Aluminium is the third most abundant element after oxygen and silicon, and the most common metal. It forms some eight per cent of the earth’s crust. The ore is mined as bauxite, which contains aluminium oxide, together with oxides of silicon, iron and other metals.
Aluminium Mining
Most mining for bauxite is open-cast (figure 1) and takes place in tropical areas such as Northern Australia, West Africa and the West Indies. The mining companies apply strict environmental practices to ensure that the bio-diversity of the mined areas is protected. The topsoil is removed and carefully retained. Once the bauxite has been extracted the topsoil is replaced and re-planted with species native to the area. In tropical regions, with the help of such planting programmes, the former vegetation is quickly re-established through rapid natural growth.
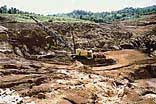
|
Figure 1. An open-cast bauxite mine.
|
Dependent upon the nature of the local land use, some mined-out areas are restored by the mining companies to become new fertile farmland, providing valuable crops and pasture for the local inhabitants.
Aluminium Production
The aluminium production process involves two main stages:
• Alumina, or aluminium oxide (Al2O3) is refined from the bauxite in a caustic soda/high temperature process.
• Aluminium is obtained by an electrolytic smelting process, which breaks down the alumina into molten aluminium and oxygen. The silver-coloured molten aluminium is syphoned off into furnaces where other elements are added to produce particular alloys, before being poured into moulds to form ingots.
In round figures it takes 4 tonnes of bauxite to make 2 tonnes of alumina, which makes 1 tonne of aluminium.
The primary production process consumes about 14kwh per 1 kg of aluminium. Approximately 60 per cent of world aluminium production uses hydro-electric power, rather than non-renewable energy sources. Producing aluminium by recycling uses only 5% of the energy used in primary production: recycling aluminium, which has always been an important part of the industry, makes sense both commercially and environmentally.
Rolling the Aluminium Foil
The ingots of aluminium are heated to make them more malleable, rolled, passing backwards and forwards through large rollers as the slab gets thinner and thinner, and longer and longer. This metal strip is hot rolled to a thickness of 2 to 4 mm (2000 to 4000 microns) and then coiled, before being cold rolled to metal thicknesses of between 6 and 400 microns. The thinnest foil used for wrapping chocolates may be only 6 microns thick (about one-eighth the thickness of newspaper!), with household wrapping and cooking foil between 11 and 18 microns, lidding foil between about 30 and 40 microns, and foil for foil containers generally between 40 and 90 microns.
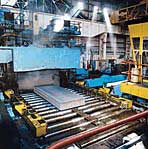
|
Figure 2. An aluminium ingot before rolling.
|
The foil is then annealed by a thermal process to make it pliable: great care is taken to ensure the correct balance between flexibility and strength for different applications.
Alloys
The most common foil alloys - the 1000, 3000 and 8000 series - contain between 0.5% and 1.5% iron, 0.1% and 0.7% silicon and 0.02% to 1.5% manganese. Up to 0.2% copper may be added when additional strength is required.
|