The MSR™ MicroSphere Refiner, a cGMP piece of equipment was designed by PSL to provide drug manufacturers with an all-in-one, innovative solution to carry out a variety of aseptic procedures at different scales with their microspheres. Polymeric microspheres are complex injectable drugs that provide sustained and controlled release of the drug load into a patients body, offering patient well-being and superior treatment adherence than usual delivery methods.
The MSR™ helps overcome the challenges of polymeric microsphere processing such as filtration and drying inefficiencies, poor batch reproducibility, and lack of sterility assurance.
PSL analyzed systemic industry difficulties and gained a deeper understanding of microsphere processes with end users in the field. Using a Quality-by-Design (QbD) methodology, focusing on the properties and process behavior of polymeric microspheres, pioneering MSR™ technology can now be used to conquer the challenges in microsphere scale-up development.
Download the Brochure for More Information
Features and Benefits
An All-in-One Solution
Drug producers can use the MSR™ MicroSphere Refiner, a piece of Current Good Manufacturing Practice (cGMP) equipment, to finish various aseptic operations with their microspheres at different scales.
Because it can perform the following tasks in a single system, it naturally maximizes product recovery, batch repeatability, and production flexibility:
- Classification, filtration, and dewatering of microspheres
- Washing microspheres
- Drying microspheres, including freeze-drying
- Microsphere discharge and recovery
Batch Reproducibility – At the Touch of a Button
The MSR™ MicroSphere Refiner is a completely automated device that eliminates the need for manual handling of products during the production process. This minimizes the possibility of human error while optimizing batch-to-batch reproducibility.
At the push of a button, production can begin, and pre-planned process recipes can be followed.
Thanks to the PSL automation and configurator platform, drug producers can pre-design and pre-load software process recipes with the necessary process parameters appropriate for their particular production needs. This increases the speed and adaptability of their production operations.
PSL can comply with major international software automation practices and regulations, such as GAMP5 (Good Automated Manufacturing Practice, version 5 by ISPE) and 21 CFR Part 11, developed by the US FDA for electronic records and signatures.
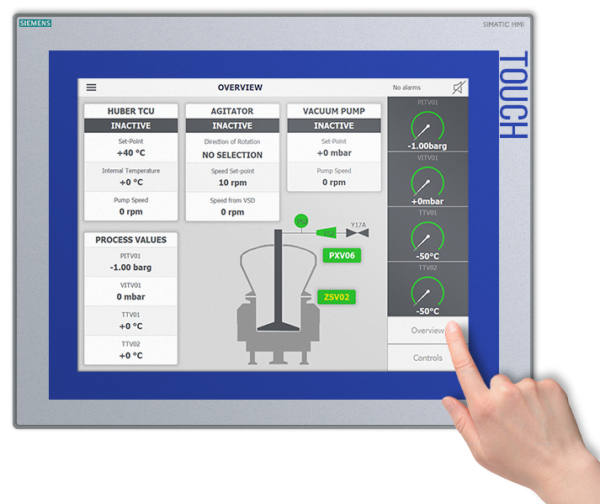
Image Credit: Powder Systems
Product Recovery – A Crucial Requirement
Because microspheres are an extremely expensive element in the development and production of drugs, pharmaceutical companies must maximize product recovery to maintain their competitiveness worldwide. This essential requirement was considered when designing the core elements of MSR™ technology.
The MSR™ MicroSphere Refiner's product recovery process is unique since it is automated and eliminates the need for operators to manually offload products through an aseptic isolator, for example. It helps maximize product yield by minimizing the number of transfers and connections.
Production Agility, Delivered
The MSR™ MicroSpehere Refiner is suited to many product applications. It is designed to enable companies to maintain their agility and quickly adjust to shifting production needs.
Source: Powder Systems
Filtration Agility |
Drying Agility |
Cleaning Agility |
One modular vessel design |
Positive temperature drying |
GMP design / no product traps |
Quick filtration media change-over |
Freeze-drying |
CIP spray-ring option |
Multi-zone filtration |
Multi-zone drying |
Suitable for potent product processing |
Process, PAT-Verified
The US FDA promotes using Process Analytical Technology (PAT) in the pharmaceutical sector to ensure improved product quality control and a faster time to market.
Drug makers have welcomed the PAT approach because MSR™ technology enables them to monitor their microsphere product quality and integrity in real-time during several production phases, including filtration and drying processes (including lyophilization).
The trial-and-error approach is reduced with the inclusion of PAT. This helps shorten the time it takes for pharmaceutical companies to develop drugs for microspheres, typically more complex than conventional drugs, and helps them progress toward right-first-time manufacturing.
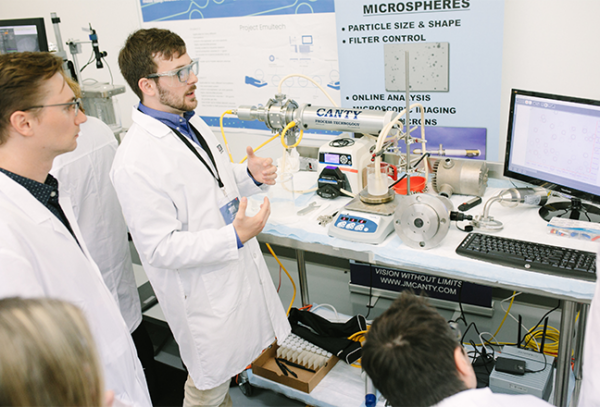
Image Credit: Powder Systems
Successful Scale-up
For most drug producers, large or small, developing sophisticated drug formulations such as microsphere delivery systems has always been difficult. It is essential to ensure that the process technology selected for the R&D stage can be fully scaled to bigger production batches.
Drug makers may have to pay millions if they discover too late that a microsphere method is not scalable.
The MSR™ scale-up approach was created to make developing microsphere pharmaceuticals more straightforward, starting from the preliminary R&D stages and moving through GLP batches, clinical trials, and finally commercial production.
The solutions can guarantee that important production factors like filtration time, washing time, drying time, etc., as well as important process objectives like product yield, product quality and integrity, batch uniformity, etc., can be maintained at each scale.
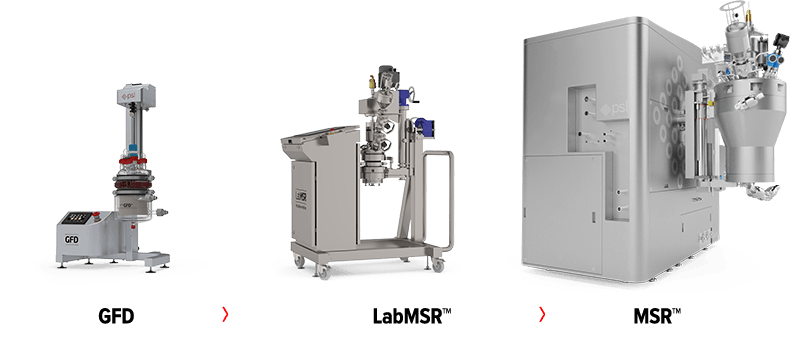
Image Credit: Powder Systems
Download the Brochure for More Information
Technical Overview
Vessel Sizes
Source: Powder Systems
|
0.05 Model |
0.125 Model |
Typical Product Cake Volume (process-dependent) |
1.25 – 9 L |
3 – 22 L |
Maximum Liquid Volume |
98 L |
123 L |
Equipment Dimensions (L x W x H) |
2720 x 2850 x 2760 mm |
Upgrade Options
Source: Powder Systems
|
Standard MSR™ |
Upgrade Options |
Filtration Method |
Suitable for Single Pass |
Loop De-watering |
Drying Method |
Suitable for Vacuum Drying and Freeze-Drying |