A customer contacted Alicat Scientific to create a mass flow controller featuring the key characteristics of a ‘Double Block and Bleed’ valve system coupled with flow and/or pressure control.
‘Double Block and Bleed’ valves are generally used to isolate process systems or instruments from their gas sources.
Development Process
During the development process, a test unit was built by placing the exhaust and feed valves of a dual valve pressure controller at the inlet to a mass flow meter. The firmware control parameters were set to control absolute pressure at the outlet of the flow meter in order to achieve absolute pressure control. This control mode would enable addition of gas to the process volume or venting of gas from the process volume automatically as required to keep the pressure level to the set-point.
The mass flow meter displayed all of the standard parameters, including temperature, absolute pressure, mass flow rate, and volumetric flow rate. This resulted in an improvement in utility to the customer by accurately revealing the amount of gas involved in keeping the pressure level to the set-point.
By switching the controlled variable from absolute pressure to mass flow rate, the flow meter showed accurate mass flow rate control.
Next, the set-point input was set to a mode to accept bidirectional commands, enabling command of both positive and negative set-points. Positive flow would be the flow going to the process from the controller, while negative flow would be the flow going to the controller from the process. This mode also worked perfectly, without software modifications.
Prototype Development and Production Line Product Testing
These initial tests led to the designing of a closely integrated mechanical configuration, and then to the fabrication of a prototype.
Alicat Scientific has delivered both small flow and large flow configurations to clients for production line product testing. Some of the examples are discussed here.
Testing the Flow vs. Pressure Characteristics of Respiratory Assist Equipment
This application involved the generation of both positive and negative flows with recording of pressure rises or drops. Readings of different pressure and flow values were recorded when the flow meter switched between modes.
Flow and Leak Testing of a Multi-Port Industrial Valve Product
This application involved the application of pressures at a number of ports with recording of the flow rates. When the flow meter was changed from one mode to another, flows stopped along one path and began along another path.
The flows at all of the ports were monitored to characterize internal and external leakage paths as well as the flow path blockages.
Application in Remote Environmental Monitoring Station
A remote environmental monitoring station required to check its accuracy periodically. Usually, separate mass flow controllers would be employed to:
- Direct flow towards the infrared analyzer from the sample stack to determine a variety of pollutants.
- Direct a controlled amount of a calibration gas via the analyzer to validate proper operation.
Moreover, the station required additional valves and/or manual operator intervention. As opposed to the usual configuration, the connection of an Alicat MCD enabled the inlet valve to be fed by the calibration gas, while outlet valve is connected to a vacuum pump. This, in turn, allowed the process connection to be routed to the analyzer.
For most of the time, the flow meter is programmed for a 5 LPM volumetric flow rate in the negative direction, directing a constant volumetric flow rate to be passed through the analyzer from the sample stack. During the calibration cycle, the controller is set to deliver a positive 100 CCM flow from the calibration gas cylinder to the analyzer, eventually venting out of the sample stack. This cycle may be carried out under local computer control without additional control valves.
Testing a Pressure Relief Valve
This application involved the use of the Alicat MCD to easily ramp the pressure monitored by a pressure relief valve. This is performed by commanding a fixed mass flow rate and monitoring the absolute pressure.
The pressure stops increasing during the opening of the relief valve. Now, the instrument is commanded to stop flowing and the new reading of the pressure level is recorded.
By commanding a negative flow for a short time, the pressure is reduced to subsequently perform a re-test of the cracking pressure.
Applications of Alicat MCD Series Devices
Alicat MCD series devices have found use in:
- Mass flow control from a pressurized source to a vacuum process.
- Mass flow control from a pressurized source to a process at or above atmospheric pressure.
- Absolute pressure control of a closed volume, demanding smooth ramping of pressures, up and down, through bi-directional mass flow control.
- Absolute pressure control of a flowing process.
- Volumetric (uncorrected) flow control into and out-of processes without the requirement to change connection configurations or programming.
- Absolute back-pressure control of a flowing process.
MCD series controllers have all of the standard Alicat features, including multi-drop RS-232 serial communications and gas selection.
Conclusion
The MCD series is highly flexible, making it to be employed as a ‘Universal Control Element’. The use of Alicat MCD controllers enables researchers to rapidly and conveniently assemble proof of concept analyses within minutes or hours rather than weeks or months.
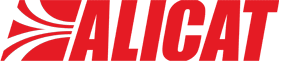
This information has been sourced, reviewed and adapted from materials provided by Alicat Scientific.
For more information on this source, please visit Alicat Scientific.