UBE NYLON CoPA 6/6.6 and TerPA 6/6.6/12 have been used in the extrusion of vacuum bagging films and in the fabrication of composite components for some time. Industrial end products are produced using these composite components in industries such as: automotive, construction, energy, nautical and aerospace (Figure 1).
.jpg)
Figure 1. UBE NYLON is used in the manufacture of composite components for use in industries such as: automotive, construction, energy, nautical and aerospace.
UBE NYLON-based Vacuum Bagging Films
Air-blown machines are used for extruding UBE NYLON-based vacuum bagging films (Figure 2). These films form the last layer of a more intricate system of release films and must have a resin (the matrix). The curing or drying of this resin takes place in ovens for several hours in a temperature range of 170-180°C in order to produce the final desired composite component.
.jpg)
Figure 2. UBE NYLON-based vacuum bagging films are extruded using air-blown machines.
Advantages of UBE NYLON
The wide range of melting points of the UBE NYLON provides the option to fabricate vacuum bagging films used for the production of final composite components. The material’s heat resistance property is advantageous in the curing phase of the composite components.
In addition, it has good flex-crack resistance, softness and flexibility/modulus, which are crucial aspects for the efficient and convenient application of the material in the production of composite components.
UBE offers turn-key, thermo-stabilized products to manufacture composite vacuum bagging films from high-quality TerPA 6/6.6/12, CoPA 6/6.6, and PA6. UBE NYLON 5033FD10 is one such thermo-stabilized CoPA 6/6.6 material, which can be readily extruded without the inclusion of any further additives to produce superior quality films. This material can retain efficient functional features and mechanical properties even after curing at extreme conditions.
Conclusion
At its UBE NYLON production plant located in Castellón, Spain, the UBE Group produces the superior quality UBE NYLON in granulate form. By producing the high-quality UBE NYLON, the UBE Group plays a key role in the success of several composite component manufacturers as well in the development of lightweight components, which are advantageous in terms of improved efficiency and reduced cost and waste.
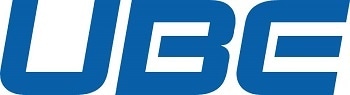
This information has been sourced, reviewed and adapted from materials provided by UBE Group.
For more information on this source, please visit UBE Group.