Amada Miyachi America, Inc., a leading manufacturer of resistance welding, laser welding, marking, cutting, and micro machining equipment and systems, announces it offers complete local product and sales support for the DC1013-T and DC613-T Series of linear DC resistance spot welding power supplies, manufactured by our sister company MacGregor™.
Typically used in aerospace, medical, and electronic assembly applications, DC1013-T and DC613-T units are ideal for butt welding fuses, welding components to leadframes, gold ribbon bonding, and welding fine wire to pads. High speed automation and communication ports offer users full remote control capability.
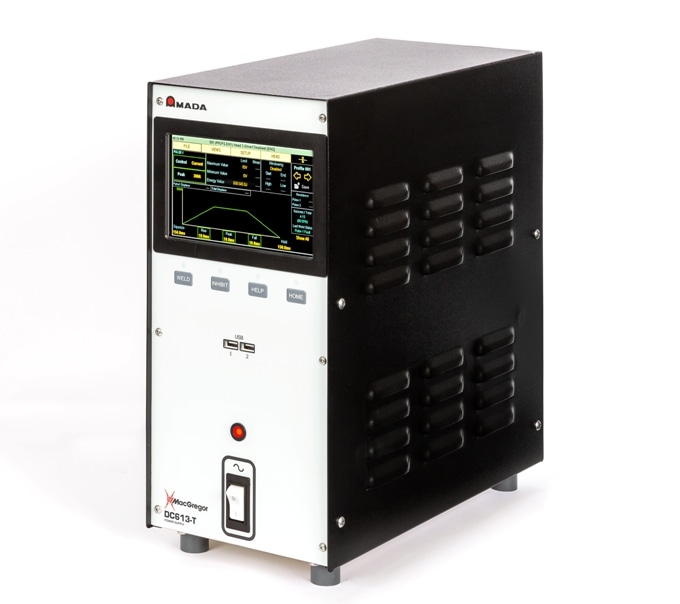
The DC1013-T and DC613-T Series incorporate statistical process control (SPC) data collection and reporting capability via Ethernet. The high performance 1000 ampere (A) precision linear DC spot welding power supplies combine touch panel integrated database process control and monitoring with a high accuracy, zero ripple linear transistor output stage that delivers ultra-fast 10 micron per second (µs) dynamic process response rates, with absolute closed loop 1 A incremental accuracy and repeatability.
Offering high speed, ultra-low ripple closed-loop output control, the DC1013-T and DC613-T Series provide consistent welding process definition and control. Operators can select constant current, voltage, and power modes with programmable multi-pulse combinations in 1 A steps up to 1000 A. Programmable part and weld checking is coupled with optional displacement and force limit checking. The DC1013-T offers three phase operational variants, while the DC613-T supports single phase operations.
Operators have access to full TCP/IP Ethernet interfacing to internal and external SPC database systems. They can easily view both PDF and text format work instructions and process manuals with weld schedules and can view image files with weld schedules for quality control and process checking. Other useful features include 3 USB ports for use with a memory stick, mouse, keyboard, or servo head drives; and SMART weld head force control within weld schedules.