Homogeneity is the most desirable factor in the process of mixing. However, achieving homogeneity is a challenging task for mixing highly viscous materials.
Turbulent Flow
A turbine-type mixer creates a chaotic flow when generating turbulence in the lower viscosity ranges of below 5000cps. The face of the rotating blade produces substantial movement radially and axially to distances of two to 10 blade diameters. The flow is more turbulent and extended if the viscosity is low. The flow exhibits isotropic turbulence if the root-mean-square fluctuating velocities are equal. However, this type of turbulence generally lacks rotation or vorticity.
Reynolds numbers are dimensionless values used for describing the boundary between turbulent flow and stable laminar flow. They are calculated from the viscosity, density, and flow velocity of the fluid. The Reynolds number range for turbulent flow is between 1,000 and 100,000 or more based on the impeller type. Impeller power numbers are generally compared in the turbulent range.
Here, a Reynolds number of 2,100 has been taken as the boundary between laminar and turbulent flow. Mixing gets intensified when the Reynolds number goes beyond 2,100. Mixing will be less intense and more streamlined and the viscosity of the overall flow increases when the Reynolds number declines below 2,100. It is to be noted that turbulent motion is not characterized by the intensity alone.
Changing to Viscous Flow
The products need to be moved accurately and intensely by the mixer for high-viscosity mixing. Laminar impellers are generally preferred over turbulent impellers for viscous mixing systems because laminar impellers usually fill the whole mixing tank. Eddy current formation is limited in the viscous range. The high levels of energy imparted by the mixing blade are dissipated within a very short distance, causing localized heat build-up and poor heat exchange.
Selection Criteria of Appropriate Viscous Mixture for a Specific Purpose
The mixing process is generally performed to achieve homogenous blending of two or more ingredients as uniformity can influence the performance, durability, stability, reaction and other factors of the resultant product. Some of the major factors to be considered for achieving uniformity include the mixer design, the times and techniques of loading, discharge, power consumption, cleaning, and maintenance downtime.
Newtonian fluids are materials with low but consistent viscosity. Non-newtonian fluids generally have viscosities more than 500cps. At constant shear rates, there is a drop in viscosity for thixotropic products and increment for rheopectic products in time-dependent systems. In time-independent systems, the viscosity of pseudoplastic products decreases with increasing shear, while dilatant products experience viscosity increase with increasing shear.
Bingham plastic fluids need a minimum shear stress prior to the onset of flow. Viscoelastic fluids show elastic recovery from deformations due to the movement of a mixer blade. The largest group in this category is polymeric fluids, which may exhibit the Weissenberg Effect wherein the fluid climbs up the shaft during the mixing process. The selection of the appropriate mixer is based on the characteristics suitable for a specific product profile, the conditions created by them, and their effect on the mixing process.
Shear typically takes place at low Reynolds numbers and heat is generally a by-product of the stress formed between particles. This stress is prone to tear the particles apart as in the case of viscous flow. Shear is useful in deagglomeration, but is unfavorable in the case of maintaining the particle size in the mixing process.
Maintaining the temperature within a specific range may require additional equipment for heating or cooling the system. In challenging environments, this may include computer-controlled systems that respond to command in controlling heat exchange. Each of these devices will incur additional capital, installation, operating and maintenance costs.
It is to be noted that the most effective mixing system or the ideal system may not be the most affordable. A system’s estimated profitability and the duration of the product’s demand need to be matched against not only the capital and operating costs of the system, but also the expected start-up time needed with such a system. Furthermore, it is important to consider the alternative purpose and resale value of the equipment.
Advantages of Advanced Systems
Closed loop process systems are witnessing a substantial increase in demand owing to today’s safety and environmental concerns. Advanced technologies are available for most mixing and milling operations to achieve improved productivity, quality and reliability. Computer-controlled systems yield accurate weights and measures, and provide on-line, continuous monitoring of batch conditions such as viscosity, pressure, vacuum and temperature. This results in mixing systems is capable of producing exacting results safely and profitably. Some systems can perform waste recycling and self-cleaning.
Although the capital cost of these advanced systems is on the higher side, they avoid the costs associated with insurance to cover spills, workman’s compensation and spoiled batches, thus justifying their higher initial costs by eliminating future liability and litigation costs.
Conclusion
It is not possible to design a mixer capable of fulfilling all mixing needs. Although viscous mixing is a challenging task, it can be simplified through gaining insights into the fundamentals of mixing, asking the appropriate questions and applying scientifically validated test results.
About Hockmeyer Equipment Corporation
Hockmeyer Equipment Corporation has been providing process solutions for over 70 years. It is a leader in the wet grinding and dispersion industry and offers custom designed process equipment for mixing, blending, dispersing and particle size reduction as fine as 25 nano-meters. The Hockmeyer Team is dedicated to building and designing processing equipment that is the highest quality available. Our goal is to increase the profitability of our customers through continuous innovations in process technology.
We are committed to learning our customer’s process so that we can provide the best possible equipment for the application. We will build equipment that is as efficient as possible to reduce the energy requirements, and therefore, the environmental impact of the industries we serve. Hockmeyer offers a state of the art customer service laboratory for product testing and process development.
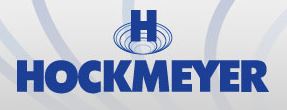
This information has been sourced, reviewed and adapted from materials provided by Hockmeyer Equipment Corporation.
For more information on this source, please visit Hockmeyer Equipment Corporation.