The accuracy and quality of results depends considerably on the cuts made to prepare a sample for tensile testing. It is very important to prepare a sample without nicks or jagged edges for accurate tensile results.
Those imperfections may impact the ability to offer reliable tensile results for the physical properties of the specimen. The tensile test results also depend on how a sample is handled and the smaple must also be handled with care once cut.
Example of Sample Preparation
The importance of sample preparation can be understood by using an example test ASTM D882 for tensile properties of thin plastic sheeting. This test method covers determining tensile properties of plastics in the form of thin sheeting, including film (less than 1.0mm (1,000microns) in thickness).
Specimens are arranged in the universal tester and pulled till failure. For ASTM D882, the grip separation and test speed are based on the elongation needed to break the material. Elongation and tensile moduli can be calculated from crosshead displacement.
Specimen Size: Uniform width, thickness, and 2 inches longer than the gage-length
Sample Width: It shall not be less than 5mm, or greater than 25.4mm (selection of common width : 15mm or 25mm or 25.4mm)
A lot of care must be exercised in cutting specimens to prevent nicks and tears that are likely to cause premature failures. The edges should be parallel to within 5% of the width over the length of the specimen between the grips.
One may use microscopical examination of the specimens to detect flaws because of specimen or sample preparation.
Two preparation tools were studied for demonstrating the importance of the sample cut - the JDC Precision Sample Cutter and the MTT 1” Strip Cutter.
Using a black plastic film, Figures 1 and 2 show a 200 time magnification of the cuts made:
.jpg)
Figure 1. JDC Precision Sample Cutter
.jpg)
Figure 2. MTT 1” Strip Cutter
.jpg)
Figure 3. Sample cuts magnified 200 times
It is understood while reviewing these images that the MTT handheld strip cutter results in a rough cut while the JDC precision cutter creates a smooth precise sample edge.
The implications of the choice to go with the less expensive cutter can impact tensile results and increase production cost by reflecting the need to make a product stronger than necessary based on the tensile strength results.
Tensile Test Results for JDC Precision Sample Cutter VS MTT 1" Strip Cutter
The results are shown in Figure 4.
.png)
.png)
Figure 4. Tensile test results
The results clearly show the quality of cut makes a large difference in the results.
About Thwing-Albert Instrument Company
Thwing-Albert Instrument Company is one of the nation's leading manufacturers of advanced testing instrumentation. For more than a century, Thwing-Albert has provided proven testing equipment and has earned a reputation as a foremost authority on physical testing standards.
The core business of Thwing-Albert focuses on tensile testing applications across a wide range of industries including adhesives, paper, plastics, packaging, textiles, and others. Research laboratories and quality control departments worldwide confidently rely on Thwing-Albert's affordable precision instruments to develop and produce high quality products.
Thwing-Albert is headquartered in West Berlin, NJ, and has Sales Offices worldwide.
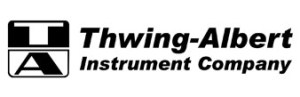
This information has been sourced, reviewed and adapted from materials provided by Thwing-Albert Instrument Company.
For more information on this source, please visit Thwing-Albert Instrument Company.