Introduction In the processing of ceramic articles, the most important parameters influencing the quality of the final products are the incorporation of argillaceous minerals and their specific characteristics (composition and purity). Usually the raw material is extracted directly from the terrestrial surface and consequently the concentration of impurities in the raw material is not homogeneus. Depending on the atmospheric and geologic conditions of deposition, as well as the degree of alteration of the clay, it can contain certain mineral concentrations such as: hematite, illmenite, pyrite, magnetite, chromite, etc. These minerals commonly contribute to elements such as Fe, Cr, Mn, Ti and Ni, which have the characteristic to pigment the product undesirably [1, 2]. Raw materials with iron oxide concentrations of 0.5 - 3% reduce the whiteness of the mineral, giving it a brown – yellow coloration and limiting its use in the ceramic industry [2]. Some researchers have developed different physical and chemical techniques (and more recently microbiological) with the purpose of removing the ferric iron present as oxide or hydrated oxide in the clay. Those techniques can increase the whiteness in the final products [3-5]. The use of organic acids has been one of the most efficient methods for the whitening of kaolin. Cameselle et al. [3] found that for dissolving a mol of iron three masses of oxalic acid are necessary for the kaolin studied by them. With this relation they determined the formula of the complex formed by oxalic acid and the iron in solution: 3C2O42- + Fe3+ [Fe(C2O4)3]3- Recent investigations have focused mainly on the study of iron extraction from kaolin, whose main component is kaolinite. In this work the method of iron removal by oxalic acid in a clay sample was adopted. For this purpose, an experimental design was carried out using a 2k Factorial Design, where k is the number of factors [6]. Considered factors are: concentration of oxalic acid, time and temperature, becoming a 23 design. Materials and Methods The clay sample used in this work comes from a deposit located in the South of Mexico, and was provided by a local company. This clay has no commercial interest due to the high content of iron present in it (4.2%) and its low whiteness index (L = 71). Chemical and mineral characterization was made by X-ray fluorescence (XRF) and X-ray diffraction (XRD), respectively. The milling of the clay was carried out using a porcelain mill with alumina balls. Under our conditions, the milling was made until the clay was 85% below mesh 325 (~40µm). A simplex method was used for optimizing the leaching conditions. The matrix of this design is listed in Table 1. The initial conditions of the treatment were selected on the basis of the optimal results for kaolin found in references [2-5]. Table 1. Matrix of the experimental design for three factors 23. | 1 | - | - | - | 2 | + | - | - | 3 | - | + | - | 4 | + | + | - | 5 | - | - | + | 6 | + | - | + | 7 | - | + | + | 8 | + | + | + | A = Oxalic acid B = Time C = Temperature The leaching experiments were carried out using 250 mL flasks with a mixture of 10 g of clay and 100 mL of oxalic acid. The flasks were placed on heating plates with constant agitation (870 rpm). The amount of leached iron after this procedure was determined by atomic absorption spectroscopy. Also, the initial color of the sample was determined in each one of the solids obtained by filtration. For the whiteness measurements, the samples were heat treated at 1000°C for 30 minutes. After this procedure, the whiteness index was determined through a GretagMcBeth colorimeter Eye Color 7000A. Results and Discussion The clay consists of calcite, quartz, albite and muscovite. The iron is present as an amorphous phase and hydroxides, according to the results presented by the company who provided the clay. In Table 2 XRF analysis of the clay is listed. Table 2. XRF analysis of clay. | Al2O3 | 8.23 | Fe2O3 | 4.19 | CaO | 28.96 | MgO | 1.28 | SO3 | 1.37 | Na2O | 0.56 | K2O | 2.40 | TiO2 | 0.52 | P2O5 | 0.10 | Mn2O3 | 0.00 | *LOI. | 22.70 | *950° C The clay under a heat treatment of 1000°C for 30 minutes showed a brown-reddish coloration and a whiteness index (L) of 71. After the leaching process it was observed that in a period of 2 to 3 days a brown-color precipitate is formed and diminished the intensity in color of the leaching solution containing the dissolved iron. The ferric iron is bonded to three oxalate ions by one of the oxygen ions in each one of these acid groups. This complex presents a yellow color, which agrees with the liquors obtained after the treatments with clay [4]. Table 3 lists the results of the first simplex for the factorial design 23. The greater amount of leached iron was 30%, corresponding to low concentrations, but with higher conditions of time and temperature. This result suggests that just the oxalic acid concentration in itself does not affect the iron removal reaction. Combination of concentration and time has a heavier effect in iron removal, yielding higher indexes. This is observed more clearly in Table 4. Possibly this could be due to a low reaction kinetic, in which not only the species concentration take part, but also time (and temperature). Table 3. Results of the first simplex of the factorial design 23. | 1 | 100 | 2 | 50 | 10 | 2 | 200 | 2 | 50 | 5 | 3 | 100 | 5 | 50 | 19 | 4 | 200 | 5 | 50 | 23 | 5 | 100 | 2 | 80 | 15 | 6 | 200 | 2 | 80 | 17 | 7 | 100 | 5 | 80 | 30 | 8 | 200 | 5 | 80 | 27 | A = Oxalic acid B = Time C = Temperature Table 4. Determination of effects and interactions between factors. | 1 | - | - | - | + | + | + | - | 10 | 2 | + | - | - | - | - | + | + | 5 | 3 | - | + | - | - | + | - | + | 19 | 4 | + | + | - | + | - | - | - | 23 | 5 | - | - | + | + | - | - | + | 15 | 6 | + | - | + | - | + | - | - | 17 | 7 | - | + | + | - | - | + | - | 30 | 8 | + | + | + | + | + | + | + | 27 | A = Oxalic acid B = Time C = Temperature Effect A -0.47 Effect B 12.99 Effect C 7.67 Effect of interactions Effect AB 0.84 Effect AC 0.09 Effect BC -0.51 Effect ABC -3.05 According to the results presented in Table 4, time is the factor that affects more on iron removal, since it has the highest index in iron removal. For acid concentration and temperature effects, the result is negative and positive respectively. This indicates a possibility to obtain better results using lower acid concentrations and higher conditions of temperature [7]. However, the combination of these three factors is essential, as observed in the high values obtained in Table 4. Once identified best and worse responses in the removal results, it was come to continue with the second sequential simplex. Because the worse response is the 5% removal in experiment 2 (Table 4), the sequential simplex replaces those conditions with addition of a new experiment No. 9, as listed in Table 5. Table 5. Determination of effects and interactions between factors. | 9 | 86 | 5.4 | 84 | 44 | 10 | 71 | 9 | 99 | 26 | 11 | 71 | 9 | 89 | 39 | 12 | -29 | 9 | 89 | 0 | 13 | 71 | 6 | 99 | 31 | 14 | -29 | 6 | 99 | 0 | 15 | -29 | 6 | 89 | 0 | 16 | 71 | 6 | 89 | 32 | A = Oxalic acid (g/L) B = Time (h) C = Temperature (° C) As observed in experiment 9, the oxalic acid concentration is lowered to 86 g/L. Also, the conditions of time and temperature have been changed to 5.4 h and 84° C, respectively. These changes were very favorable in the removal result, since it increased to a 44%. Because this experiment displayed a far better response compared to the previous ones, the experiments with worse results are replaced by others according to a third sequential simplex. The new experiments were carried out taking into account the results of experiment 9, combined with observations in Table 4 and are listed in Table 5. Application of this new simplex moved the design to negative regions as far as the oxalic acid concentration, which does not have sense in our study. Due to this, only the experiments with positive values of concentration were made, whereas the others were taken equal to zero. These results show that the concentration influences the degree of iron removal. This can be observed clearly in Figure 1. Also, it was observed that time and temperature do not have any effect when increasing their values beyond those suggested in experiment 9, as observed in Figures 2 and 3. 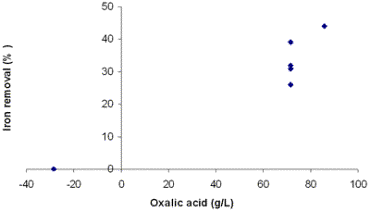 Figure 1. Effect of concentration of oxalic acid on n iron removal in third simplex. 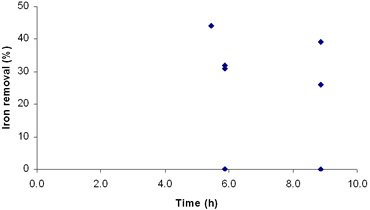 Figure 2. Effect of time on iron removal in third simplex. 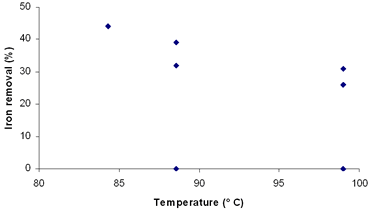 Figure 3. Effect of temperature on iron removal in third simplex. With the correction of our previous design with the new simplex taking into account the latest results, experiments 10 to 16 were replaced. The new experiments and their conditions are listed in Table 6. The new simplex returned us to regions similar to the first one, but reaching considerably higher indexes of iron removal. Table 6. Results of the fourth simplex of the factorial design 23. | 9 | 86 | 5.4 | 84 | 44 | 17 | 100 | 2 | 70 | 30 | 18 | 100 | 2 | 80 | 15 | 19 | 200 | 2 | 80 | 17 | 20 | 100 | 5 | 70 | 25 | 21 | 200 | 5 | 70 | 49 | 22 | 200 | 5 | 80 | 27 | 23 | 100 | 5 | 80 | 30 | A = Oxalic acid (g/L) B = Time (h) C = Temperature (° C) According to these results, we can see that the best conditions of the system are placed in regions of high oxalic acid concentration and temperature (Table 7). Additionally, in Figures 4, 5 and 6 are presented the results of degree of iron removal versus variation in oxalic acid concentration, time and temperature, respectively. Table 7. Determination of effects between factors. | 17 | - | - | - | 30 | 9 | + | - | - | 44 | 18 | - | + | - | 31 | 19 | + | + | - | 35 | 20 | - | - | + | 31 | 21 | + | - | + | 40 | 22 | - | + | + | 46 | 23 | + | + | + | 37 | A = Oxalic acid (g/L) B = Time (h) C = Temperature (° C) Effect A 4.50 Effect B 1.00 Effect C 3.50 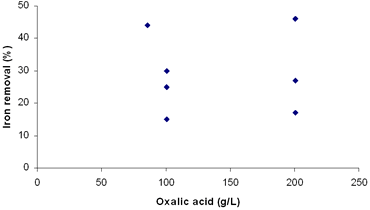 | Figure 4. Effect of concentration of oxalic acid on iron removal in fourth simplex. | 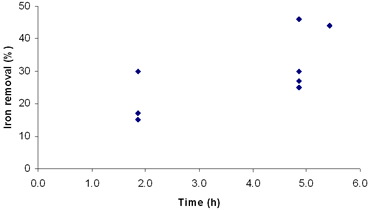 | Figure 5. Effect of time on iron removal in fourth simplex. | 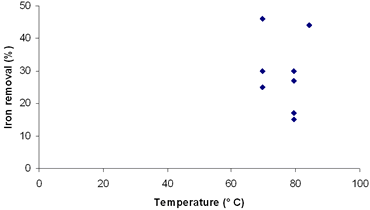 | Figure 6. Effect of temperature on iron removal in fourth simplex. | Conclusions As we have seen, the highest concentration of iron dissolved in each experiment depends on the used oxalic acid concentration and its interaction with time and temperature. At the moment a considerable iron removal has been reached under our conditions, knowing that the clay have a high concentration of iron. At the end of each treatment a yellow, oxalic acid -iron dissolution and clay with high degree of whiteness (L=81) were obtained. The treatment with lower concentrations of oxalic acid reduces proportionally the amount of dissolved iron. A future characterization of the clay by SEM will help us to understand the way in which the iron is allocated in the structure of the clay, so the application of a new simplex will probably take us to other regions with better conditions for iron removal. Acknowledgements We thank CONACyT for its financial support with the scholarship Ref No. 171120, and also the Faculty of Chemical Sciences for its help and use of the laboratories. References 1. R. Galindo, “Pastas y vidriados en la fabricación de pavimentos y revestimientos cerámicos”, FAENZA EDITRICE IBÉRICA, S.L. España, (1994) 251. 2. L. Toro, A. M. Marabini, B. Paponetti and B. Passariello, “Proceso per la rimozione del ferro da concentrati di caolino, quarzo ed altri materiali di interese industriale”, Italian Patent No. 217070 A/90. (1990). 3. C. Cameselle, M. J. Núñez and J. M. Lema, “Leaching of Kaolin Iron – Oxides with Organic Acids”, J. Chem. Tech. Biotechnol., 70 (1997) 349-354. 4. C. Cameselle, M. J. Núñez and J. M. Lema, “Bioblanqueo de caolines con Aspergillus niger. Afinidad”, Tomo LV, No. 478. 1998. 5. V. R. Ambikadevi and M. Lalithambika, “Effect of organic acids on ferric iron removal from iron – stained kaolinite”, Applied Clay Science, 16 (2000) 133-145. 6. D. Montgomery, “Diseño and análisis de experimentos”, Limusa-Wiley, 2nd Ed., (2004) 686. 7. N. Treviño, “Estrategias de optimación, Manual de Laboratorio de Química Orgánica IV”, Facultad de Ciencias Químicas, Universidad Autonoma de Nuevo Leon (UANL), (2003). Contact Details |