Nov 10 2001
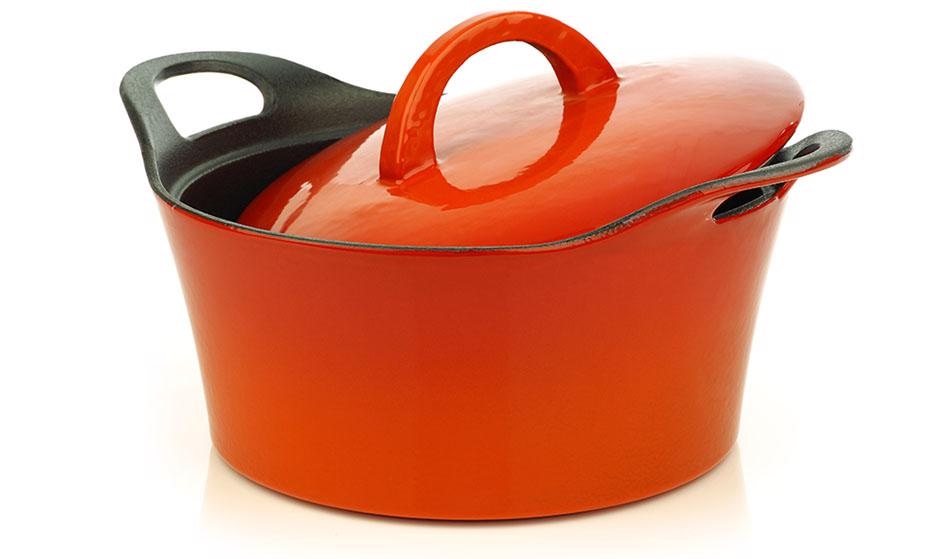
Peter Zijlstra / Shutterstock
Vitreous enamels are quite similar to ceramic glazes in several aspects. After being applied, they are fired to form an almost glassy layer. They are commonly used in the manufacture of household items, specifically those that are exposed to high heat and harsh environments, for example, enameled “white goods” like cookers and enameled cookware.
The difference lies in the fact that enamels are coated on metal items instead of ceramic. As such, enamels satisfy the unique constraints set by these materials, such as low firing temperatures and high thermal expansion.
Composition of Enamels
Although many oxides are common with glaze composition, enamels are essentially richer in fluxing (modifiers) oxides, and the materials are highly fritted.
There are a number of glass-forming systems, but enamels are almost solely based on alumino-silicate glass systems. Silica (SiO2)—the main glass-forming oxide—is modified by adding various different oxides. The function of the modifiers is to change the chemical, physical, and thermal properties (see Table 1).
Table 1
Glass Formers |
Intermediates |
Modifiers (melters) |
SiO2 |
Al2O3
ZrO2
TiO2 |
CaO
BaO
SrO
ZnO
PbO
Na2O
K2O
Li2O
Bi2O3
B2O3 |
The frit content of enamel batches is high owing to the need for low-temperature melting. Additives are added to the frit content to alter the color and fluid properties, as well as to optimize the application.
Key Properties
The properties of enamels are not fixed and tend to vary. This is because their composition and use are so varied. Enamels could be applied purely for aesthetic reasons, functional purposes, or for both. Based on the application and product/process types, the following properties are regarded to be highly significant.
Thermal Expansion
In general, enamels are required to be under compression in the fired state to prevent crazing. The composition of the fired enamel on the metal controls the expansion.
Color
The available colors for enamels depend on the chemical composition of the enamel, the firing temperature, as well as the composition of the selected color additive.
Durability
Physical and chemical durability may be of significance, based on the application. Different types of tests are performed to evaluate the durability for use in different types of products.
Maturing Range
It is essential for the enamels to mature within a suitable time interval and temperature range. In addition, maturity should be reached over an ideal range to allow the incorporation of process variables.
Enamels are applied by spraying and dipping, or through electrostatic or dry dusting techniques. In certain cases, enamels are applied in single layers. On some metals, they are applied in two layers—a base coat and a top coat—to achieve appropriate finishes and to enhance adhesion. Moreover, in some cases, pretreatments of the metal, like “pickling” in acid baths to eliminate grease, and pre-oxidation to form an oxide bonding layer may be necessary.
In general, enamels are fired between 700 °C and 1000 °C based on the substrate metal, the composition of the enamel, and the length of heating time.
Applications
As stated above, enamels are generally coated on metal substrates that are often exposed to corrosive environments and/or high temperatures. Listed below are some of the applications of enamels: