Jun 13 2002
Topics Covered
Background
Structure
Key Properties
Applications
Heart Valves
Deposition of Pyrolytic Carbon Coatings for Heart Valves
Small Orthopaedic Implants
Background
The identification of pyrolytic carbon as a suitable material for heart valves happened almost accidentally. In 1966, Dr. Bokros was working on pyrolytic carbon coatings for nuclear fuel particles. He happened to read an article by Dr. Gott who was at the time working on a carbon-based paint for use in cardio-vascular applications.
Shortly after this the two collaborated and modified the material that Bokros had been working on to give it the durability required for Gott’s application.
Prior to this time, artificial heart valves had been made from metals and plastics that had short lives due to blood clotting or wear. Today, pyrolytic carbon remains the most popular material available for artificial mechanical heart valves, being used to produce over 4 million devices, covering 25 different designs.
Structure
Pyrolytic carbon belongs to the family of turbostratic carbons, which have a similar structure to graphite. Graphite consists of carbon atoms that are covalently bonded in hexagonal arrays. These arrays are stacked and held together by weak interlayer binding. Pyrolytic carbon and other turbostratic carbons differ in that the layers are disordered, resulting in wrinkles or distortions within layers. This give pyrolytic carbon improved durability compared to graphite.
Key Properties
- Biocompatible, i.e. does not elicit any adverse reactions when implanted into human bodies
- Thromboresistant i.e. resists blood clotting
- Good durability
- Good wear resistance
- Good strength
Applications
Heart Valves
As mentioned above, pyrolytic carbon has been used for making artificial heart valves. These actually consist of thick pyrolytic carbon coatings deposited onto graphite.
Up until 1996, pyrolytic carbon heart valves consisted of silicon-alloyed pyrolytic carbon (containing from 3-8wt% silicon). The silicon was added to improve properties such as stiffness, hardness and wear resistance. Its addition had no adverse affect on biocompatibility.
In 1996, a pure carbon implant material was introduced onto the market, also developed by Dr. Bokros and his team. An improved material was made possible due to a newly developed production process, which was both tougher and stronger then the silicon alloyed variant. It had the added advantage that is was more biocompatible as it did not contain silicon carbide inclusions, which could possible compromise the thromboresistance of the carbon.
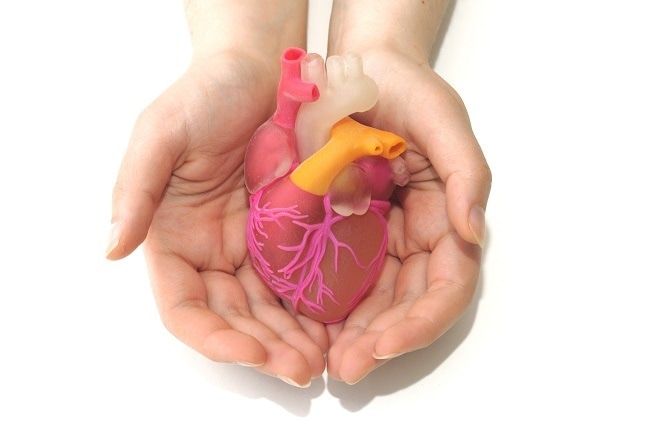
Pyrolytic carbon has ben used to make artificial heart valves. Image Credit:Shutterstock/The World in HDR
Deposition of Pyrolytic Carbon Coatings for Heart Valves
Pyrolytic carbon coatings are made by co-depositing carbon and silicon carbide onto suitable substrates using chemical vapour deposition processes. Deposition is carried out in a fluidised bed furnace, fed with silicon carrier gas and a hydrocarbon.
Small Orthopaedic Implants
Pyrolytic carbon is also suited to small orthopaedic joints such as fingers and spinal inserts.
Primary author: AZoM.com