ROHACELL HERO is an innovative composite foam structure that are lightweight, cost-effectively producible, and durable over their service life, providing the latest in materials technology for aircraft structures. It sets the new benchmark in aircraft structural core material.
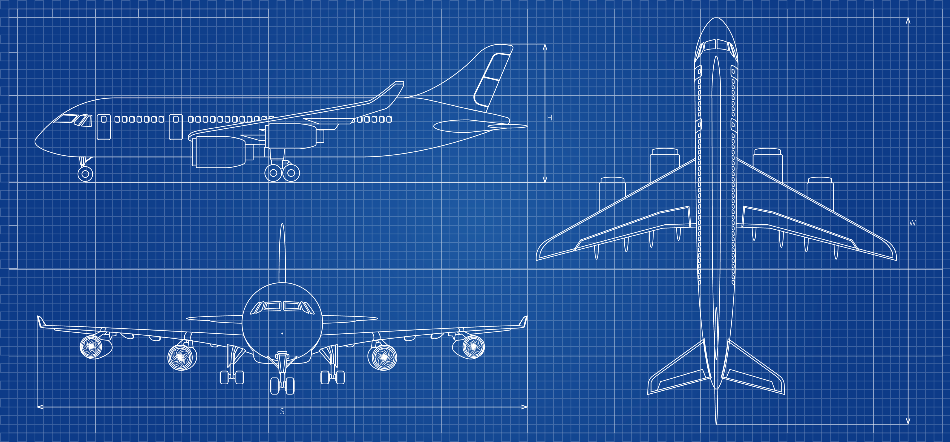
Image Credit: Shutterstock/MicroOne
Key Properties of ROHACELL HERO
The following table lists the key properties of ROHACELL HERO:
Property |
Test method |
Unit |
ROHACELL® |
71 HERO |
110 HERO |
200 HERO |
Density |
ISO 845 |
kg/m3 |
75 |
110 |
205 |
Tensile strength |
ISO 527-2 |
MPa |
4.1 |
6.3 |
12.3 |
Tensile modulus |
ISO 527-2 |
MPa |
123 |
189 |
389 |
Elongation at break |
ISO 527-2 |
% |
9.5 |
9.9 |
10.8 |
Compressive strength |
ISO 844 |
MPa |
1.1 |
2.5 |
7.1 |
Compressive modulus |
ISO 844 |
MPa |
48 |
83 |
180 |
Shear strength |
ASTM C 273 |
MPa |
1.3 |
2.3 |
5.2 |
Shear modulus |
ASTM C 273 |
MPa |
28 |
50 |
109 |
Max. shear strain |
ASTM C 273 |
% |
7.2 |
7.2 |
7.2 |
All ROHACELL products are closed-cell rigid foams based on polymethacrylimide (PMI) chemistry and without CFC's.
Key Features and Benefits of ROHACELL HERO
Sandwich technology is an efficient approach for weight reduction, and ROHACELL HERO sandwich cores provide the most weight reduction potential of all structural foams owing to their low density and superior mechanical properties. ROHACELL HERO is composed of an entirely closed cell structure and reduces added weight by taking up resin only in the cut surface cells. This delivers finished components with lighter weight compared to conventional honeycomb structures.
ROHACELL HERO exhibits outstanding elongation at break properties and remains strong and durable for the service life of the aircraft. It enables easy detection of surface impact damage during inspections and simplifies rework/repair because it does not allow the core damage to extend beyond the initial impact location and as well as water ingress, a major drawback of the honeycomb core structures.
ROHACELL HERO demonstrates heat resistance of up to 220°C, thus allowing for increasing the processing or curing temperatures to a much higher level compared to other core materials, for instance, typical cure cycle at 180°C/0.7MPa is acceptable. This capability considerably shortens total cycle time and increases productivity.
Compared to other core materials, ROHACELL HERO is convenient to be processed in many different processes, including resin infusion, autoclave, RTM and VARTM. Evonik’s Sandwich Technology Center is ready to supply customers with finished, ready-to-use shaped ROHACELL HERO components to be used in their next processing step. Customers can achieve the following benefits:
- Waste elimination
- Reduction in in-house production time
- Up to 30 % cost savings
Conclusion
ROHACELL HERO is a recommended grade to be used as core material in sandwich structures for aircraft components, including ailerons, horizontal and vertical stabilizers, landing gear doors, aircraft wings, and other areas based on surface impact damage.
About Evonik Industries - ROHACELL
For more than 40 years, Evonik's ROHACELL structural foam has been offering the aerospace and automotive industries, medical technology and other markets boundless possibilities for creating high performance composite parts and products.
Considering ROHACELL's excellent mechanical properties over a wide temperature and density range, impressive dynamic strength and fatigue behavior, and a temperature resistance of up to 220C (428F), it is no coincidence that Evonik remains a leader in supplying foam cores sheets and shapes for lightweight sandwich construction worldwide.
.jpg)
This information has been sourced, reviewed and adapted from materials provided by Evonik Industries - ROHACELL.
For more information on this source, please visit Evonik Industries - ROHACELL.