What do plastic spectacle lenses and PET bottles have in common? They are both light, almost unbreakable and often preferred to their equivalent glass products. Spectacle lenses are also required to be scratch-resistant and glare-free, while PET bottles must be chemically resistant and impermeable to gases. As no single grade of plastics has all these properties, the answer is to treat the plastics products in such a way that, while retaining their basic benefits, they gain new or improved properties. This is exactly what Schott HiCotec, a division of Schott Spezialglas GmbH, is doing with its patented Plasma Impulse Chemical Vapour Deposition (PICVD) process.
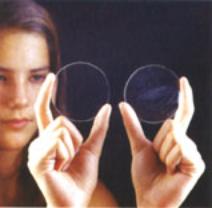
|
Figure 1. Anti-scratch coatings after the steel wool test, coated (left) and uncoated (right)
|
What Materials Can be Coated Using Plasma Impulse Chemical Vapour Deposition
Although developed 20 years ago by Schott Glas, PICVD has been very successful in coating high volume glass products, such as cold light reflectors, energy saving lamps and pharmaceutical vials. To expand the application areas of PICVD) into plastics Schott HiCotec was set up as a new division. Very quickly it succeeded in modifying the original PICVD process and applying bonded homogeneous coatings - in particular glass-like SiO2 and TiO2 oxide coatings to a broad range of plastics (e.g. PET, PMMA, PC, COC, PP and HDPE). The result is that plastic can now have all the positive properties of glass. In the case of plastic lenses and display covers it is now possible to produce anti-scratch and antireflective coatings, while in the case of plastics packaging, a PICVD coating creates a barrier against the passage of gas oxygen can no longer get in, and released carbon dioxide cannot get out. Consequently the contents have a longer shelf life with no effect on their taste.
How Does the Plasma Impulse Chemical Vapour Deposition Work?
How then, does the process for coating plastics work? The items to be coated are placed in a vacuum chamber into which a gaseous coating material is introduced using gas lances. Microwaves are then beamed into the chamber, igniting the plasma and breaking down the gas, causing the carried material, such as SiO2 or TiO2 to be deposited on the surface of the item in the chamber. Up to this point the process is the same as the conventional CVD process. The special part of the PICVD process is the ‘I’ (Impulse) because, in this case, the plasma is pulsed. This means that the coating is built up a in a series of small stages, which produces an extremely dense and homogeneous coating. Another advantage is the precise control of the process. Very low process temperatures can be used - it is possible to carry out the process at room temperature - and the chemical composition of the reaction mixture can be changed between pulses. Consequently, in the course of one process operation, different layers can be combined to produce a made-to-measure multilayer system.
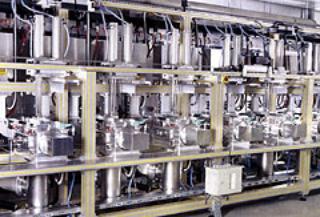
|
Figure 2. A PICVD coating unit.
|
Multilayer Systems
A typical multilayer system for the display cover of a mobile telephone, an electronic measurement device or an in-car navigation system that would consist of, for example, a bonding agent layer, an anti-scratch layer and an anti-reflective layer. The bonding agent layer ensures that the subsequent layers remain firmly bonded to the display, even when this expands or contracts with changes in temperature. With the anti-scratch layer the display cover becomes as scratch resistant as if it were made of glass, meaning it can be cleaned without the need for any special precautions. The anti-reflective layer consists of a series of coatings comprising alternating layers of SiO2 and TiO2. This multilayer system forces the incident light to pass through several barrier layers. At each barrier, part of the light is reflected. The reflected parts of the rays superpose each other as they exit the layers of coating, resulting in the light practically extinguishing itself. This means that the proportion of light reflected from the surface of the display is less than one percent of the incident light. It becomes virtually invisible to the viewer, who has a clear view of the information required whether it be a measurement, a caller’s telephone number or a recommended itinerary.
Coating Thickness and Uniformity
The thickness of multilayer systems of this type, i.e. those that comprise a bonding agent layer, anti-scratch and antireflective coatings, amounts to no more than a few fractions of a micrometer and it only takes a few minutes to apply the coatings. Owing to the pulsed nature of the plasma, the gaseous coating material is distributed uniformly throughout the reaction chamber, making it possible to coat an item from both sides at the same time. This means that PICVD technology can apply coatings quite economically and can be tailored to specific requirements.
Plasma Impulse Chemical Vapour Deposition as Part of a Production Process
In addition to providing individual coatings to order, Schott HiCotec also supplies complete machines. The company designs and builds PICVD machines that enable the coating to be incorporated in the manufacturing process of the plastics product. These machines have had a particularly good take up in the packaging industry, with packaged products ranging from food, cleaning agents and cosmetics to pharmaceuticals.
Plasma Impulse Chemical Vapour Deposition in Packaging Applications
In most packaging uses the PICVD coating has a barrier function. For example, in the case of glass packaging it increases its chemical resistance to alkaline solutions and acids, while with plastics packaging it prevents the exchange of oxygen and carbon dioxide. In the case of PET bottles, a 50nm‑thick PICVD coating of SiO2 is sufficient to increase the shelf life of beer or fruit juice many times over.
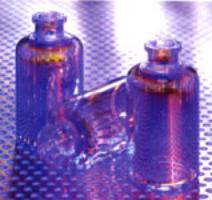
|
Figure 3. Pharmaceutical packaging bottles coated using PICVD barrier coatings.
|
Ensuring Uniformity on Plastic Bottles
How is a complex, three-dimensional object such as a plastic bottle coated with such a wafer thin barrier coating? It is the pulsed plasma that ensures that the different layers are applied uniformly. However, optimum conditions are achieved by using the ‘single user concept’ - one bottle per reaction chamber. Each item is then subjected to exactly the same boundary conditions and the coating quality remains constant. The plastics bottle itself acts as the reaction chamber with the reaction gas mixture being introduced into the inside of the bottle via a gas lance. This results in only the inside being coated, with the advantage that the internal coating cannot be damaged in handling or transport, and the plastic bottle has no direct contact with its contents. In addition, this process avoids coating the process chamber too.
How Plasma Impulse Chemical Vapour Deposition in a Continuous Process
To integrate the PICVD coating of plastics containers in an economic mass production system, the machines operate on a continuous flow basis. The containers are loaded into the vacuum chambers in rapid succession and the internal coating - a bonding agent layer plus the SiO2 barrier layer - is applied. A complete coating cycle lasts no more than a few seconds. To guarantee the layer quality on a long-term basis, the whole process is subject to comprehensive monitoring - from the gas composition of the plasma via the process parameters right through to long-term stability including temperature, pressure and gas flow. This also includes monitoring maintenance and service routines.
An excellent example of the integration of PICVD coating into a mass production system is a new type of machine for coating PET bottles. Developed as the result of co-operation between Schott HiCotec and SIG Corpoplast GmbH, it can coat up to 10,000 PET bottles per hour. The machines are being marketed for the food and drinks market exclusively by SIG Corpoplast. The first machine for one of SIG Corpoplast’s main customers has just been constructed and will shortly go into production.
Summary
PICVD coated PET bottles should make up a growing proportion of the plastics bottle market. For one thing they meet all the drinks industry's requirements as regards barrier performance, bonding of the layers and economy. There are also benefits from the user’s point of view in that they are light, unbreakable and transparent. And PET bottles are 100% recyclable.
Clearly, PICVD technology is making a decisive contribution to the use of plastics products, since coating using this method is providing new and improved properties for plastics products.
|