Boron nitride (BN is a synthetic material, which although discovered in the early 19th century was not developed as a commercial material until the latter half of the 20th century. Boron and nitrogen are neighbours of carbon in the periodic table - in combination boron and nitrogen have the same number of outer shell electrons - the atomic radii of boron and nitrogen are similar to that of carbon. It is not surprising therefore that boron nitride and carbon exhibit similarity in their crystal structure.
In the same way that carbon exists as graphite and diamond, boron nitride can be synthesised in hexagonal and cubic forms.
The synthesis of hexagonal boron nitride powder is achieved by nitridation or ammonalysis of boric oxide at elevated temperature. Cubic boron nitride is formed by high pressure, high temperature treatment of hexagonal BN.
Hexagonal boron nitride (h-BN) is the equivalent in structure of graphite (see figure 1). Like graphite its plate like microstructure and layered lattice structure give it good lubricating properties. h-BN is resistant to sintering and is usually formed by hot pressing.
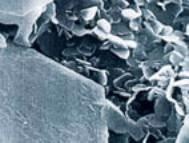
Figure 1. h-BN powder (photo courtesy of Ceram Research Ltd)
Key Properties
Hexagonal Boron Nitride (h-BN)
h-BN has excellent lubricating properties
In the hot pressed state, h-BN is readily machinable using conventional metal cutting techniques, hence complex shaped components can be fashioned from hot pressed billet.
Providing oxidation of the surface can be prevented, h-BN is not wetted by most molten metals, glasses and salts and hence has a high resistance to chemical attack.
High dielectric breakdown strength
High volume resistivity
Good chemical inertness
Cubic Boron Nitride (C-BN)
C-BN is the second hardest material known, inferior only to diamond
High thermal conductivity
Excellent wear resistance
Good chemical inertness
Table 1. Typical properties for hexagonal and cubic boron nitride.
Property |
h-BN |
C-BN |
Density (g.cm-3) |
2.3 |
2.2 |
Melting Point (°C) |
3000 (dissociates) |
|
Hardness (Knoop 100 g) (kg.mm-1) |
400 |
|
Modulus of Rupture (MPa) |
100 (ll to press dir)
50 (⊥ to press dir) |
110 |
Youngs Modulus (MPa) |
20 - 103 |
|
Thermal Expansion Co-eff (RT-1000 °C - x10-6) (°C-1) |
1 (ll to press dir)
4 (⊥ to press dir) |
3.8 |
Thermal Conductivity (W/m.K) |
20 (ll to press dir)
27 (⊥ to press dir) |
|
Dielectric Breakdown Strength (kV.mm-1) |
35 |
|
Dielectric Constant |
|
4.1 |
Vol Resistivity (ohm.cm) |
108 - 1013 |
|
Note: Data for h-BN were taken from a hot pressed sample. As this is a highly directional forming process, properties are anisotropic i.e, differ in directions relative to the pressing direction. For this reason, some values are higher than those reported in the attached property table.
Applications
Electrical insulators
The combination of high dielectric breakdown strength and volume resistivity lead to h-BN being used as an electrical insulator however its’ tendency to oxidise at high temperatures often restrict its use to vacuum and inert atmosphere operation.
Crucibles and reaction vessles
Its chemical inertness leads to application as thermocouple protection sheaths, crucibles and linings for reaction vessels though as above oxidation must be avoided.
Moulds and evaporating boats
h-BN is used in bulk form or as a coating for refractory moulds used in glass forming and in superplastic forming of titanium (see figure 2). It is also used as a constituent in composite materials e.g. TiB2/BN composites for metal evaporation boats, and Si3N4/BN for break rings in continuous casting of steel (see figure 3).
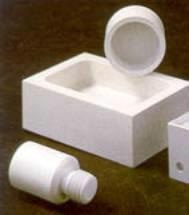
Figure 2. Crucible and boat for molten steel (photo courtesy of Ceram Research Ltd)
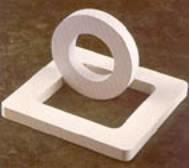
Figure 3. Breakrings for horizontal continuous casting of steel (photo courtesy Ceram Research Ltd)
Hot isostatic pressing
Its refractoriness combined with the fact that it is not wetted by molten glass lead to h-BN being used in the production of hot isostatically pressed (HIP’ed) material, most notable ceramics. In this application preformed parts are coated in h-BN prior to glass encapsulation and HIP’ing. This protects the part being HIP’ed from actually coming into contact with the glass, which in turn makes it easier to remove after HIP’ing.
Machine cutting tools and abrasives
Cutting tools and abrasive components particularly for use with low carbon ferrous metals have been developed using C-BN. In this application the tools behave in a similar manner to polycrystalline diamond tools but can be used on iron and low carbon alloys without risk of reaction.
Substrates for electronic devices
C-BN is used for substrates for mounting high density and high power electronic components where the high thermal conductivity achieved allows efficient heat dissipation.
Wear resistant coatings
Due to its high hardness and excellent wear resistant properties, coatings of C-BN have been developed.
About Goodfellow
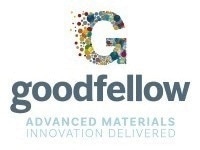
Goodfellow supplies metals, ceramics and other materials to meet the research, development and specialist production requirements of science and industry worldwide.
The Goodfellow group consists of four companies. The main administration, research laboratories and workshops are located at the Company's headquarters in Cambridge, England. The subsidiary offices in America, France and Germany provide an additional service.