One common description of plasma is that it is the fourth state of matter. We normally think of the three states of matter as solid, liquid and gas. For the most commonly known substance, water, these states are ice, water and steam. If you add heat energy, the ice will change from a solid to a liquid, and if more heat is added, it will change to a gas (steam). When substantial heat is added to a gas, it will change from gas to plasma, the fourth state of matter.
Ionisation
If we add more energy to water, it vaporises and separates into two gases, hydrogen and oxygen, in the form of steam. By adding even more energy to a gas, we find that its characteristics are modified substantially in terms of temperature and electrical characteristics. This process is called ionisation, the creation of free electrons and ions among the gas atoms.
By adding even more energy to a gas, we find that its characteristics are modified substantially in terms of temperature and electrical characteristics. This process is called ionisation, the creation of free electrons and ions among the gas atoms. When this happens, the gas, which has now become a plasma, is electrically conductive because free electrons are available to carry current. Many of the principles that apply to current conduction through metals also apply to plasmas. For example, if the current-carrying cross-section of a metal is reduced, the resistance increases. A higher voltage is needed to force the same amount of electrons through this cross-section and the metal heats up. The same is true for a plasma gas; the more we reduce the cross-section, the hotter it gets.
In this historic review of the plasma arc process, we will follow the development of a plasma arc with high speed gas flow which is, essentially, the "plasma cutting process."
Development of the Plasma Arc Process
In 1941, the U.S. defence industry was looking for better ways of joining light metal together for the war effort and, more specifically, for the production of airplanes. Out of this effort, a new welding process was born. An electric arc was used to melt the metal, and an inert gas shield around the arc and the pool of molten metal was used to displace the air, preventing the molten metal from picking up oxygen from the air. This new process "TIG" (Tungsten Inert Gas), seemed to be a perfect solution for the very specific requirement of high-quality welding. Since this welding process became a substantial user of such gases as argon and helium, the industry that had the most interest in this new application turned out to be the industrial gas manufacturers. These industrial gas companies and, in particular, Union Carbide's Linde Division, became active and successful with the TIG process, also known as "Argonarc" or "Heliarc." Today, this process is referred to as "GTAW" (Gas Tungsten Arc Welding).
By 1950, TIG had firmly established itself as a new welding method for high-quality welds on exotic materials. While doing further development work on the TIG process, scientists at Union Carbide's welding laboratory discovered that when they reduced the gas nozzle opening that directed the inert gas from the TIG torch electrode (cathode) to the workpiece (anode), the properties of the open TIG arc could be greatly altered. The reduced nozzle opening constricted the electric arc and gas and increased its speed and its resistive heat. The arc temperature and voltage rose dramatically, and the momentum of the ionised and non-ionised gas removed the molten puddle due to the higher velocity. Instead of welding, the metal was cut by the plasma jet.
In Figure 1, both arcs are operating in argon at 200 amps. The plasma jet is only moderately constricted by the 3/16 inch (4.8 mm) diameter of the nozzle orifice, but it operates at twice the voltage and produces a much hotter plasma arc than the corresponding TIG arc. If the same current is forced through a nozzle with an even smaller opening, the temperature and voltage rise. At the same time, the higher kinetic energy of the gas leaving the nozzle ejects the molten metal, creating a cut.
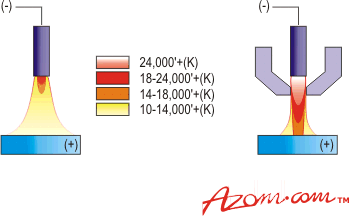
|
Figure 1. Temperature profiles for TIG arc and plasma jet (right).
|
The plasma cutting arc was considerably hotter than the TIG arc shown in Figure 2. These greater temperatures were possible because the high gas flow in the plasma torch nozzle formed a relatively cool boundary layer of un-ionised gas along the nozzle wall, allowing a higher degree of arc constriction. The thickness of this boundary layer could be further increased by swirling the cutting gas. The swirling action forced the heavier, cooler, un-ionised gas to move radially outward and form a thicker boundary layer. Most plasma cutting torches swirled the cutting gas to attain maximum arc constriction.
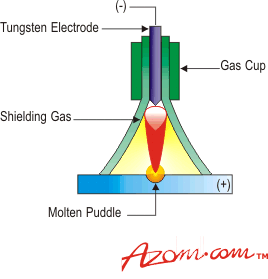
|
Figure 2. TIG welding arc.
|
Transferred and Non-Transferred Modes
A plasma jet can be operated in the transferred mode, where the electric current flows between the plasma torch electrode (cathode) and the workpiece (anode). It can also be operated in the non-transferred mode where the electric current flows between the electrode and the torch nozzle. Both modes of operation are illustrated in Figure 3.
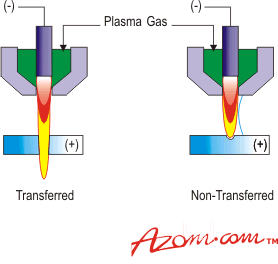
|
Figure 3. Transferred and non-transferred modes.
|
Although a stream of hot plasma emerges from the nozzle in both modes of operation, the transferred mode is invariably used in plasma cutting because the usable heat input to the workpiece is more efficiently applied when the arc is in electrical contact with the workpiece.
Altering the Characteristics of the Plasma Jet
The characteristics of the plasma jet can be altered greatly by changing the gas type, gas flow rate, arc current, arc voltage and nozzle size. For example, if low gas flow rates are used, the plasma jet becomes a highly concentrated heat source ideal for welding. Conversely, if the gas flow rate is increased sufficiently, the velocity of the plasma jet is so great that it ejects molten metal created by the hot plasma arc and cuts through the workpiece.
Conventional Plasma Arc Cutting (1957)
The plasma jet generated by conventional "dry" arc constriction techniques was introduced in 1957 by Union Carbide's Linde Division. In the same year, Dr. Robert Gage obtained a patent, which for 17 years gave Union Carbide a virtual monopoly. This technique could be used to sever any metal at relatively high cutting speeds. The thickness of a plate could range from thin sheet metal to plates as thick as ten inches (250 mm). The cut thickness was ultimately dependent on the current-carrying capacity of the torch and the physical properties of the metal. A heavy duty mechanized torch with a current capacity of 1000 amps could cut through 10-inch thick stainless steel and aluminium. However, in most industrial applications, plate thickness seldom exceeded two inches. In this thickness range, conventional plasma cuts were usually bevelled and had a rounded top edge. Bevelled cuts were a result of an imbalance in the heat input into the cut face. A positive cut angle resulted because the heat energy at the top of the cut dissipated as the arc progressed through the cut.
This heat imbalance was reduced by placing the torch as close as possible to the workpiece and applying the arc constriction principle, as shown in Figure 1. Increased arc constriction caused the temperature profile of the electric arc to become extended and more uniform. Correspondingly, the cut became more square. Unfortunately, the constriction of the conventional nozzle was limited by the tendency of increased constriction to develop two arcs in series, one arc between the electrode and nozzle and a second arc between the nozzle and workpiece.
This phenomenon was known as "double arcing" and damaged both the electrode and nozzle. Double arcing severely limited the extent to which plasma cut quality could be improved. Since the introduction of the plasma arc process in the mid-50's, considerable research has focused on increasing arc constriction without creating double arcing. Plasma arc cutting as performed then is now referred to as "conventional plasma cutting." It can be cumbersome to apply if the user is cutting a wide variety of metals and different plate thicknesses. For example, if the conventional plasma process is used to cut stainless steel, mild steel, and aluminium, it is necessary to use different gases and gas flows for optimum cut quality on all three metals.
Conventional plasma cutting predominated from 1957 to 1970, and often required very expensive gas mixtures of argon and hydrogen.
Dual Flow Plasma Arc (1962)
The dual flow technique was developed and patented by Thermal Dynamics Corporation and James Browning, President of TDC, in 1963. It involved a slight modification of the conventional plasma cutting process. Essentially, it incorporated the same features as conventional plasma cutting, except that a secondary gas shield was added around the plasma nozzle. Usually, in dual flow operation the cutting, or plasma, gas was nitrogen and the secondary shielding gas was selected according to the metal to be cut. Secondary shield gases typically used were air or oxygen for mild steel, carbon dioxide for stainless steel, and an argon/hydrogen mixture for aluminium.
Cutting speeds were still better than with conventional cutting on mild steel; however, cut quality was inadequate for many applications. Cutting speeds and quality on stainless steel and aluminium were essentially the same as with the conventional process.
The major advantage of this approach was that the nozzle could be recessed within a ceramic gas cup or shield cup as shown in Figure 4, preventing the nozzle from shorting with the workpiece, and reducing the tendency for double arcing. The shield gas also covered the cutting zone, improving cut quality and speeds as well as cooling the nozzle and shield cap.
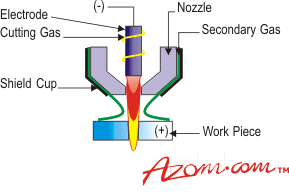
|
Figure 4. Dual flow plasma cutting.
|
Air Plasma Cutting (Since 1963)
Air cutting was introduced in the early 1960s for cutting mild steel. The oxygen in the air provided additional energy from the exothermic reaction with molten steel. This additional energy increased cutting speeds by about 25% over plasma cutting with nitrogen. Although the process could be used to cut stainless steel and aluminium, the cut surface on these materials was heavily oxidized and unacceptable for many applications.
The biggest problem with air cutting has always been the rapid erosion of the plasma torch electrode. Special electrodes, made of zirconium, hafnium, or hafnium alloy, were needed since tungsten eroded in seconds if the cutting gas contained oxygen. Even with these special materials, electrode life using air plasma was much less than the electrode life associated with conventional plasma.
Although air cutting was not pursued in the late 1960s in the United States and the western world, steady progress was made in eastern Europe with the introduction of the "Feinstrahl Brenner" (torch producing a restricted arc), developed by Manfred van Ardenne. This technology was adopted in Russia and eventually in Japan. The major supplier became Mansfeld of East Germany. Several shipyards in Japan were early users of air plasma cutting equipment. However, the electrode life was relatively short and studies disclosed that the cut face of the workpiece had a high percentage of nitrogen in solution which could cause porosity when subsequently welded.
Water Shield Plasma Cutting (1965)
Water shield plasma cutting was similar to dual flow except that water was substituted for the shield gas. Cut appearance and nozzle life were improved because of the cooling effect provided by the water. Cut squareness, cutting speed and dross accumulation were not measurably improved over dual flow plasma cutting because the water did not provide additional arc constriction.
Water Injection Cutting (1968)
Earlier, it was stated that the key to improving cut quality was increasing arc constriction while preventing double arcing. In the water injection plasma cutting process, water was radially injected into the arc in a uniform manner as shown in Figure 5. The radial impingement of the water at the arc provided a higher degree of arc constriction than could be achieved by just the copper nozzle alone. Arc temperatures in this region are estimated to approach 50,000°K or roughly nine times the surface temperature of the sun and more than twice the temperature of the conventional plasma arc. The net result was improved cut squareness, increased cutting speeds and the elimination of dross when cutting mild steel. Radial water injection arc constriction was developed and patented in 1968 by Richard W. Couch Jr., President of Hypertherm, Inc.
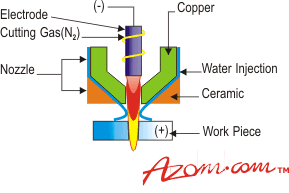
|
Figure 5. Water injection plasma cutting.
|
Another approach taken to constrict the arc with water was to develop a swirling vortex of water around the arc. With this technique, the arc constriction was dependent on the swirl velocity needed to produce a stable water vortex. The centrifugal force created by the high swirl velocity tended to flatten the annular film of water against the arc and, therefore, achieved less of a constricting effect than with radial water injection.
Unlike the conventional process described earlier, optimum cut quality with water injection plasma was obtained on all metals with just one gas: nitrogen. This single gas requirement made the process more economical and easier to use. Physically, nitrogen was ideal because of its superior ability to transfer heat from the arc to the workpiece. The heat energy absorbed by nitrogen when it dissociated was relinquished when it recombined at the workpiece. Despite the extremely high temperatures at the point where the water impinged the arc, less than 10% of the water was vaporized. The remaining water exited from the nozzle in the form of a conical spray, which cooled the top surface of the workpiece. This additional cooling prevented the formation of oxides on the cut surface and efficiently cooled the nozzle at the point of maximum heat load.
The reason for arc constriction at the zone of water injection was the formation of an insulating boundary layer of steam between the plasma jet and the injected water. (This steam boundary layer, the "Linden Frost Layer," is the same principle that allows a drop of water to dance around on a hot metal plate rather than immediately vaporizing.)
Nozzle life was greatly increased with the water injection technique because the steam boundary layer insulated the nozzle from the intense heat of the arc, and the water cooled and protected the nozzle at the point of maximum arc constriction and maximum arc heat. The protection afforded by the water steam boundary layer also allowed a unique design innovation: the entire lower portion of the nozzle could be ceramic. Consequently, double arcing, a major cause of the nozzle destruction, was virtually eliminated.
An important characteristic of the cut edges was that the right side of the kerf was square and the left side of the kerf was slightly beveled. This was not caused by water injection but rather it resulted from the clockwise swirl of the plasma gas. This swirl caused more arc energy to be expended on the right side of the kerf. This same cut asymmetry existed using the conventional "dry" cutting when the cutting gas was swirled. This meant that the direction of travel needed to be properly selected to produce a square cut on the correct side of the workpiece.
In the case of cutting a ring with parallel sides, the outer radius would be cut in the clockwise direction, which gives a square cut on the right side. Similarly, the inside cut is made in a counterclockwise direction to maintain a square edge on the inside of the ring. A counterclockwise swirl ring can be provided which reverses the gas flow swirl and, consequently, also the good side of the cut to the left side. This would be used if a two torch cutting system had to cut mirror image parts simultaneously.
Water Muffler and Water Table (1972)
Since the plasma arc process was a highly concentrated heat source of up to 50,000K, there were some negative side effects with which to contend:
• At highest arc current, plasma cutting generated an intense noise level well over that normally allowed at work areas, requiring ear protection.
• Smoke and potentially toxic gas developed at the work area, requiring good ventilation.
• Ultraviolet radiation, which could potentially lead to skin and eye burns, required protective clothing and dark glasses.
These side effects opened the plasma arc process to criticism on the environmental front. Something had to be found to deal with these problem areas.
In 1972, Hypertherm introduced and patented the Water Muffler and the Water Table Pollution Control systems, which controlled the potentially hazardous effects of plasma arc cutting.
Water Muffler
The Water Muffler system created a high flow water shield around the torch which produced the following benefits when used with a Water Table:
• The high noise level of the plasma arc was sharply reduced through the muffling effect of the water curtain.
• Smoke and toxic gases were confined to the area of the water curtain, which acted as a water scrubber, removing the smoke particles in the water.
• Arc glare was reduced to a level that was less dangerous to the eyes.
• With the proper dye in the water, ultraviolet radiation was diminished.
Water Table
The water reservoir of the Water Table located beneath the workpiece encapsulated the high intensity noise from escaping out the bottom of the cut and also absorbed smoke particles.
Underwater Cutting (1977)
Further attempts in Europe to decrease the noise level of the plasma arc and to eliminate smoke development as much as possible led to underwater cutting. This method for high power plasma cutting with cutting currents above 100 amps has become so popular that today, many high power plasma cutting systems cut under water.
For underwater plasma cutting, the workpiece is immersed about 2 to 3 inches under water and plasma torch cut while immersed in the water. The smoke and noise level as well as the arc glare are reduced dramatically. One negative effect of this cutting method is that the workpiece can not be observed while cutting and the cutting speed is reduced by 10-20%. Further, the operator can no longer determine from the arc sound whether the cutting process is proceeding correctly and whether the consumables are producing a good quality cut.
Finally, when cutting in water, some water surrounding the cut zone is disassociated into oxygen and hydrogen, and the freed oxygen has a tendency to combine with the molten metal from the cut (especially aluminium and other light metals) to form metal oxide, which leaves free hydrogen gas in the water. When this hydrogen collects in a pocket under the workpiece, it creates small explosions when reignited with the plasma jet. Therefore, the water needs to be constantly agitated while cutting such metals.
Underwater Muffler
Based on the popularity of underwater cutting, in 1986 Hypertherm designed and patented an underwater Water Muffler which injected air around the torch, establishing an air bubble in which cutting could proceed. This became the air injected underwater cutting process which is most often used with oxygen cutting up to 260 amps. Use of this process increased cut quality and produced normal high cutting speeds achieved by water-line and "in-air" plasma cutting techniques.
Low-Amp Air Plasma Cutting (1980)
In 1980, plasma arc cutting equipment manufacturers in the Western hemisphere introduced equipment using air as the plasma gas, particularly for low-amp plasma systems. By early 1983, Thermal Dynamics launched the PAK3 and SAF introduced the ZIP-CUT. Both units were immensely successful, one in the USA and the other in Europe. This opened a new era for plasma arc cutting which increased the world market size about 50 times in the 1980s and created many new manufacturers. Plasma arc cutting was finally accepted as the new method for metal cutting and considered a valuable tool in all segments of the modern metalworking industry.
With the new thrust given to the plasma arc cutting industry through increased competition, many new improvements were introduced which made the process easy to use. The process was much more reliable and required less skill to operate. Power supply designs using solid state primary and secondary converter technology improved arc characteristics and reduced the size and weight of the systems. Hypertherm made other contributions with such patents as the blowback (or contact start) torch which eliminated high frequency arc starting, and the air-injected shield nozzle, which protected front end parts during metal piercing.
Oxygen Plasma Cutting (1983)
Since the traditional method of cutting steel was the oxyfuel process, it was logical that engineers that developed plasma arc cutting tried from the very beginning to use oxygen as the plasma gas. However, the very high temperatures at the tip of the electrode and the presence of pure oxygen caused all known electrode materials to rapidly deteriorate, so either no cuts could be made or only cuts of a very short duration This rendered oxygen and air unacceptable as plasma gases. Oxygen cutting therefore was abandoned in the early years of plasma cutting technology development. In early 1970, it was found that hafnium and zirconium in an industrially available form did resist the rapid deterioration which occurred with oxygen plasma arc cutting. Air and oxygen as plasma gases again became of extreme interest.
Hypertherm took this challenge and began R & D efforts in earnest. In 1983, the company succeeded with an improved torch design that made it possible to use oxygen as the plasma gas. A patent for water-injected oxygen plasma arc cutting was granted and oxygen plasma cutting became the latest development in plasma arc technology. Oxygen plasma cutting offered a wide range of dross-free cutting speed conditions, increased cutting speed by up to 30%, while operating at lower current levels, and produced smooth, square, and softer edges. The resulting cut edge was easier to fabricate by bending or welding. All steels, including high strength, low alloy steels, were now cut dross free with this new process.
The critical part continued to be electrode life, which, even when using hafnium, remained limited. However, the cut quality of steel cut with oxygen was superb, and most end users found the tradeoff of much higher speed and cut quality in the face of shorter electrode life to be acceptable. Costly post-cut dross removal operations often associated with nitrogen cutting were virtually eliminated with oxygen plasma.
Oxygen Injection Plasma Cutting (1985)
Oxygen injection plasma cutting circumvented the electrode life problem by using nitrogen as the plasma gas and injecting oxygen downstream at the exit of the nozzle as shown in Figure 6.
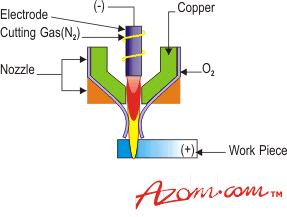
|
Figure 6. Oxygen injection plasma cutting.
|
This process was used exclusively on mild steel and slightly increased the cutting speeds. However, major disadvantages were lack of cut squareness, excessive kerf removal, short nozzle life, and limited versatility (mild steel). While this process is still being used at some locations, the limited increase in performance associated with it does not justify the extra expense of this rather complicated and delicate torch design.
Deep Water Plasma Cutting
In the 1990s, the atomic power industry was faced with two major challenges:
1. How to extend the life of existing nuclear plants
2. How to dismantle non-operational plants
While the power industry is working hard to develop procedures for repairing components in the reactor pool, the atomic commissions of several countries are searching for methods to cut the expended reactors and other components into small pieces for disposal.
Since the reactor and auxiliary components must be kept in a pool of water, all repair and dismantling must also he done underwater. Since a major part of the components are made of stainless steel, plasma cutting is a desired method. Overcoming the problems of underwater cutting has been a challenge to plasma equipment manufacturers with most refusing to get involved in the process. Hypertherm has worked with several contractors in the nuclear power industry to develop plasma cutting equipment for underwater cutting. In 1990 Hypertherm's PAC500 1000 amp plasma system was successfully used to cut up 4 1/2" (114 mm) stainless steel heat shields under 15 feet (4.56 m) of water at the Connecticut Yankee Nuclear power plant. Also in 1990, the MAX100 and MAX200 were used underwater in several locations at a depth of 25 feet (7.62 m). Plans are being made to cut below 100 feet (30.48 m) for offshore applications.
High Density Plasma Cutting (1990)
Laser cutting has become an important competitor in the metal-cutting industry because of its ability to produce high quality cuts with precise accuracy. To assume a place in the precision metal-cutting market, plasma equipment manufacturers have increased their design efforts to further improve the cut quality of their equipment.
In the early 1990s we saw the first high quality plasma installation of 40 to 90 amps, which produced a squarer cut and reduced kerf width with increased cutting speed. Some units have come from Japanese manufacturers. Hypertherm has introduced its HyDefinition technology to compete in this marketplace. The expectations are that a plasma cut will soon be of the same quality as a laser cut. Since plasma equipment is much lower in capital cost than a laser unit, we expect that this type of plasma cutting will become a major competitor in today's laser cutting market.
Laser Lasting Consumable Parts (1990)
Since air and oxygen plasma cutting have become more popular, the major issue has become the short life cycle of their consumable parts. The major manufacturers of plasma cutting systems are working on this issue. It is expected in the near future that the lifetime of air/oxygen electrodes will be extended substantially, reducing the cost of plasma cutting, and thereby making this process much more widely used for cutting steels. Hypertherm has introduced its LongLife technology on several models which offer greatly increased parts life.
Conclusion
From this review, it is clear that the plasma process has made astonishing progress in the last thirty-five years, particularly in the last five years. Today, three pronounced trends can be detected:
1. The market for light hand-cutting units with current levels below 200 amps will continue to expand. This expanding market will attract more competitors which will produce improved products and broaden the market for low-amp air plasma.
2. The market for cutting machines and robots will continue to seek high quality, close tolerance cutting from plasma cutting systems. Attractively priced oxygen plasma and simpler and lighter low-amp units will compete favourably with laser-cutting equipment. Hypertherm, with its technical leadership, will continue to play a dominant role in this market segment.
3. Research and development on consumable parts and cutting torches will continue, constantly extending the life of consumables and improving cut quality.
As plasma cutting approaches its mature stage, the industry is challenged to provide more accurate torches and consumable parts, and power sources of advanced technology. In general, it is expected that the plasma cutting market will continue along a high growth trend for the foreseeable future.
|