Heraeus‘ SOL9610 Series of front-side metallization pastes are designed to help cell manufacturers enhance the performance and efficiency of crystalline silicon solar cells.
Specifically formulated to print with finger openings between 35um and 55um wide, to provide finer line resolution than previous generations of paste. With further improvements in contact to silicon wafers, test results have shown cell efficiencies greater than 19.5% on standard p-type cells. The pastes feature high cell efficiency while using less paste per cell with the new SOL9610 Series. The adhesion reliability is also high once the cells are integrated into modules.
The SOL9610 series pastes are being used by top manufacturers in their mass production lines. The SOL9610 Series represents one of Heraeus’ highest performing front-side pastes for conventional c-Si solar cells. With latest advancements in research and development, the SOL9610 Series represents the launching pad for new products Heraeus will deliver to the market that will increase customers performance at a lower cost per watt.
New Generation of Higher Efficiency Front-side Pastes
SOL9610 Series metallization materials were formulated to meet the needs of high efficiency emitter structures. Building on the technology of the SOL9600 materials, our newest pastes demonstrate further improvements in contact quality and fine line print capabilities. These translate to higher efficiencies and further reductions in paste consumption.
The SOL9610 series are front-side Ag conductor pastes for fine line screen printing applications on mono and multicrystalline silicon solar cell wafers. They effectively etch SiNx:H and/or SiOx passivation layers during the co-firing process and provide low contact resistance. The benefit of SOL9610 is maximized at finger line openings of 35-55 µm, offering improved transfer and line definition.
SOL9610’s high manufacturability lowers cell’s cost per watt by providing higher throughput and cosmetic yield. Also, the high performance binability provides cell manufacturers with a very tight and high cell output power/efficiency distribution, increasing the value of their production.
Key Benefits
The benefits of front-side metallization pastes are:
- Low series and contact resistance
- High cell efficiency
- Fine line resolution
- Low paste consumption per cell
- Excellent manufacturability includes high cosmetic yield, high throughput speed, outstanding printability, wide processing window and high performance binability
Typical Properties
Viscosity
HBT Cone and Plate Viscometer (Brookfield)
- 120 – 250kcps
- CPE-51 spindle, @ 1 RPM, 25°C
Cone and Plate Viscometer (Haake)
- 12 - 20 Pas;
- Plate/cone (O = 20mm, angle = 0.5°)@ 100s-1; 25 °C
Solids
90.5 ± 1%
Solderability
- Sn62, SAC305
- Use with low solids, no clean flux
Further Contact Resistance Improvement
The novel Heraeus SOL9610 Series is far better than the performance of Heraeus SOL9600 Series with additional improvement in contact resistance providing higher conversion efficiencies. Figure 1 shows a 33% reduction in contact resistance with respect to the company’s previous generation of paste. This improvement in contact resistance has demonstrated an average of 0.17% absolute efficiency improvement at beta customer sites.

Figure 1. Trials at customers’ sites have demonstrated a 33% reduction in contact resistance and an average efficiency improvement of 0.17% absolute using the SOL9610 Series
It is a known fact that a low surface concentration of dopants in Si wafers typically results in poor contact formation between the paste and wafer after firing. Heraeus scientists continue to make advancements in the company’s paste development to overcome technical challenges that improve cell performance. SOL9610 is especially designed for high ohmic emitters with low surface concentration. By changing the paste chemistry, Heraeus is capable of growing much higher density of silver crystallites, especially on lowly doped surfaces, which significantly improve contact properties as shown in Figure 2.
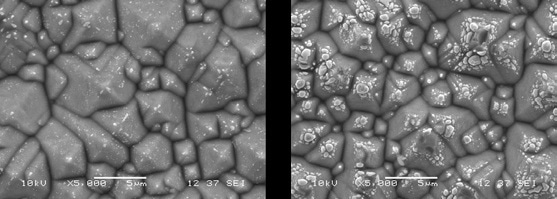
Figure 2. Crystal formation on a high ohmic emitter with old generation paste (left) and current generation paste (right)
Recommended Processing Guidelines
Printing guidelines are provided in Table 1
Table 1. Printing guidelines
Design Finger Line Opening |
Screen Parameter Recommendations |
35 - 55µm |
290 mesh, 20µm stainless steel wire
360 mesh, 16µm stainless steel wire
400 mesh, 18µm stainless steel wire
Note: 15µm EOM typical |
Squeegee |
70 - 75 Shore |
Squeegee Speed |
≥ 180mm/sec |
Squeegee Pressure |
60 – 90N |
Flood Speed |
≥ 300mm/sec |
It is typically dried in an IR dryer with set points of 250-300°C in less than 20 seconds or 150°C for 10 minutes in circulated air oven.
The firing profile is shown in Figure 3.
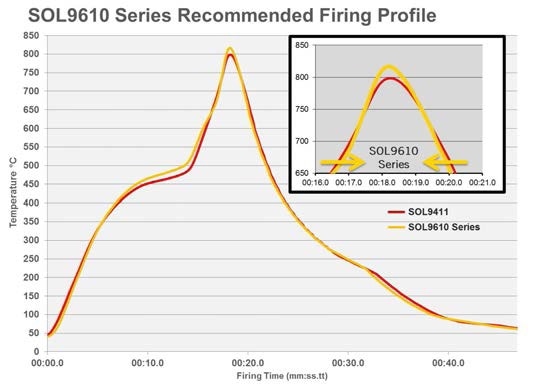
Figure 3. The above firing profile is a standardized recommendation for a profile optimized to the client requirement
Thickness (fired) - 15 - 25µm
Storage - Store in a dry location at 5°C – 25°C.
About Heraeus Photovoltaics
The Heraeus Photovoltaics Business Unit is an industry leading developer and manufacturer of metallization pastes for the photovoltaic industry.
Heraeus has been a manufacturer of thick film pastes for over 40 years. Since 2008, we have been an innovative supplier to the photovoltaics industry, working with c-Si cell manufacturers to improve their cells’ efficiency for both conventional and advanced cell designs.
Heraeus have developed silver metallization pastes that have been integrated into commercially available technologies such as MWT, Double Print, Dual Printing, Selective Emitter, Back Side Passivation and N-Type Cells.
Heraeus have also expanded our capabilities and developed lower temperature processing pastes for Thin Film and other c-Si technologies.
Heraeus' goal is to improve our customers’ cell efficiency and reduce their cell’s cost per watt through our innovative paste design technology.
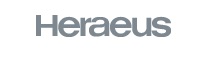
This information has been sourced, reviewed and adapted from materials provided by Heraeus Photovoltaics.
For more information on this source, please visit Heraeus Photovoltaics.