In the semiconductor industry, more sophisticated control of the planarization steps is a key process requirement for higher density chip technology. The use of colloidal dispersion of metal oxide slurries called Chemical-Mechanical Planarization (CMP) affects the planarization or polishing steps. These slurries are predominantly of silica and alumina, with mean diameters in the 10-200nm range.
Laser Diffraction is a commonly used technique in the characterization of the particle size distribution (PSD) of these slurries. It is a known fact that a small volume percentage of particles larger than 1µm are present in these slurries and their presence can cause defects such as scratches on the wafer surfaces. This article demonstrates that Single Particle Optical Sizing (SPOS) is a better tool to quantitatively characterize CMP slurries compared to Laser Diffraction.
Limitations of Laser Diffraction
Laser Diffraction devices gained popularity owing to their fast measurement times and large dynamic ranges. However, they are based on an ensemble technique, requiring a relatively complex and an ‘ill-conditioned’ mathematical algorithm to produce an approximate representation of the PSD.
Laser Diffraction relies on the combination of Fraunhofer Diffraction and Mie Scattering principles. Fraunhofer Diffraction depends upon the pattern of scattered light intensity due to the phenomenon of diffraction. Nonetheless, the spatial pattern of periodic intensity variations caused by the phenomenon of diffraction cannot be observed for particles tinier than roughly 2µm. Instead, the mechanism, which is functioning, is that of light scattering.
Hence, it is necessary to implement a second measurement based on Mie Scattering theory to acquire even moderately reliable size information for particles tinier than this lower Fraunhofer ‘limit,’ which consists of virtually the whole population distribution of typical CMPs. This theory delineates the scattering intensity variations at relatively large angles attributable to the mutual interference of individual light waves scattered from various points within a single particle. This causes an angular dependence in the scattering intensity, which relies on the index of refraction of the particle, the particle diameter and laser wavelength.
Furthermore, the amount of light absorbed by the particles significantly influences the variation of scattering intensity with an angle. This aspect is accounted for by the imaginary part of the (complex) index of refraction of the particles. Therefore, both the real and imaginary components of the index of refraction of the slurry particles need to be provided.
Finally, a light scattering device needs to successfully integrate the results of its Fraunhofer diffraction and Mie Scattering analyses to provide accurate and reliable results for PSDs, which overlap both physical regions and, consequently, theories. Hence, producing the appropriate ‘admixture’ of results from two entirely different physical phenomena is a technically challenging task for devices based on these physical principles.
Laser Diffraction yields a reliable mean particle diameter for CMPs that are stable and ‘good’ polishing slurries. However, this technique is inadequate to characterize unstable ‘bad’ slurries as they contain large fractions of ‘outlier’ particles, often producing unacceptably large artifacts in the computed PSD.
CMP Slurry Monitoring Using the PSS AccuSizer
Capabilities of SPOS Technique
The SPOS technique counts particles, one at a time, based on light obscuration. Hence, it has unprecedented sensitivity and resolution to determine defect-causing particles. As a single particle counter, it is essentially unaffected by the kinds of instabilities and artifacts exhibited by the PSDs acquired by the Laser Diffraction technique.
The SPOS technique can accurately and reproducibly provide quantitative information about the region of the largest slurry particles, which is highly significant to slurry performance. Figure 1a consists of the population distribution acquired by SPOS on two Cerium Oxide type slurries with a manufacturer-specified diameter of 350nm. Slurry 1 was observed to be a well-performing slurry, while Slurry 2 was thought to be unstable as it produced sediment at the bottom of its container.
.jpg)
Figure 1. a. Population Distribution of Cerium Oxide Slurry 1 (circles) and Slurry 2 (triangles); b. Volume-Weighted PSDs for Slurry 1 and Slurry 2.
Figure 1b consists of the Volume-Weighted distributions for these same samples, showing a broader tail for Slurry 2 compared to the tail of the more stable Slurry 1. This indicates the greater tendency of Slurry 2 to sediment.
Figure 2 consists of the Volume-Weighted PSDs acquired by Laser Diffraction on the same two Cerium Oxide slurries. Figure 2a consists of the results estimated with a real index of refraction of 1.65 and an imaginary index of refraction of 0.01i, while the results in Figure 2b were computed with an imaginary index of refraction of 0.10i. Both sets of results were computed from the same scattered light pattern. Although the results revealed that Slurry 2 had more big particles than Slurry 1, they also illustrated the difficulty of obtaining accurate quantitative information from Laser Diffraction.
.jpg)
Figure 2. Volume- Weighted PSDs of Slurries 1 (circles) and 2 (diamonds) obtained by Laser Diffraction. a. index of refraction - = 1.65 + 0.01i, b. index of refraction -1.65 + 0.10i.
The selection of the imaginary index of refraction resulted in a 10% shift in the mean diameter for Slurry 1 and significantly changed the shape of the distribution for Slurry 2. Moreover, the data from Slurry 2 shows that particles larger than 1µm contributed to the majority (>70%) of solids volume. This is impossible and contradicts with the data from a gravimetric analysis as well as that from the SPOS technique that showed the solids percentage from particles larger than 1µm to be below 1% in Slurry 2.
Figure 3 depicts the Volume-Weighted PSDs (ID=1.65 + 0.10i) of Slurry 1 after sonication, suggesting that sonication causes the slurry to aggregate. This is against the expected behavior of sonication to break up weakly bonded aggregates. This data demonstrates the tendency of Laser Diffraction to produce artifacts that do not represent actual particle sizes.
.jpg)
Figure 3. Volume-Weighted PSD of Cerium Oxide Slurry 1 after 20 seconds of sonication obtained from Laser Diffraction.
Figure 4a consists of the Number-Weighted PSD acquired by the SPOS technique on the same sample, showing only one tail and no indication of a second peak at 35µm. The comparison of the percentage solids in the tail for particles larger than 1µm (0.23%) shows no change from the unsonicated sample (0.25%). Figure 4b illustrates the Volume-Weighted SPOS data from Slurry 2 after sonication. It is overlaid with the unsonicated data from Figure 1.
.jpg)
Figure 4. a. Slurry 1 after 20 seconds of sonication; b. Slurry 2 before and after sonication.
Contrary to Laser Diffraction results, the results from the SPOS technique clearly show the effect of the sonication in significantly lowering the volume contribution for particles larger than 2µm and risks of using Laser Diffraction to determine slurry performance.
Figure 5 shows the data obtained from a silica-based CMP. Figure 5a consists of the SPOS tail data (Volume-Weighted) of two silica slurries, starting at 0.5µm. As can be observed, particles in the 2-20µm range made a significant volume contribution in Slurry A, while particles larger than 5µm were not found in Slurry B.
Figure 5b shows the Volume-Weighted PSD (ID=1.08 + 0.10i) produced by Laser Diffraction on slurry A. The PSD for slurry B was identical. As can be observed, it comprises a single, symmetrical peak centered at 0.15µm, but free from particles larger than 1µm. This result shows the ability of Laser Diffraction to provide useful mean-diameter information when the sample has a narrow PSD. This data also illustrates the lack of sensitivity of Laser Diffraction to see differences in these two silica slurries that can be observed with the SPOS technique.
.jpg)
Figure 5. a. Volume-Weighted PSDs for Silica Slurry A and B obtained from SPOS. B. Volume-Weighted PSD for Silica Slurry A obtained from Laser Diffraction.
Conclusion
The results clearly demonstrate the ability of the SPOS technique to provide accurate information about the CMP slurry performance and its superior sensitivity over Laser Diffraction to quantify the large outlier particles, which can cause defects and decrease chip yields.
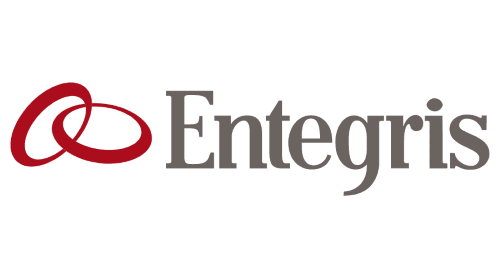
This information has been sourced, reviewed and adapted from materials provided by Entegris
For more information on this source, please visit Entegris