Aug 16 2002
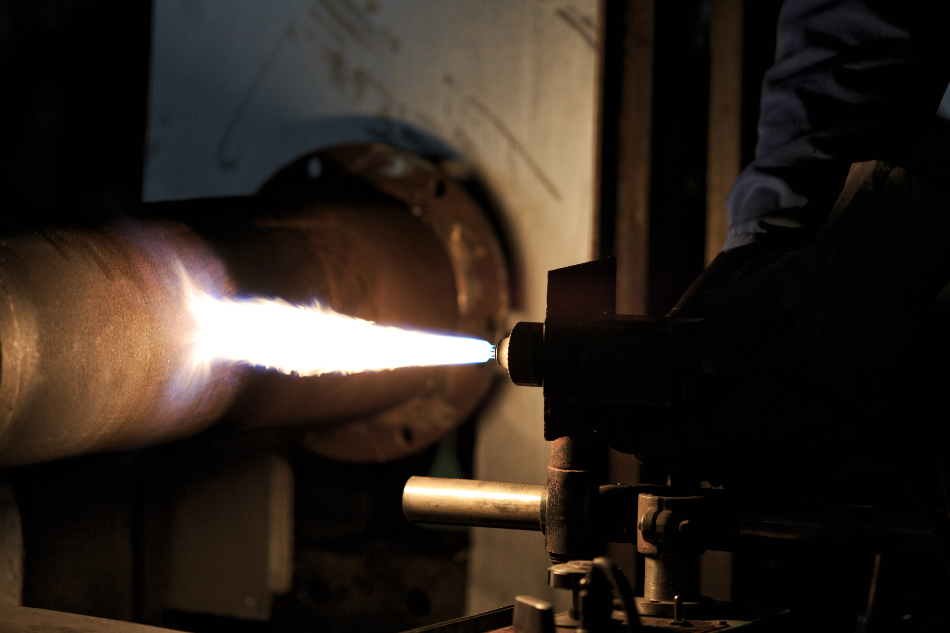
Kimtaro / Shutterstock
Researchers’ interest in thermal spraying varies from the very practical to the uncommon and theoretical studies. In between this lies the July 2000 issue of Materials Research Bulletin titled “Thermal Spray Processing of Materials.” The seven articles in this issue include everything from the fundamentals of tools and process selection, through to modeling and dynamics of deposit formation or fabrication of fuel cells, spraying of polymers, or barrier coatings for gas turbine engines.
This article provides a summary of most of the above-mentioned areas.
The Process
In the thermal spraying process, particles of 1 to 50 µm are partially melted and accelerated to high velocities by an arc or a flame. The particles get splattered onto a surface, forming a layer whose quality is evaluated by the porosity, oxide content, and bond strength to the substrate. The material sprayed can be ceramic, metal, or polymer. Table 1 illustrates the temperature, velocity, and standard features for five types of sprays.
Table 1. Characteristics of some thermal spray processes. Source: Institute of Materials Engineering Australasia.
Type |
Temperature C |
Velocity m/s |
Features |
Combustion |
3000 |
40 - |
100 |
Porosity and oxidation |
High-Velocity Oxy-Fuel |
3000 |
400 - |
800 |
Dense, good adhesion, compressive stress |
Two-wire arc |
3000 - 6000 |
50 - |
150 |
Dense, thick |
Plasma |
5000 - 25,000 |
80 - |
300 |
Ceramics porous |
Cold spray |
Ambient |
400 - |
800 |
Dense, compressive stresses |
Differences Between Thermal Spray Processes
The supersonic velocity of the HVOF spray delivers a thin, dense, and well-bonded splat. Variants of the gun are being created for a number of applications. Other conventional approaches involve melting two wires in an arc or feed powder into a high-speed plasma gas stream and, for high-performance applications, using inert or low-pressure gases.
Current advancements include radio-frequency induction plasma with its high temperatures or the opposite process with a high velocity, low temperature, localized spray, which offers pure, dense material with high compressive stresses.
Coating Structure
Sprayed layers are anisotropic and resemble a brick wall comprising interlocked splats. The key defects are microcracks or pores in brittle materials, while porosity and oxides characterize metal sprayed layers.
Flaws arise from metal oxidation, unmelted particles, low-velocity impact, isolated large particles, and cold-induced fragmentation of splats. The evaluation for quality needs a range of methods, perhaps including thermal conductivity, porosimetry, or even neutron diffraction in research work.
Automotive uses are a key area of application, including oxygen sensors and piston rings. Although it is now in the research stage, the high-pressure shock (up to 30 GPa) generated while splattering a particle enables developing high-pressure phases, which are stable in the nanocrystalline form at room temperatures, for example, 5 to 10 nm diamond phases developed from a sprayed nickel-graphite powder.
Other applications being developed include the formation of multi-layers for sensors, spray synthesis, and engineering metal layers with resistivity two or more times the bulk resistivity.
Characterizing Thermal Spray Processes
Modeling has revealed the complexity of the gas-particle interactions and, for instance, the distribution of non-molten particles in a spray. It also demonstrates how hard it is to ensure that a new spray process stays in the permissible narrow window, and shows why it takes time to formulate new processes.
HVOF modeling is challenging due to the supersonic properties of the gas stream and the work needed to characterize the combustion process. But particle vaporization is not typically as much of a concern as is plasma because the gas temperatures are lower, particles are supplied faster, and the thermal conductivity of the particles is higher in HVOF.
Measurements of in-flight particle size, temperature, and velocity performed to verify model calculations involve using methods such as laser Doppler velocimetry, radiance comparisons, and considerable computation effort. The approaches must include the difference in temperature of several hundred degrees and velocity differences of over 100 m/second.
Residual Stresses in Thermal Spray Coatings
During the dynamic formation of the coating, tens of microseconds are taken up for splattering, a few milliseconds for layer formation, and a few seconds for the subsequent gun pass. Although the end result can be seen by sectioning a coating, it is somewhat difficult to evaluate the dynamic processes behind the micron size particle splattering itself onto a cold surface.
Firstly, models have to deal with either the splat or the layer piling process, generally with simplifications. It is really challenging to determine mechanical properties such as surface roughness, particle size, direction, shape, and composition at higher temperatures.
The research helps gain insights into residual stresses, which is a major determinant of the spallation, fatigue, and thermal cycling resistance performance of thermal spray coatings.
Residual stresses originate from substrate blasting or quenching of the splat on a cool substrate. Although it is lower than 50 MPa for ceramics due to microcracking, sturdy alloys could have stresses up to 300 MPa.
The discrepancy in thermal expansion coefficients between surface and spray materials also leads to stress, which deteriorates with a higher temperature difference between spray and ambient temperatures, and when temperature gradients exist in the sprayed part.
Applications of Thermal Spray Coatings
The deposition of thermal barrier (ceramic) coatings on gas turbine engine components and the spray fabrication of fuel cell components have been discussed in various studies. These ceramic coating properties are governed by the complex interaction of ceramic sintering and creep, elastic modulus kinetics and thermal conductivity, bond coat oxidation and thermal fatigue.
Thermally Sprayed Polymers
Reports have indicated that the practice of polymer spraying has increased. The materials coated include PE copolymers, ketones, polyethylene, polyester, fluoropolymers, nylon, and liquid crystal polymers. Plasma, combustion, and HVOF processes have all been used, and the operating conditions must be chosen to maintain the window between polymer degradation and poor coalescence of particles.
The coating temperature must be selected to enhance the essential properties as maximum density occurs at a lower temperature than maximum hardness and toughness.
A majority of the polymer applications involve corrosive environments, thus making it crucial to ensure full coalescence and to avoid porosity and splat interfaces. Coating applications include magnetic or wear-resisting polymer composite materials.