The government-mandated CAFE standards for the automotive industry will reduce the global carbon footprint and conserve natural resources, according to recent studies. Once the standards reach full effect, consumers could save $8,000 on average over the life span of the vehicle. Hence, automakers are showing more interest in developing innovative solutions that reduce emissions with improved fuel economy.
One of the potential solutions is designing compact, high-power output engines coupled with high efficiency transmissions. The materials specified in the key components of these engines and transmissions need to withstand extremely aggressive, high temperature conditions. Lightweight VICTREX PEEK polymers have a proven track record of over three decades of success in substituting metals and other polymers in the most challenging environments.
VICTREX PEEK Polymers
The rising demands of compact, high-power output engines can also result in high levels of noise, vibration and harshness (NVH). The use of VICTREX PEEK polymers in designing components can overcome these factors. This has been proved in a case study conducted by Metaldyne, a key player designing and supplying powertrain components and assemblies.
According to the case study, the use of VICTREX PEEK as an alternative solution to metals in a balance shaft module reduced NVH by 3dB, i.e., a 50% noise level reduction. Besides reducing NVH, the company was able to reduce the system inertia by 30% and the power consumption by up to 9% owing to the lightweight nature of the polymer. Thrust washers made from VICTREX PEEK polymer is shown in Figure 1.
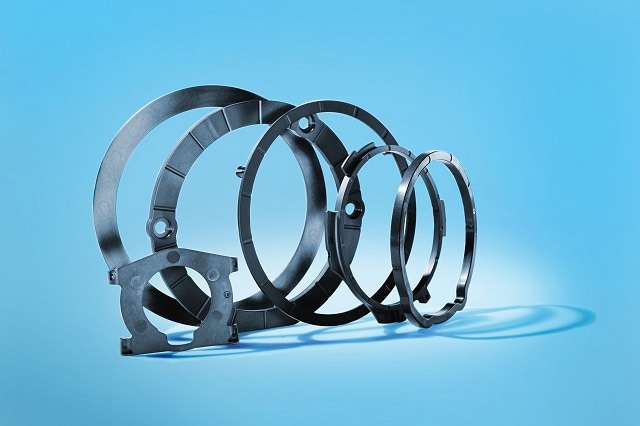
Figure 1. Thrust washers made from VICTREX PEEK polymer
Advantages of VICTREX PEEK in Engine and Transmission Applications
VICTREX PEEK polymers provide up to 80% weight reduction in powertrain components, including gears, shift fork wear pads, bearings, bushings, thrust washers, and seal rings, when compared to metals. Together with weight reduction, the unique combination of low wear rate, a low coefficient of friction, and superior corrosion resistance properties of the material can enhance the overall efficiency of the transmission. The low friction and minimal stress on components result in better fuel economy, lower maintenance costs, and eventually extended service life of the powertrain.
Dimensional stability at temperatures more than 200°C, the ability to handle temporary lubrication loss, and superior corrosion resistance to automotive fluids are other benefits of high performance VICTREX PEEK thermoplastics, all of these qualities can increase the lifetime of components especially as manufacturers are promising extended warranties to gain a competitive advantage.
Victrex proactively tackles the demands of the automotive market with its latest VICTREX WG polymers to meet the requirement for improved wear resistance and minimal frictional losses in crucial automotive components. These wear grades exhibit reduced wear rate and a lower coefficient of friction when compared to other polymers, including polyamide-imide and polyimide. These qualities improve reliability and energy efficiency.
Standard injection molding machines can be used to process VICTREX WG polymers, thus minimizing part-to-part variability and processing costs when compared to other polymers. Parts consolidation and other design improvements are also possible with VICTREX PEEK, thereby considerably shortening the assembly time and reducing the overall system cost.
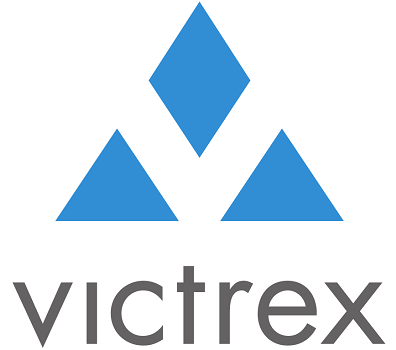
This information has been sourced, reviewed and adapted from materials provided by Victrex.
For more information please download the full brochure from Victrex.