The advanced metallic hot zones available from PLANSEE have been developed for temperatures ranging from 1000°C to 2800°C. PLANSEE specializes in thermal processes, such as hot isostatic pressing (HIP) and high vacuum, protective gas atmospheres. The company answers any queries related to brazing, sintering, heating and annealing systems.
.png)
PLANSEE Provides Optimum Solution
PLANSEE teams up with system engineers and users to develop hot zones for contemporary thermal processes. For instance, in growth sectors like silicon or sapphire crystal growing, PLANSEE works with the clients right from the conception stage to arrive at a suitable solution.
Generally, hot zones comprise innumerable number of components such as charge carriers, heating elements, hearth assemblies and shield packs. Customers can get all these parts at PLANSEE. Some of the components are listed below:
- Wire mesh heaters
- Ribbon heaters
- Twisted wire heaters
- Charge carriers
- Screws, bolts, nuts
- Shieldings
- Tubes
- Full metal or hybrid hot zones with ceramic or graphite fiber insulation
- Hot zones made from tungsten, molybdenum, niobium, tantalum and their alloys
- From extremely small to large hot zones
- Customized designs such as rectangular, round, horizontal, vertical or unique geometries are available
PLANSEE’s team ensures that the right configuration of the heat shielding and heating capacity is achieved and makes sure that there is an even temperature across the furnace, and then concurrently minimizes heat loss. For individual hot zone, PLANSEE selects the materials to suit particular requirements. The company delivers molybdenum hot zones equipped with steel supporting frames for temperatures of approximately 1300°C. For temperatures of 1700 °C or above, PLANSEE usually selects tungsten for those parts that are subjected to more thermal stress. The hybrid hot zones from PLANSEE feature ceramic fiber insulation or graphite felt.
.png)
Metallic Hot Zones
Graphite furnaces tend to cause contamination owing to the presence of carbon. On the other hand, metallic furnaces fprovide a clean and carbon-free solution.
Some of the advantages offered by PLANSEE hot zones are short cycle times, superior vacuum conditions, special metal alloys for excellent dimensional stability, no contamination and very fast quenching with high gas pressures
Tungsten and Molybdenum
Tungsten and molybdenum are refractory metals and are suitable for applications at extreme temperatures, unlike other materials. These metals have unique properties, which make them an ideal option for components employed in the furnace construction industry. These metals have excellent creep resistance, superior dimensional stability, high melting points that allow operating temperatures of up to 2800°C. They have a low coefficient of thermal expansion and an excellent corrosion resistance.
TZM for Better Creep Resistance
To meet demanding applications, PLANSEE adds zirconium and titanium to reinforce the microstructure of pure molybdenum. Ti-Zr carbides and Mo-Ti solid solution make sure that optimum strengths are attained at approximately 1400°C temperatures.
TZM is comparatively better than pure molybdenum because it has greater thermal stability, improved creep resistance and higher recrystallization temperature.
ML for More Ductility
PLANSEE uses appropriate alloys and optimized manufacturing processes in order to enhance molybdenum’s properties, and also dopes pure molybdenum with small quantities of La2O3 to realize a high level of creep resistance and ductility. The modified recrystallization behaviour combined with the stabilized microstructure helps in preventing fracture and premature embrittlement of PLANSEE’s furnace components.
When compared to pure molybdenum, ML is significantly better as it has higher creep resistance, higher recrystallization temperature, enhanced resistance to oxidation and extended grain structure for better ductility
ENERZONE® Offers an Efficient Solution
Ceramic fiber insulation, better shielding and less mass are the secrets behind PLANSEE’s low energy hot zones. In addition to consuming 20% to 25% less energy, the hot zones are comparatively better than standard metal hot zones.
.png)
For instance, when the furnace is lightweight, it promotes rapid heating, which results in shorter heating cycle and reduced power usage. Moreover PLANSEE has substituted pure molybdenum with molybdenum alloys, like TZM and ML. Owing to the excellent strength of these materials, the company is able to use thinner shieldpacks and charge carrier parts. PLANSEE has also used molybdenum by replacing various stainless steel components, because one layer of molybdenum delivers the same shielding effect similar to five layers of steel.
Molybdenum Components for Coating Facilities
Molybdenum is a key aspect of CIGS solar cells and is also employed in equipment used for manufacturing thin film solar cells for shielding, heating or supporting functions. Whether pure or doped with other alloys, molybdenum provides an ideal solution for complex vacuum processes even at extremely high temperatures.
.jpg)
.png)
PLANSEE has an engineering team that deals specifically in the construction of furnaces. Whether they are sintering furnaces, annealing furnaces or coating systems, the team specializes in all high-temperature processes. Additionally, FEM analyses help in eliminating mistakes. For instance, the team can demonstrate how one particular hot zone will work in live operation. For complex projects, the team designs models using 3D computer drawings and all aspects are completely checked. PLANSEE installs its products at the customers’ premises and also checks, maintains and optimizes existing furnaces.
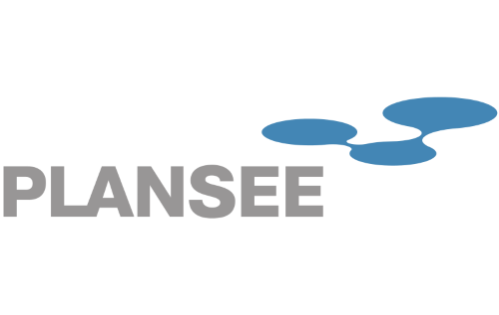
This information has been sourced, reviewed and adapted from materials provided by PLANSEE.
For more information on this source, please visit PLANSEE.