for 60 min. | The dependence of GMR ratio on the annealing time is investigated and shown in Figures 4-6. The GMR ratio significantly changes from 2 to nearly 5% with increase of annealing time from 30 to 45 min for the Co8Cu92 sample annealed at 450°C. For both Co10Cu90 and Co8Cu92 samples, there is optimal annealing time corresponding to maximum GMR ratio (Figure 5). The time dependence of GMR ratio is related to the change of the microstructure of the samples (the size of the Co particles and their distribution in the Cu matrix). The maximum of the GMR ratio reaches 5.5% after annealing at 450oC for 60 min (Figures 5 and 2(a)). In this case, it is probably assumed that the sample has a higher surface-to-volume ratio that acts as the spin-dependent scattering centers of conduction electrons. 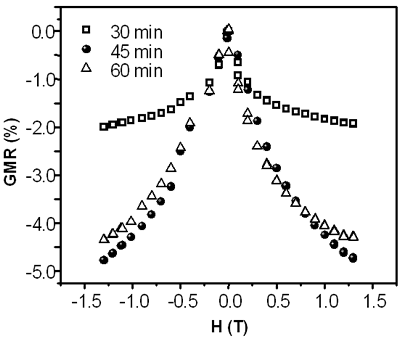 | Figure 4. Time dependence of GMR ratios of Co8Cu92 samples annealed at 450oC. | 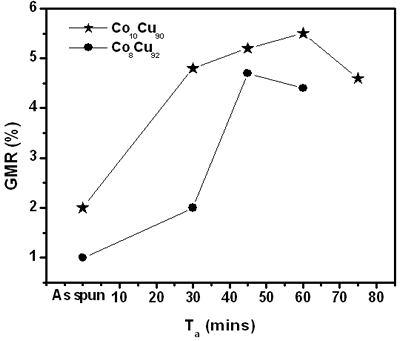 | Figure 5. Time dependence of GMR ratios of Co10Cu90 and Co8Cu92 samples annealed at 450oC. | 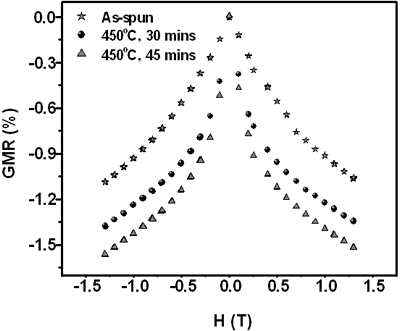 | Figure 6. Time dependence of GMR ratios of Co20Cu80 samples annealed at 450oC. | Samples with high GMR ratios are used as new sensors for magnetic field measurement. A Tesla meter based on the 4-point technique with the GMR sensor has been designed and assembled as shown in Figure 7. The Tesla meter with GMR sensor is able to detect the field as high as 1.3T and work independently on the detected field direction. 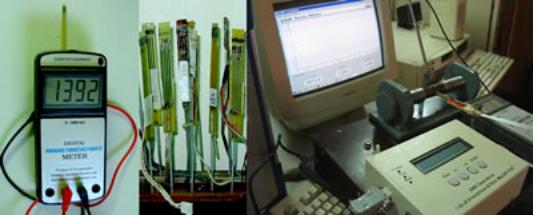 | Figure 7. The GMR sensors and GMR Tesla meters. | Conclusions The Cu-Co granular alloys prepared by rapid quenching method show high GMR ratio of about 5.5% at room temperature. The influence of heat treatment conditions on GMR effect of the CoX Cu(100-X) alloys with x ≈ 8-20 was investigated. The optimum annealing condition was found to be 450oC for 60 min for composition of Co10Cu90. A Tesla meter with GMR sensor has been made. Acknowledgements This work was supported by State Programs on Basic Science and Advanced materials (Vietnam). Authors thankfully acknowledge the sample preparation and magnetic measurement performed at Lab of Amorphous materials and ITIMS (Hanoi University of Technology). References 1. M. N. Baibich, J. M. Broto, A. Fert, Nguyen Van Dau, R. F. Petroff, P. Eitenne, G. Creuzet, A. Friederich and J. Chazelas, "Giant Magnetoresistance of (001)Fe/(001)Cr Magnetic Superlattices", Phys. Rev. Lett., 61 (1988), 2472. 2. A. E. Berkowitz, J. R. Mitchell, M. J. Carey, A. P. Young, S. Zhang, F. E. Spada, F. T. Parker, A. Hutten and G. Thomas, "Giant magnetoresistance in heterogeneous alloys", Phys. Rev. Lett., 68 (1992) 3745-3748. 3. J.Q. Xiao, J.S. Jiang and C.L. Chien, "Giant Magnetoresistance in Nonmultilayers Magnetic Systems", Phys. Rev. Lett., 68 (1992) 3749-3752. 4. A. D. C Viegas, J. Geshev, L. S. Dorneles and J. E. Schmidt, "Correlation Between Magnetic Interactions and Giant Magnetoresistance in Melt-Spun Co10Cu90 Granular Alloys", J. Appl. Phys., 82[6], (1997). 5. P. M. Levy, "Current Understanding and Open Questions on Giant Magnetoresistance", J. Magnetism and Magnetic Materials, 485 (1995) 140-144. 6. M. G. M. Miranda, G. J. Bracho Rodriguez, A. B. Antunes, M. N. Baibich, E. F. Ferrari, F. C. S. da Silva and M. Knobel, "Transport and Structure of Co10Cu90 Heterogeneous Ribbons During Annealing", J. Magn. Magn. Mat., 185 (1998) 331-338. 7. D. Altbir, P. Vargas and J. d Albuquerque e Castro, "Magnetic Coupling in Metallic Granular Systems", Phys. Rev. B, 54 (1996) 6823. 8. M. Kuzminski, A. Slawska-Waniewska, H. K. Lachowicz and M. Knobel, "The Effect of Particle Size and Surface-to-Volume Ratio Distribution on Giant Magnetoresistance (GMR) in Melt Spun Cu-Co Alloys", J. Magn. Magn. Mat., 205 (1999) 7-13. 9. N.H. Nghi, N.D. Nhan, C.V. Thang, N.X. Phuc, N.M. Hong, N.H. Duc, N.A. Tuan, B.X. Chien and L.M. Hoa, "GMR effect of Rapidly Solidified Co-Cu alloys", Proceedings of the Fifth Vietnamese-German Seminar on Physics and Engineering, Hue, Vietnam, (2002) 185-189, Printed by Hanoi University of Technology, 2002. Contact Details |