SOL230H is a proven paste for back-side metallization of conventional solar cells and is also ideal as back-side metalization paste for cells with passivated surfaces, where it shows good adhesion properties.
The paste is both lead and cadmium free and suitable for mono and multicrystalline solar cell wafers. SOL230H is a robust paste that can be processed on untextured or textured wafers and allows the use of lead or lead-free solder ribbons. Benchmark testing against a commonly used tabbing silver paste showed several advantages for SOL230H using a range of conditions. The benefits include greatly improved adhesion and reduced paste consumption. This series of paste is also available in other versions based on customer’s process requirements.
Key Benefits
The key benefits of the SOL230H are:
- Wide processing window
- Excellent solderability, adhesion and conductivity
- Pb free solders on both textured and untextured wafers
- Significantly reduced lay downs
- Excellent coverage and easy printability
- Co-fireable with back Al and front Ag pastes
- Pb and Cd free
Adhesion and Solderability
High adhesion shows a good quality solder joint. The impact of humidity or contaminants on the integrity of the solder joint is minimized giving reliable thermal cycling and lifetime testing results. Adhesion testing with a GP-Stab tester with Sn62Pb36Ag2 solder @ 270°C with Kester 961-E flux was used to measure the peak adhesion strength between solder ribbon (ECu 2mm x 150µm) and back contact metallization (1.5 – 2cm section). Initial force measurement showed with a 6.0µm fired film thickness an average value of 6.2N and with a 7.5µm fired film thickness an average of 8.2 N with SOL230H. This is shown in Figure 1.
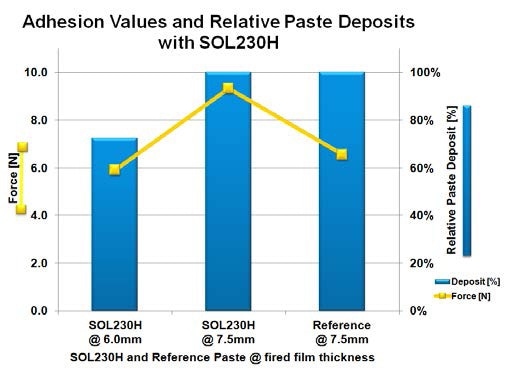
Figure 1. Adhesion values and relative paste deposits with SOL230H
Coverage and Cost Savings
Increased paste coverage with superior results provides a high quality, cost effective solution to any solar cell manufacturer. With rising costs of precious metals, SOL230H can provide savings with improved performance. Coverage with SOL230H provides 95 cm2/gm, which is significantly better than competitor materials. Increased paste coverage translates into lower paste consumption.
Leach Resistance
Testings of leach resistance of SOL230H with Sn63Pb37 solder @ 260°C, (5s-DipFlux: Kester 961-E) demonstrates excellent results. This is shown in Figure 2.
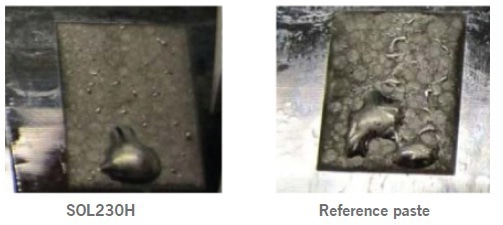
Figure 2. Busbar pads after testing of leach resistance
Recommended Processing Guidelines
Recommended processing guidelines are given below:
- Printing: Screen Parameter Recommendations
200-230 mesh stainless steel screen
10 – 15µm emulsion
- Printing Speed: 100 – 250mm/s 1.0 bar
- Drying: Typically dried in an IR dryer with a set point of 250 – 300°C in less than 20seconds.
- Firing: IR furnace with actual wafer
- Peak Temperature at 725 – 825°C
- Thickness: 7 – 10µm (fired)
- Storage: Store in a dry location at 5°C – 25°C
About Heraeus Photovoltaics
The Heraeus Photovoltaics Business Unit is an industry leading developer and manufacturer of metallization pastes for the photovoltaic industry.
Heraeus has been a manufacturer of thick film pastes for over 40 years. Since 2008, we have been an innovative supplier to the photovoltaics industry, working with c-Si cell manufacturers to improve their cells’ efficiency for both conventional and advanced cell designs.
Heraeus have developed silver metallization pastes that have been integrated into commercially available technologies such as MWT, Double Print, Dual Printing, Selective Emitter, Back Side Passivation and N-Type Cells.
Heraeus have also expanded our capabilities and developed lower temperature processing pastes for Thin Film and other c-Si technologies.
Heraeus' goal is to improve our customers’ cell efficiency and reduce their cell’s cost per watt through our innovative paste design technology.
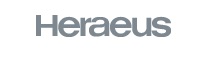
This information has been sourced, reviewed and adapted from materials provided by Heraeus Photovoltaics.
For more information on this source, please visit Heraeus Photovoltaics.