Introduction A Si3N4 ceramic is one of the most important structural materials, because they have excellent high temperature strength, good resistance to oxidation and low coefficient of thermal expansion. However, the pure Si3N4 ceramics are difficult to densify due to its low self-diffusivity of this type of covalent material. Normally, oxides, such as Y2O3, Al2O3, Yb2O3, ZrO2, Nd2O3 and Dy2O3 [1-4] are added as sintering additives to improve the sinterability of Si3N4. The additives can form liquid phase in grain boundaries, which is beneficial to improve the sinterability of Si3N4. It was reported [5] that Lu2O3-SiO2 additives are useful to improve the bending strength of Si3N4 at elevated temperature; this is attributable to the formation of a high melting point Lu4Si2O7N2 grain boundary phase, which can be extensively crystallized during sintering. The bending strength of the tape-cast Si3N4 with rod-like β-Si3N4 seed can also be further improved [6-7] because the elongated grains from seeds were preferentially oriented parallel to the casting direction. Therefore, in this study, Lu2O3-SiO2 additives were selected as sintering additives, and tape casting was used to prepare the unidirectional aligned β-Si3N4 elongated grains Si3N4 ceramics. Experimental Procedure The starting powders used in the experiments were Si3N4 (SN-E10, UBE Industries, Tokyo, Japan), Lu2O3 (99.9% purity, Shinetsu Chemical Co., Ltd., Tokyo), and SiO2 (High Purity Chemical Co., Ltd.,). Rod-like β-Si3N4 seed was prepared in our laboratory. A powder composition of 3 wt% β-Si3N4 seed, 90 wt% Si3N4, 1 wt% SiO2, and 9 wt% Lu2O3 powder were made. The powders were ball milled with solvent and dispersant for 24 h, then after adding a binder and a plasticizer, they were ball milled for another 48 h. The slurry was dispersed in an ultrasonic bath for 5 min to break up soft agglomerates and degased in vacuum before tape casting. The typical composition of the slurry is shown in Table 1. Table 1. Typical slurry composition. | Si3N4 | Powder | 38.2 | Lu2O3 | Additive | 3.9 | SiO2 | Additive | 0.4 | Diamine RRT | Dispersant | 1.3 | N-butyl alcohol | Solvent | 8.9 | Toluene | Solvent | 40.2 | PVB | Binder | 3.9 | Bis(2-ethylhexyl) adipate | Plasticizer | 1.9 | Tape casting was performed in a tape casting machine (Sansho Industrial, Co., Ltd., Japan). The casting speed was 20 cm/min. The cast slurry was dried on the drying chamber, where the temperature can be controlled in three different stages, i.e. 45°C, 55°C, and 70°C. Finally, the green body of Si3N4 can be received through debonding, cutting, laminating and CIPing green tapes. The green body was then CIPed at 200 MPa and dried in an oven for 48 h before binder removal. The green body was sintered at 10 atm N2 atmosphere at 1950°C for 6 h. The rectangular shape specimens with dimension 3 × 2 × 20 mm were machined to measure the bending strength at room temperature (6 specimens) and elevated temperatures (4 specimens). A three-point bending test (span 16 mm) was used in the experiment. The microstructure was studied by scanning electron microscope (SEM) of specimens with polished and plasma-etched surfaces. The sample surface etching was carried out in CF4 plasma. X-ray diffraction (XRD) was used to determine phase compositions, and thermogravimetric analysis (TGA) was employed to investigate the weight loss of the green tape during the binder removal, Figure 1 shows the SEM photograph of the rod-like Si3N4 seeds. 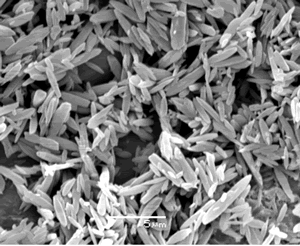 | Figure 1. SEM photograph of the rod-like β-Si3N4 seeds. | Results and Discussion Figure 2 shows the typical SEM micrographs of the tape-cast Si3N4 with and without rod-like β-Si3N4 seed addition. Figures 2 (a) and (b) indicate that the Si3N4 has obvious anisotropic microstructure. As previously reported [8], the whiskers or particles with anisotropic shapes are rotated and aligned during tape casting. SEM micrograph shown in Figure 1 indicates that the seed used in the experiment has a large aspect ratio. Therefore, the seeds are easily re-arranged during tape casting and β-Si3N4 grain growth unidirectionally can be enhanced by the rod-like β-Si3N4 seeds. Eventually, the Si3N4 ceramics with highly unidirectionally aligned β-Si3N4 elongated grains can be received. The SEM micrograph (c) of Si3N4 without rod-like β-Si3N4 seed addition shows the isotropic microstructure. Figure 3 shows the XRD patterns of 9 wt% Lu2O3-1 wt% SiO2-Si3N4 with and without 3 wt% Si3N4 seed addition. Their phase composition is the same and the main phases are Si3N4 and Lu4Si2O7N2. However, several small peaks are not easily distinguished, it should be the remnant SiO2 or other Lu-Si-O-N phases [9]. 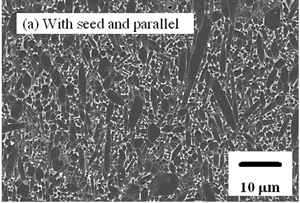 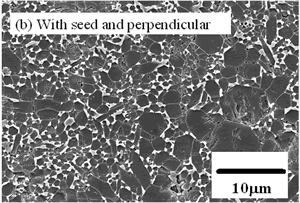 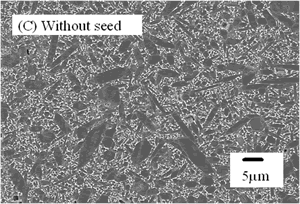 | Figure 2. SEM micrographs of the tape-cast Si3N4 (a) parallel, (b) perpendicular, and (c) no-seed. | 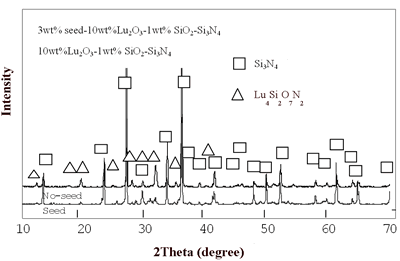 | Figure 3. XRD pattern of the tape-cast Si3N4. | Figure 4 shows bending strength of the Si3N4 with and without rod-like β-Si3N4 seeds addition. The addition of rod-like β-Si3N4 seed is beneficial to improve bending strength in parallel direction at room temperature and 1500°C, however, the bending strength in perpendicular direction is decreased due to the unidirectionally aligned β-Si3N4 elongated grains. The bending strength of the specimens perpendicular to the casting direction is much smaller than that of the parallel direction. The strength of the specimens parallel to the casting direction at 1500°C was 738 MPa, which was almost the same as room temperature bending strength 739 MPa. This is attributable to the formation of the high melting point Lu2Si2O7N2 phase and unidirectionally aligned β-Si3N4 elongated grains. 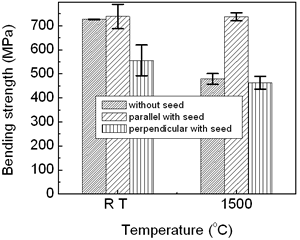 | Figure 4. Bending strength of Si3N4 with and without seeds at different temperatures (tape thickness 100 μm ). | Figure 5 shows the bending strength of the Si3N4 as a function of the thickness of green tape. Compared with the specimens prepared from 150 μm green tape, the Si3N4 specimens prepared from 100 μm green tape show a high bending strength in parallel direction and a low bending strength in perpendicular direction. During tape casting, besides the rheological properties of the slurry, the thickness of the tape has great effect on the degree of rotation of the whisker or the rod-like seed. The thinner the thickness of the tape was, the easier the seed aligned unidirectionally. It means that there are many unidirectionally aligned β-Si3N4 elongated grains in specimens made from 100 μm green tape than that from 150 μm green tape. As an anisotropic material, crack propagation behavior of the Si3N4 is significantly dependent on its microstructure. If the crack propagates perpendicularly to elongated Si3N4 grains growing direction, namely, tape casting direction, there are more elongated grain fractures which enhance crack bridge effects. The large elongated Si3N4 grains increased the opportunities for crack bridging and crack deflection [10]. If the crack propagates parallel to the tape casting direction, intergranular fracture occurs more easily. This made all the seeded and tape-cast specimens to exhibit high bending strength in the direction perpendicular to the grain alignment. 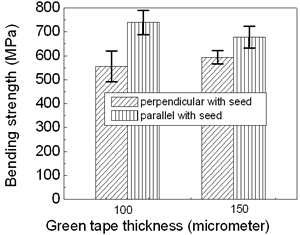 | Figure 5. Bending strength of the Si3N4 as a function of the thickness of green tape (room temperature). | Conclusions Tape casting and gas pressure sintering were employed to prepare unidirectionally aligned β-Si3N4 elongated grain Si3N4 materials, The experimental results indicate that the seeded and tape-cast Si3N4 materials show anisotropic microstructures and bending strength. The thickness of green tape has some effect on the bending strength. Due to the formation of a high melting point grain boundary phase Lu2Si2O7N2 and the unidirectionally aligned β-Si3N4 elongated grains, the seeded and tape-cast Si3N4 shows good bending strength at elevated temperature. The bending strength of the Si3N4 materials are strongly directional at 1500°C and was 738 MPa, which was almost the same as room temperature bending strength of 739 MPa. References 1. Tsuge, K. Nishida and M. Komatsu, “Effect of Crystallizing the Grain-boundary Glass Phase on the High-temperature Strength of Hot-pressed Si3N4 Containing Y2O3”, J. Am. Ceram. Soc., 58 [7-8] (1975) 323-326. 2. H. Park, H. E. Kim and K. Niihara, “Microstructure Evolution and Mechanical Properties of Si3N4 with Yb2O3 as a Sintering Additive”, J. Am. Ceram. Soc., 80 [3] (1997) 750-756. 3. H.-J. Kleebe, G. Pezzotti and G. Ziegler, “Microstructure and Fracture Toughness of Si3N4 Ceramics: Combined Roles of Grain Morphology and Secondary Phase Chemistry”, J. Am. Ceram. Soc., 82 [7] (1999) 857-1867. 4. I.C. Huseby and G. Petzow, “Influence of Various Densifying Additives on Hot-Pressed Si3N4”, Powder Metall. Int., 6 (1974) 17–19. 5. S. Guo, N. Hirosaki, Y. Yamamoto, T. Nishimura and M. Mitomo, “Improvement of High- temperature Strength of Hot-pressed Sintering Silicon Nitride with Lu2O3 addition”, Scripta Materialia, 45 (2001) 867-874. 6. H. Imamura, H. Kiyoshi, E. B. Manuel, T. Motohiro and K. Shuz, “Further Improvement in Mechanical Properties of Highly Anisotropic Silicon Nitride Ceramics”, J. Am. Ceram. Soc., 83 [3] (2000) 495–500. 7. K. Hirao, T. Nagaoka, M. E. Brito and S. Kanzaki, “Microstructure Control of Silicon Nitride by Seeding with Rod-like β-Silicon Nitride Particles”, J. Am. Ceram. Soc., 77 [7] (1994) 1857–62. 8. K. Hirao, M. Ohashi, M.E. Brito and S. Kanzaki, “Processing Strategy for Producing Highly Anisotropic Silicon Nitride”, J. Am. Ceram. Soc., 78 [6] (1995) 1687–90. 9. N. Hirosaki, Y. Yamanoto, T. Nishimura and M. Mitomo, “phase relationships in the -Si3N4-SiO2- Lu2O3 system”, J. Am. Ceram. Soc., 85 [11] (2002) 2861-63. 10. T. Ohji, K. Hirao and S. Kanzaki, “Fracture Resistance Behavior of Highly Anisotropic Silicon Nitride”, J. Am. Ceram. Soc., 78 [11] (1995) 3125–28. Contact Details |