Steel is a strong, versatile and relatively inexpensive material with a great many uses in many different industries. It has, however, one major disadvantage. It is prone to corrosion, even in interior environments. Corrosion prevention is therefore essential if steel structures are to be economical. Today, increased awareness of the long-term savings possible from reduced maintenance costs have highlighted the need for durable protective systems for steel. Metallic zinc coatings are applied to protect steel in several ways: • From a molten metal bath (hot dip galvanizing) • By electrochemical means (zinc plating) • From a spray of molten metal (metallizing) • In the form of zinc powder (mechanical plating). Hot Dip Galvanizing Hot Dip Galvanizing, as a method of corrosion protecting for steel, has grown almost continuously since it was first used over 150 years ago. Its ability to grow in the face of sophisticated competition is the result of the simplicity of the process and the unique advantages of the coating. Galvanizing can only be performed on chemically clean surfaces. Therefore most of the preparation work is done with this objective in mind. The substrate will usually be dipped in a dilute acid solution to remove all traces of surface oxide such as rust and mill scale. After rinsing, the work is then dipped in a flux prior to galvanizing. As the clean iron or steel is immersed in the galvanizing bath, the zinc (at about 450°C) wets the surface and a reaction takes place to form zinc-iron alloy layers. When the work is removed from the bath some molten zinc will remain on top of the alloy layers, and the result is a coating that is metallurgically bonded to the base metal, unlike most protective coatings, resulting in extremely good adhesion of the coating (see fig. 1). The average time of immersion is about three or four minutes but it can be longer. Conditions in the Galvanizing plant such as temperature, humidity and air quality do not affect the quality of the galvanized coating. A schematic galvanizing line is shown in figure 2. 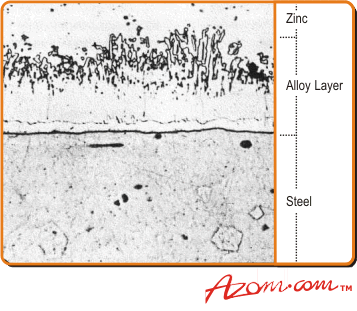 | Figure 1. Microstructure of a typical hot dip galvanised coating. | 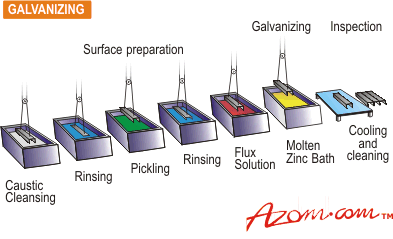 | Figure 2. Diagram of a typical galvanising line. | The coating thickness is normally determined by the underlying steel thickness and the standard average minimum coating, weight to BS 729 is 610 g.m-2 (85 µm) for steel more than 5 mm thick (see Table 1). The outer layer of pure zinc in hot dip galvanizing is relatively soft and absorbs much of the shock of an initial impact during handling. The alloy layers beneath are much harder, sometimes even harder than the base steel itself. This combination provides a tough coating. (See fig.3.). 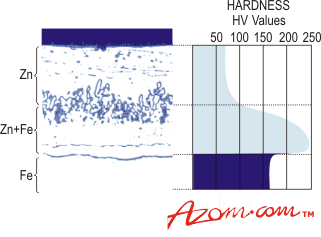 | Figure 3. Microstructure of hot dip galvanised coating showing variations in hardness through the coating. | Centrifuged Galvanized Coatings This involves a process covered in BS 729: 1971 (1986) and is used for galvanizing threaded components and other small parts. The steel parts are prepared as usual, and then dipped in the molten zinc in a perforated basket. After the coating has formed this is centrifuged or spun at high speed, to throw off the surplus zinc to ensure a clean profile. A minimum of 13 microns should be left on all surfaces. Thicker Coatings by Surface Roughening. Grit blasting the steel surface prior to immersion roughens and increases the surface area and, therefore. increases the amount of steel in contract with the molten zinc. This can increase the weight of a zinc coating by up to 50%. Galvanizing Reactive Steels A thicker zinc coating can be obtained if the article to be galvanized is manufactured from a reactive steel. Silicon is frequently added to steel as a deoxidant during its production. The silicon changes the composition of the zinc-iron alloy layers so that they continue to grow with time and the rate of growth does not significantly slow down as the layer becomes thicker. Protection by Sacrificial Action If damage to a protective coating reveals the bare steel, then the resulting effect depends very much on the type of coating. Protective systems usually fall into two major groups: • barrier coatings that give no protection at points of damage (e.g. most paints) • coatings that protect by sacrificial action (e.g. zinc coatings). Zinc corrodes in preference to steel and sacrifices itself to protect the steel, hence hot dip galvanizing is in the second group. The corrosion products from the zinc are deposited on the steel resealing it from the atmosphere and therefore stopping corrosion. Organic Coating of Galvanised Steel Hot dip galvanising by itself is a well established and cost effective means of protecting steel from corrosion. However, the addition of an organic coating such as paint or powder, known as a duplex system, has further advantages: • colours can be used • the extra barrier provided by the organic film extends the life of the galvanizing • the life of the coating is extended by the action of the zinc layers, by preventing corrosion underneath the paint. This synergistic system allows steel to be used in a variety of forms and applications, providing added corrosion protection and enhanced aesthetic appeal. Properties of Galvanized Sheet The degree of post-forming possible on a general galvanized article is limited by the low ductility of the alloy layers. This is of little importance for fabricated parts. However, galvanized sheet often needs to be severely bent or drawn during subsequent fabrication, and for this purpose the coating is modified by adding 0.1-0.2% aluminium to the galvanizing bath which inhibits alloy layer formation and gives a very ductile coating. Some grades of galvanized sheet can be folded flat on themselves without the coating flaking off. Galvanized sheet and sections can be joined by all conventional methods including fusion and resistance welding, though the operating techniques are slightly different from those used for uncoated steel. Specifying Galvanizing Standards The basic specification for hot dip galvanized coatings on iron and steel articles is defined by a single standard, BS 729: 1971 (1986) (European standard under development: pr EN 21461). To ensure the best quality and technical backup service, it is recommended that the work is processed by a member of the Galvanizers Association. Zinc Plating Large tonnages of steel strip and wire are protected by electro-galvanizing, in which the zinc, either pure or alloyed, is electrodeposited from a solution of zinc and other salts in high-speed, high-current density electroplating lines. The coatings are generally more uniform, smoother and thinner than hot-dip coatings. These coatings are becoming increasingly important in automotive applications. Zinc coatings may also be electroplated onto individual formed articles. (See also: BS 1706: 1990 and BS 3382 Parts 3 & 7: 1965.) Metallizing Atomised particles of molten zinc are projected on to a grit-blasted steel surface from a special flame or arc-pistol, fed with wire or powder. The process is often applied to structural components too large to be dipped in a galvanizing bath, and to structures which cannot withstand heating, or which require a thicker coating than can economically be applied by other methods. (See also: BS 2569 Part 1: 1964(1988).) Mechanical Plating Zinc is cold welded on to the steel surface by tumbling the prepared articles with a mixture of zinc dust, glass spheres, a wetting agent and water. Before processing, the steel surface is coated with a thin copper layer by immersion in copper sulphate solution. The treatments are carried out cold, so there is no risk of softening tempered steel springs or case-hardened fasteners. A very even zinc coating is formed. (No BS applies.) Sherardising Prepared iron or steel articles are heated with zinc dust and sand in a slowly-rotating drum at a temperature just below the melting point of zinc, until the zinc has formed an alloy coating over their surfaces. The coating is very even. The process, which gives a matt-grey coat, is mainly used for fairly small articles such as fasteners because of the difficulty of heating the contents of large drums evenly. (See also: BS 4921: 1988.) Zinc-Rich Paints These consist of fine dust suspended in a vehicle allowing very high pigmentation and the formation of an electrically conductive dry film. These paints can be applied to any rust and scale-free steel surface by brushing, spray or dipping, and are mainly used to protect factory steelwork, ships’ hulls and parts of car bodies, and to repair damage to other types of zinc coatings. Automatic grit blasting and paint spraying facilities are widely used in steelworks and shipyards to give steel plates a thin layer of zinc dust paint which provides protection during storage before fabrication. (See also: BS 4652: 1971(1979).) |