Power plants are required to produce electricity safely and efficiently. However, in relatively a simple change can have a major impact on a power plant’s ability to increase its electricity production and enhance its overall safety.
There are many plants that depend on large amounts of stored hydrogen as a cooling gas for generators, but this approach can result in windage losses and moisture accumulation in the generator casings. These problems not only affect the efficiency of electricity output, but also increase the risk of accidents.
.jpg)
Figure 1. Northern Power Station in Port Augusta switched from bottled hydrogen to an on-site hydrogen generator to supply its two 260 MW turbines with cooling gas.
The Northern Power Station (NPS) in Port Augusta, South Australia has recently replaced its hydrogen gas storage tanks with an on-site hydrogen generation system (Figure 1). This simple change made the facility safer and helped the company to improve its generating efficiency.
Problems with Delivered Hydrogen Gas
.jpg)
Figure 2. NPS installed a Nel Hydrogen H-Series hydrogen generator, which produces 2 Nm3 of ultra pure cooling gas each hour, using only electricity and deionized water.
.jpg)
Figure 3. A pair of Nel Hydrogen StableFlow gas control systems to maintain optimal gas dryness, pressure and purity inside the generators.
Alinta Energy operates a 520 MW coal-fired power station and installed a set of H-Series hydrogen generators (Figure 2) and two StableFlow hydrogen control systems (Figure 3) in 2010 to feed its two 260 MW turbines with cooling gas. For a number of years, the power station received a supply of hydrogen gas cylinders from Adelaide. According to Darwin Chellachamy, production manager from Alinta Energy’s NPS, each week the station required 30 hydrogen gas cylinders to fill its two turbines with hydrogen.
Ultimately, when there was delivery issues, NPS ordered hydrogen cylinders from Sydney. However, the long distance from its gas provider together with the need to have a constant supply of hydrogen gas meant the station had to keep 15 cylinders. But this large number of cylinders has the explosive equivalent of 525 lbs of TNT. Moreover, the station had to comply with different sets of safety regulations to store and handle large amount of hydrogen.
Impure Cooling Gas Leads to Windage Friction Losses
At NPS, the use of delivered hydrogen gas did not allow the turbines to run at their peak efficiency. Also, the delivered gas that was supplied to the turbines was not pure hydrogen. It is a well-known fact that even small reductions in the purity of hydrogen lead to increased windage friction losses within the turbine generators, and these in turn have a direct impact on the efficiency of the power plant.
Air is more than 14 times as dense as hydrogen. Therefore, even low levels of air can significantly increase the density of the gas and this in turn affects its ability to remove heat.
For every 1% of air trapped in a generator casing cooled by hydrogen, there is 250kW drop in electricity production. Since carbon dioxide is 22 times as dense as hydrogen, it has an even bigger impact on electricity production. Impure hydrogen results in revenue loss or increases fuel costs for a power plant.
Hydrogen Dew Point
.jpg)
Figure 4. Average dew points inside turbines.
Chellachamy stated that the dew point of hydrogen gas was a major issue. The hydrogen gas cooling system at NPS can only top up the hydrogen gas within the turbine generator casing, and the old gas dryers failed to operate while the turbines were online. That means the gas was extremely wet when it was entering the generator casings; this can pose a major issue, particularly in warm climates like in South Australia. Preferably, hydrogen dew points should be at about 15°C to -20°C to ensure that condensation is not formed. Figure 4 shows the average dew points within the turbines.
The table below shows the average dew points and purity before and after the Installation of hydrogen generator.
Table 1. Average purity and dew points before and after hydrogen generator installation.
Turbine |
Average purity before generator installation (°C) |
Average purity after generator installation (°C) |
Reading as of 4/30/13 |
Unit 1 |
96.52% |
99.24% |
99.57 |
Unit 2 |
95.35% |
98.66% |
99.44 |
Turbine |
Average dew point before generator installation (°C) |
Average dew point after generator installation (°C) |
Reading as of 4/30/13 (°C) |
Unit 1 |
-1.97 |
-3.23 |
-20.63 |
Unit 2 |
-11.18 |
-10.37 |
-23.26 |
Moisture not only increases the density of the ambient gas in the generator casing, but may also lead to turbine failure. Chellachamy informed that if moisture enters into the rotor retaining rings, they may crack and corrode and this may lead to catastrophic explosion. Explosion and fire from the oil lines, insulation resins and hydrogen gas may also compound the damage. Therefore, condensation could wipe out a turbine and compromise operators’ safety.
In order to reduce the dew points, NPS operators attempted to refrigerate the delivered hydrogen gas and also passed the gas via a desiccant dryer; however, they were only able to achieve a dew point of about 0°C. Moisture issues together with the impurities in the hydrogen gas meant the generators at NPS were experiencing windage friction losses. These losses usually begin at nominal pressure higher than atmospheric pressure and at some nominal purity.
Hydrogen supply requires optimal dew point, pressure and purity to increase output from a generator. These variables were difficult to control at NPS using a stored hydrogen gas supply. As a result, both windage loss and expenses continued to remain high.
On-site Hydrogen Generation System
Chellachamy informed that NPS initially considered replacing its gas dryers. Given that drying equipment is very expensive, it was found to be more cost-efficient to purchase a Proton Exchange Membrane (PEM) on-site hydrogen generation with a StableFlow control system to make sure that the gas which is being used is pure and dry across the entire operation of the power generator.
.jpg)
Figure 5. Average hydrogen purity inside turbines.
An on-site PEM hydrogen gas generator utilizes only electricity and deionized water to generate 99.9995% purity hydrogen at 440 psig (Figure 5). Instead of purchasing 30 hydrogen gas cylinders every month, NPS now pays only for the electricity and deionized water needed to make 2 Nm3 of hydrogen gas per hour. In order to control the purity, pressure and humidity on each generator, NPS installed a pair of Proton OnSite’s StableFlow hydrogen control systems for the steam turbines. By maintaining purity and optimal dryness, windage losses as well as moisture in the casings and on the rings were minimized.
Conclusion
On-site generation means increased efficiency and safety. NPS and other power plants across the globe have found that swapping stored gas with an on-site generator not only saves expenses but also enables safe and streamlined operation. With a hydrogen generator, NPS has a simple, safe and cost-effective way to generate more electricity.
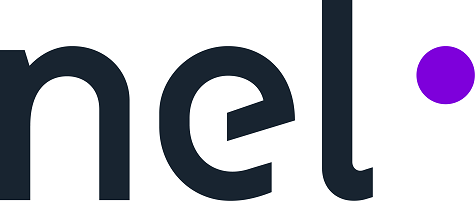
This information has been sourced, reviewed and adapted from materials provided by Nel Hydrogen.
For more information on this source, please visit Nel Hydrogen.