Textured surfaces are found in everyday products, from steel body panels and bearings to book covers and quilted toilet paper. Although a number of processes can be used to achieve the desired surface texture, each has drawbacks, restricting wholesale introduction. Ink-Jet Texturing Overcoming the limitations of previous technologies, ink-jet texturing is a new process developed by Intexia Lid, capable of producing non-random (deterministic) textures on both flat and cylindrical metallic parts, irrespective of the hardness of the metal. Furthermore, there is no heat-affected zone or displaced material, making it suitable for a large number of applications, including directly textured bearings and seals, automotive steel and aluminium sheet, basic embossing rollers, and basic injection mould dies. Other Texturing Processes Although the paper industry has long recognised the benefits of texturing, other industries such as steel, automotive and textiles have been held back by the limitations of current processes. These include random methods, such as shot blasting, electro-discharge texturing and grinding (sometimes referred to as mill finish), and deterministic procedures such as photochemical etching, laser machining and electron beam texturing. Why Surface Texturing is Used Defined as ‘the modification of the functional properties of the surface of an object’, surface engineering is typically undertaken to change the physical or visual properties of a surface. These properties, and the reasons for wanting to change them, are many and varied. There may be a requirement to reduce (or even increase) the friction between mating parts, to improve the formability of a metal sheet, to increase the surface area of a substrate (perhaps to improve the adhesion of a coating), or to enhance its decorative appeal and reduce its sensitivity to surface scratches. Surface engineering is frequently taken to mean the application of chemical processes such as coating, nitriding or ion implantation. Yet all of the above benefits, and more, can also be achieved by surface texturing - modifying the topography of the surface instead of its chemistry. The Ink-Jet Texturing Process Ink-jet texturing is a remarkably straightforward process. A controlled mask is printed on the surface of the part, followed by a chemical or electro-chemical machining process to etch away those parts of the surface that remain exposed. The standard embodiment of ink-jet texturing, in which the surface is etched to a single depth, is termed 2D texturing. The texture pattern could be of a regular geometry for functional purposes (such as sheet steel) or a decorative pattern for embossing. Essentially it could be any image generated in the software and downloaded to the ink-jet printhead. The Ink-Jet Texturing Machine The new texturing machine developed by Intexia uses the latest high-resolution, drop-on-demand inkjet printheads. The machine incorporates both the ink-jet printing and electro-chemical etching systems. Designed for maximum versatility, it is capable of texturing a range of both flat and cylindrical components in a variety of sizes. At the heart of the print system is a 126 nozzle ink-jet head, which is capable of printing using a range of different fluids. Applications Ink-Jet Texturing in Engine Components Intexia’s high-resolution system offers a wealth of potential applications for ink-jet texturing in engine components. The surfaces of many of these parts have to be textured to retain sufficient friction, or to achieve the desired level of lubrication for the parts to function efficiently. Some companies in the automotive industry are currently investigating potential new technologies to enable this application of surface textures. Ink-jet texturing could have significant advantages compared to laser etching, including surface smoothness and pattern design. Furthermore, laser etching uses high temperatures to displace the unwanted metal, which can decrease the quality of the object being created. With ink-jet texturing, the unwanted metal is dissolved into solution, therefore eliminating any formation of heat-affected zones. Ink-Jet Texturing for Permanent Traceability Another area of potential application is component marking for permanent traceability. Conventional ink-jet codes may wear off, break down at high temperatures or be attacked by chemical contact. Thermal and mechanical processes may distort thin parts or leave material tens of microns proud of the marked face, which is potentially catastrophic if a good thermal contact is critical. An inkjet textured code would be permanently recessed into the surface, yet retain the flexibility of ink-jet and laser for incremental serialising. This type of texturing can also be used in mechatronics. Origins of the Ink-Jet Texturing Technology The overall design of the ink-jet texturing system follows extensive research by the University Edinburgh. In the early 1990s, the School of Engineering at the university was commissioned by the Ford Foundation to investigate alternative methods for texturing the temper mill rollers used in the cold rolling of automotive sheet steel. The processes currently used include shot blast texturing, electro-discharge texturing, electro-chromium deposition and electron beam texturing (EBT) Of these, the only process that can produce deterministic textures is electron beam texturing. Here, an electronbeam, acting in a high vacuum, is used to create toroidal peaks on the surface of the roller by locally melting and resolidifying the steel. These are then rolled into the sheet to create ‘doughnut’ shaped craters. Lasers were once used in a similar manner, but the process proved to be slow, expensive and unreliable, and as a result it has almost been completely phased out by the steel industry Surface Texture and Formability for Automotive Panelling In sheet steel production, surface texture can enhance the formability, painted appearance and the adhesion of coatings. A number of studies into auto body steel have suggested that formability especially when deep drawing, is enhanced by the provision of isolated micro-craters in the surface of the sheet. These act as small hydrostatic lubricant reservoirs and debris traps to reduce galling and provide more uniform frictional properties. Other studies have linked poor painted image clarity (‘orange peel’ effect) to high levels of surface waviness (typically features with a wavelength of 0.8-2.5 mm). In a follow up project carried out by the university and sponsored by the EPSRC, British Steel and Domino Printing Sciences, small-scale pilot mill trials were carried out in a European steel mill. Here, the low wear rate, regular structure and low waviness were particularly impressive. Figure 1 shows surface plots comparing the roughness and waviness of sheet steel rolled with ink-jet textured and electron-beam textured rollers. The measurements, taken with a Zygo NewView non-contact interferometer, represent surface areas of 8 x 8mrn and have been digitally filtered with a cut off of 0.8mm. The ink-jet textured sheet has particularly low levels of waviness - important when trying to reduce the orange peel effect in painted finishes. The ink-jet texturing system developed at the University of Edinburgh and used for these trials was based around a high resolution continuous-ink-jet printer, typically used for production line coding. This had a high print speed and, with solvent-based inks, deposited a quick drying mask onto steel substrates. While adequate for autobody sheet, it did not have the resolution, accuracy or ink durability for other applications, unlike the new machine. 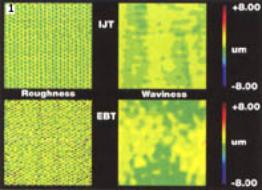 | Figure 1. Surface plots comparing the roughness and waviness of sheet steel rolled with ink-jet textured and electron beam textured rollers. | The Future of Ink-Jet Texturing Following the receipt of a SMART grant from the Scottish Executive, Intexia is now developing a new variant of the ink-jet texturing machine for embossing applications, such as rolling vinyls and paper products. Called the 3D-IJT it uses multiple masking and etching stages to etch a more three-dimensional form into the surface of the part. In the longer term, the company hopes to market the technology for any application in which a controlled surface texture is required, such as automotive dashboards, medical implants, hygiene products and greetings cards. |