One method for an ICL unit can be based on the physics of the Poiseuille Equation. The method involves creating an internal restriction known as a Laminar Flow Element (LFE), which drives the gas molecules to travel in parallel paths across the length of the passage, virtually eliminating turbulent flow. The differential pressure drop is then measured within the laminar realm.
The Poiseuille Equation
The relationship between the flow and pressure drop is quantified by the Poiseuille Equation as follows:
Q = (P1 – P2)π r4 / 8ηL,
where, Q = Volumetric Flow Rate; P1 = Static pressure at the inlet; P2 = Static pressure at the outlet; r = Hydraulic Radius of the restriction; η = (eta) absolute viscosity of the fluid; and L = Length of the restriction.
Since π, r and L are constants, the equation can be expressed as follows:
Q = K(Δ P/η),
where, K is a constant factor identified by the geometry of the restriction. It describes the linear relationship between volumetric flow rate (Q), differential pressure (ΔP), and absolute viscosity (η) as a simple equation.
Theory of Operation for an ICL Unit
The absolute viscosity of a gas is affected by changes in gas temperature. Hence, the temperature needs to be measured to identify the value of η. For most DP devices, this can be performed by manually referencing charts that provide the viscosity properties of the gas at specific temperatures.
This reference is done internally by a microprocessor and a discrete temperature sensor in an ICL device. The volumetric flow rate has only been identified at this point.
For an ICL device, the range of shortcomings of thermal devices can be addressed by taking additional measurements to identify the actual mass flow rate of the gas. The volume flow is related to the mass flow as follows:
Mass = Volume * Density Correction Factor.
According to ideal gas laws, the absolute pressure and temperature of a gas affect its density. The following equation describes the effect of temperature on density:
ρa / ρs = Ts / Ta
where, ρa = Density at Flow Condition; Ta = Absolute Temperature at Flow Condition in Kelvin; ρ s = Density at Standard Condition; Ts = Absolute Temperature at Standard Condition in Kelvin.
The effect of absolute pressure on density is as follows:
ρa / ρs = Pa / Ps
where, ρa = Density at Flow Condition; Pa = Flow Absolute Pressure; ρs = Density at Standard Condition; and Ps = Absolute Pressure at Standard Condition.
To determine the mass flow rate (M), the aforementioned equations necessitate the application of two correction factors to volumetric flow rate: absolute pressure effect on density and temperature effect on density. Hence, the equation can be expressed as:
M = Q(Ts / Ta)( Pa / Ps).
An ICL flowmeter contains a discrete absolute pressure sensor at the laminar region of the flow stream to acquire information to be sent to the microprocessor. This information along with the data acquired by the discrete absolute temperature sensor is used to appropriately calculate mass flow rate.
These calculations can be performed using the reference to some standard temperature and pressure (STP) as indicated by variables Ts and Ps.
Conclusion
The units for mass are described in grams, kilograms, etc., while the mass flow rate is specified in standard cubic feet per hour (SCFH), standard cubic centimeters per minute (SCCM), or standard liters per minute (SLPM).
By determining the STP calibration of the device and the density of a specific gas at that STP, the flow rate can be determined in grams per minute, kilograms per hour, etc.
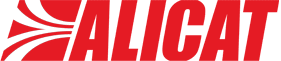
This information has been sourced, reviewed and adapted from materials provided by Alicat Scientific.
For more information on this source, please visit Alicat Scientific.