|
|
Topics Covered |
Background Electric EAPs Ferroelectric Polymers Dielectric EAP Electrostrictive Graft Elastomers Electrostrictive Paper Electro-Viscoelastic Elastomers Liquid Crystal Elastomer (LCE) Materials Ionic EAPs Ionic Polymer Gel (IPG) Ionomeric Polymer-Metal Composites (IPMC) Conductive Polymers (CP) Carbon Nanotubes (CNT) Applications |
Background |
In the last decade a new breed of polymer has emerged which responds to external electrical stimulation by displaying a significant shape or size displacement. These materials, known as electroactive polymers, or more commonly EAPs are now on the verge of many exciting applications. EAPs have attracted much attention from engineers and scientists from diverse disciplines. In particular, researchers in the field of biomimetics (a field of study where robotic mechanisms are based on biologically-inspired models) find it foreseeable that these materials may be applied to mimic the movements of animals, insects and even human body parts (Figure 1). 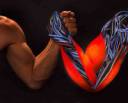 | Figure 1. Potential application for EAP in biomimetics. | Generally, EAPs have the ability to induce strains that are as high as two orders of magnitude greater than the movements possible with rigid and fragile electroactive ceramics (EACs). EAP materials have higher response speeds, lower densities and improved resilience when compared to shape memory alloys (SMAs). Limiting factors to EAPs are low actuation forces, mechanical energy density and lack of robustness. However, there have been reported successful applications in catheter steering elements, miniature manipulators, dust-wipers, miniature robotic arms and grippers. There are two major categories that EAPs depending on their mode of activation mechanism, these include, electronic and ionic categories. Table 1, outlines the advantages and disadvantages of both types of EAPs. Table 1. Outline advantages and disadvantages of both electronic and ionic EAP categories. | Electronic EAP | • Can operate in room conditions for long periods of time • Rapid response time (mSec levels) • Can hold strains under DC activation • Induces relatively large actuation forces | • Requires high voltages (~150 MV/m) • Requires compromise between strain and stress • Glass transition temperature is inadequate for low temperature actuation tasks | Ionic EAP | • Requires low voltage • Provides predominately bending actuation (longitudinal mechanisms can be constructed) • Exhibits large bending displacements | • Except for CP (Conductive Polymers), ionic EAPs don’t hold strain under DC voltage • Slow response (fraction of a second) • Bending EAPs induce a relatively low actuation force • Except for CP and CNT (Carbon Nanotubes), it is difficult to produce a consistent material (particularly IPMC – Ionomeric Polymer-Metal Composites) • In aqueous systems the material sustains hydrolysis at > 1.23 V | Electric field or Coulomb forces generally drive electronic EAPs, while the primary driver for ionic EAPs is the mobility or diffusion of ions. Types of Electric EAPs and Ionic EAPs are summarised below: |
Electric EAPs |
Ferroelectric Polymers |
Piezoelectricity was discovered in 1880, with the discovery that certain crystals e.g. quartz, tourmaline and Rochelle salt, when compressed along certain axes, produced a voltage on the surface of the crystal. The reverse effect was also found whereby application of an electric current saw the crystal sustain an elongation. Poly(vinylidene fluoride) or PVDF and its copolymers are the most exploited ferroelectric polymers. They consist of a partially crystalline component in an inactive amorphus phase. Large applied AC fields (~200 MV/m) induce electrostrictive (non-linear) strains of nearly ~2%. P(VDF-TrFE) a PVDF polymer which has been subject to electron radiation has shown electrostrictive strain as high as 5% at lower frequency drive fields (150 V/μm). Ferroelectric EAP polymer actuators can be operated in air, vacuum or water and throughout a wide temperature range. |
Dielectric EAP |
Electrostatic fields can be employed to those polymers exhibiting low elastic stiffness and high dielectric constants to induce large actuation strain, these polymers are known as electro-statically stricted polymers (ESSP) actuators. Dielectric EAP actuators require large electric fields (~100 V/μm) and can produce strain levels (10—200%). It has been reported that an acrylic elastomer tape manufactured by 3M™ (tradename VHB™) is capable of planar strains of more than 300% for biaxially symmetric constraints and linear strains up to 215% for uniaxial constraints. |
Electrostrictive Graft Elastomers |
This is a polymer consisting of two components, a flexible macromolecule backbone and a grafted polymer that can be produced in a crystalline form. The material exhibits high electric field induced strain (~4%) combined with mechanical power and excellent processability. A typical example is a combination of an electrostrictive-grafted elastomer with a piezoelectric poly(vinylidene fluoride-trifluoro-ethylene) copolymer. This combination has the ability to produce a varied amount of ferroelectric-electrostrictive molecular composite systems. These may be operated as a piezoelectric sensor or even an electrostrictive actuator. |
Electrostrictive Paper |
Generally the paper is composed of a multitude of discrete particles, which are mainly of a fibrous nature forming a network structure. An example of which is silver laminated paper whereby two silver laminated pieces of paper with silver electrodes are placed on the outside surfaces. Upon electric voltage being applied to the electrodes a bending displacement occurs. These types of actuators are lightweight, simple to fabricate and are likely to be used in applications such as active sound absorbers, flexible speakers and “smart” shape control devices. |
Electro-Viscoelastic Elastomers |
These materials are composites of silicone elastomer and a polar phase. Upon curing an electric field is applied that orientates the polar phase within the elastomeric matrix. An applied electric field (<6 V/μm) induces changes in shear modulus. Typical forecast applications are as alternatives to electro-rheological fluids for active damping applications. |
Liquid Crystal Elastomer (LCE) Materials |
These posses EAP characteristics by inducing Joule heating. LCEs are composite materials consisting of monodomain nematic liquid crystal elastomers and conductive polymers, which are distributed within their network structure. The actuation mechanism is a phase transition between nematic and isotropic phases. The actuation takes place in less than a second. |
Ionic EAPs |
Ionic Polymer Gel (IPG) |
These are polymer gels having the potential of matching the force and energy density of biological muscles. The polyacrylonitrile materials are activated by chemical reaction(s), a change from an acid to an alkaline environment inducing an actuation through the gel becoming dense or swollen. The actuation is somewhat slow due to the diffusion of ions through the multilayered gel. |
Ionomeric Polymer-Metal Composites (IPMC) |
These are EAPs that bend in response to an electrical activation as a result of the mobility of cations in the polymer network. Generally, two types of base polymers are employed to form IPMCs these are Nafion® (perfluorosulphonate manufactured by Du Pont) and Flemion® (perfluorocaboxylate manufactured by Asahi Glass, Japan). IPMC require relatively low voltages to stimulate a bending response (1-10 V) with low frequencies below 1 Hz. |
Conductive Polymers (CP) |
CPs actuate via the reversible counter-ion insertion and expulsion that occurs during redox cycling. Significant volume changes occur through oxidation and reduction reactions at corresponding electrodes through exchanges of ions with an electrolyte. Electrodes are commonly fabricated from polypyrrole or polyaniline, or PAN doped with HCl. CP actuators requires voltages in the range of 1-5 V. Variations to the voltage can control actuation speeds. Relatively high mechanical energy densities of over 20 J/cm3 are attained with these materials, however, they posses low efficiencies at levels of 1%. Other material combinations for CP are polypyrrole, polyethylenedioxythiophene, poly(p-phenylene vinylene)s, polyaniline and polythiophenes. Some applications reported for these CPs are miniature boxes that have the ability to open and close, micro-robots, surgical tools, surgical robots that assemble other micro-devices. |
Carbon Nanotubes (CNT) |
In 1999, CNTs emerged as formal EAPs with diamond-like mechanical properties. The actuation mechanism is through an electrolyte medium and the change in bond length via the injection of charges that affect the ionic charge balance between the nano-tube and the electrolyte. The more charges that are injected into the CNT the larger the dimension change. As a consequence of the mechanical strength and modulus of single CNTs and the achievable actuator displacements, these EAPs can boast the highest work per cycle and generate much higher mechanical stresses than other forms of EAPs |
Applications |
Applications of EPAs are still in their embryonic stages however, some of these include: parts that will have the ability to mimic insect, animal or even human systems (e.g. human artificial muscles), catheter steering elements, miniature manipulator, dust-wipers, miniature robotic arms, grippers, electro-rheological fluids for active damping, miniature boxes, micro-robots, surgical tools and surgical robots that have the ability to assemble other micro-devices. Primary author: Dr. Yoseph Bar-Cohen Source: Electroactive Polymers as Artificial Muscles – Reality and Challenges (2001), Proceedings of the 42nd AIAA Structures, Structures Dynamics and Materials Conferences (SDM), Gossamer Spacecraft Forum (GSF), held in Seattle WA, April 16-19. For more information on this source please visit http://ndeaa.jpl.nasa.gov |