QinetiQ has recently completed sea trials of a new composite propeller in Falmouth Bay, UK. With a 2.9 metre diameter it is the world’s largest propeller. However, despite its immense proportions it weighs significantly less than an equivalent traditional ship’s propeller made from nickel aluminium bronze (NAB). The reason - new lightweight composite materials. 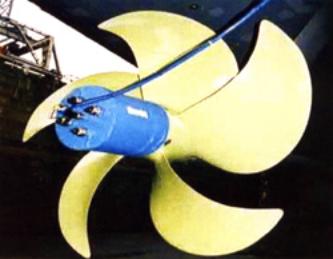 | Figure 1. The 2.9m diameter composite propeller on the RV Triton triple hull warship. | Composite Propeller Construction The propeller has five composite blades bolted and bonded to a NAB hub. The materials used within the composite are commercially available, and it is the development of the right mix of fibres, resin and laminate lay-up that provide the desired mechanical and environmental performance for marine application. The extensive development trials included durability testing in the marine environment, and water uptake and fouling tests. The effects of cavitation, impact and environmental fatigue were also studied. The Vessel that The Composite Propeller was Tested On The propeller, designed for QinetiQ’s trimaran warship prototype, RV Triton, was developed to explore the application of composite materials for marine propulsion. RV Triton is the world’s largest motor powered triple-hull vessel. Optimising Properties of the Composite Propeller Catherine Kane, Technology Chief of Marine Structural Concepts at QinetiQ, described the optimisation process of the materials used. ‘The fundamental mechanical properties required in this application include stiffness, strength and fatigue performance. The structure was optimised to be stiffest along the length of the blade (i.e. in the radial direction of the propeller) and strong enough to have a significant factor of safety upon the design load. On a materials basis, the composite was about half as stiff as NAB but had a similar strength (see figure 2). On first inspection, one might have concerns about the stiffness, but the specific stiffness of these materials makes them very attractive. Structural stiffness was regained through improved design of the propeller itself. Additionally, the fatigue performance is largely dependent on the performance of the metal insert at the root. During tests, failure has been initiated by flaws in the NAB while the composite has remained undamaged.’ 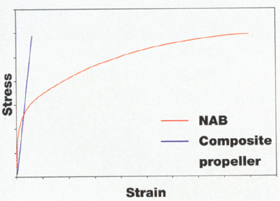 | Figure 2. Stress-strain graph comparing nickel aluminium bronze and the new composite material. | Improved Cavitation Performance of the Composite Propeller A reduction in the perennial problem of cavitation damage pitting caused by pressure gradients in water forming bubbles of vapour on the surface of the propeller, which then collapse and cause repetitive localised stress was a priority for the design. Theoretical models give a cavitation inception speed of 30% higher for the composite propeller design, compared with the original NAB propeller. This was found to be a result of the improved shape, rather than the use of new materials - though the combination provides a number of benefits, explains Colin Podmore, Project Manager. ‘The use of the lighter composite materials meant that the blades could be thicker without significantly adding to the weight of the propeller. Thicker blades offer the potential for improved cavitation performance, so reducing vibration and underwater signatures.’ Improved Life Expectancy of the Composite Propeller The composite propeller is expected to last for the lifetime of the vessel - 25 years. In contrast, an NAB propeller would be expected to suffer cavitation erosion and corrosion and need to be replaced periodically. Additional trials need to be carried out to address the durability issues and fully validate the long-term performance. Expanded Applications for the Composite Propeller The composite propeller has aroused the interest of a number of MoD and defence companies. ‘It is hoped that we will be able to grow interest in the commercial sector as well,’ said Kane. Summary Qinetiq are now looking at ways of exploiting their composite materials, and it is expected that it will find a natural home among other marine applications, such as secondary structures on ships and submarines. It could also provide cost savings. ‘The processing techniques allow for the production of complex shapes and so it is probable that unit production costs can be reduced if sufficient numbers are required, by reducing the postproduction machining and joining that is commonly needed for metallic components,’ said Kane. |