Environmental and safety standards are driving factors in the automotive industry, which also has a continual focus on lowering production costs and increasing efficiency and longevity in support of extended warranties.
Better fuel economy, more comfortable driving experiences, and less frequent maintenance with no drop in performance, are the demands from consumers.
Requirement for High Performance Material Solutions
The requirement for vehicle weight reduction, driven by the desire for improved mileage and lower CO2 emissions, is leading to component miniaturization and functional integration, in the automotive industry. As a result, OEMs are seeking novel materials that offer lower weight and high specific strength to develop cost-effective component solutions with improved efficiency and performance.
Increasing demand for highly reliable smaller components fabricated from lighter materials that exhibit superior strength, outstanding flow properties, and withstand a higher temperature range can be satisfied by fabricating thinner-walled components from high performance thermoplastics. Furthermore, consolidating intricate metal components into a single injection-molded thermoplastic component can minimize overall costs.
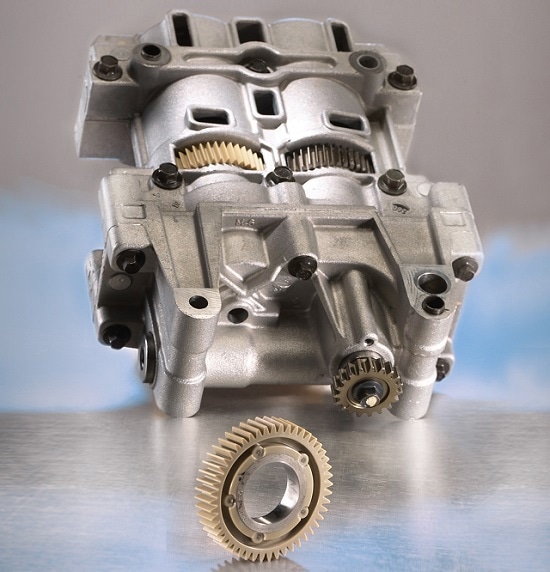
Image 1. Balance Shaft Gear
Today’s industry standards also demand materials capable of performing at ≥150°C based on the application, compared to the temperature range requirements of 100-120°C of years ago. For instance, OEMs are seeking materials capable of performing up to 180°C in the lower areas of steering columns and up to 220°C in turbocharger parts. Considering these requirements in addition to other drivers in the automotive industry, metals or conventional plastics may not provide the feasible solution for applications in such adverse conditions, where even light alloys exhibit a drop in mechanical strength at temperatures of around 200°C.
High Performance Polymers from Victrex
Victrex Polymer Solutions, a unit of Victrex plc, produces polyaryletherketones (PAEK), including VICTREX PEEK polymers, which are high performance thermoplastics demonstrating consistent mechanical properties up to 250°C.
According to a recent study, VICTREX PEEK polymers are able to retain their original stiffness, impact and tensile strength after 5000 hours of use. Under these conditions, traditional materials such as nylon 4.6 and heat-stabilized polyamide experienced property losses up to 50%. With a glass transition temperature range of 143-162°C and melting temperature range of 343-387°C, Victrex thermoplastic polymers can deliver superior performance in the most aggressive environments. The following are the benefits and properties offered by Victrex PEEK-based polymers:
-
Reduced system weight and improved efficiency
-
Design flexibility
-
Withstands high operating temperatures
-
Longevity - extended component life
-
Lubricant free operation
-
Lower noise
-
Reduced maintenance leading to more uptime and lower costs
- Ability to match thermal expansion of metals
- Low specific gravity and ease of processing
- Superior combination of high fatigue strength and ductility
- High mechanical properties across a wide range of temperatures
- Excellent chemical resistance against automotive fluids
- High resistance to wear and Low coefficient of friction
- Good resistance to ageing and moisture absorption
Conclusion
VICTREX PEEK polymers provide up to 80% in weight savings compared to metals. They are frequently used in powertrain components such as seal rings, thrust washers, bushings, bearings, shift fork wear pads, and gears. These weight savings, paired with a low coefficient of friction and low wear rate, and excellent corrosion resistance can improve the overall efficiency of the transmission.
The reduced stress on components and lower friction leads to greater fuel economy, lower maintenance costs, and can increase the lifetime of the powertrain components.
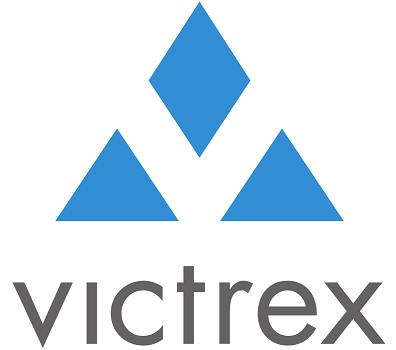
This information has been sourced, reviewed and adapted from materials provided by Victrex.
For more information, please download the full pdf brochure from Victrex.