Conventional or resistance heating is the most common method of heating materials in laboratory applications. Conventionally heated ovens and furnaces use resistance heating elements similar to stove elements. Typical element materials include resistance wire, such as iron-chrome-aluminium alloys and silicon carbide, while other more exotic materials such as molybdenum disilicide, graphite, zirconia and tungsten are also used for specific applications. These materials all generate heat by resisting the flow of electricity through them. The heat generated by the elements is then radiated onto the material being heated. Thus, heating the material from the outside. Since all materials have a characteristic thermal conductivity, there will always be a thermal gradient from the surface to the core of the sample. The temperature of the sample may also be lower than that of the furnace due to the thermal inertia, with larger samples tending to lag more than smaller ones. Microwave Heating Microwave heating differs in that it heats materials volumetrically. In general the surface temperature of a sample is slightly lower due to losses through evaporation, convection, conduction and radiation. These losses to the surrounding environment can be reduced using hybrid heating which employs "susceptors" and "low loss insulation". Susceptors are materials such as silicon carbide which absorb microwave energy efficiently, converting it to heat, which is in turn radiated back onto the sample. Low loss insulation, such as ceramic fibre insulation which can be used to encase the sample, and helps to reduce losses via conduction, convection and radiation. Ceramic materials are often heated in this manner. Susceptors are also used to aid heating at low temperatures, when microwave absorption is low. Why Use Microwave Heating? Due to the fact that materials are heated volumetrically, materials with a uniform microstructure can be produced using microwave heating, if energy losses from the surface are minimised. The nature of microwave heating is also much more efficient compared to resistance heating. These are the main reasons for using microwave heating. The Difference Between Domestic Microwave Ovens and Variable Power Microwave Systems (VPMS) There has been many a researcher who has tried to fire their ceramic component or melt a material in a domestic microwave oven. While they have probably had some degree of success, they have been limited by the simplistic control systems available on domestic and commercial units. Time Slicing Domestic and commercial microwave ovens generally use a time-slicing method to control microwave power to the load, whether the load is anything from a cup of tea to a high precision technical ceramic article. Using this method, maximum power is applied for time intervals which are proportional to the power which the user sets on the controller. For instance, if an operator selects 25% power on a microwave oven rated at 1000W, the device applies maximum power (1000W) for 25% of the time (see Figure 1). 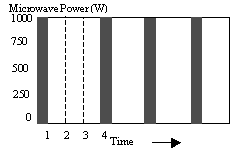 Figure 1. Diagrammatic representation of how time-sliced microwave power is applied to the load Variable Power Microwave Systems (VPMS) In Variable Power Microwave Systems (VPMS), the method in which the power is applied differs in that the power is applied continuously, while the power itself is proportional to that which the operator dials up. If we consider the same scenario as before and the operator selects 25% power, the microwave will deliver 250W of power for the entire duration of the cycle (see Figure 2). 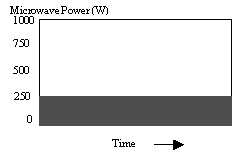 Figure 2. Diagrammatic representation of how microwave power is applied to the load with variable power microwave systems. Several problems may be encountered when people try using domestic microwaves that use the time-slicing technique. The main problem is that the pulsed power can induce uncontrollable exothermic reactions. Also, by pulsing the power, steady heat-up schedules are difficult to achieve. Further, the simplistic control systems available on these units only usually allow a limited number of power steps and do not allow control of heating schedules. By now you may be wondering why this type of control system is used. The answer is price, and price alone. Using time-slicing, manufacturers of domestic and commercial microwave units can keep the price down, which is important from the point of view of the average consumer. As you have no doubt noticed through your own experience, the simple control system is easy to use for the average person and, yes, your dinner does get hot. However, for the researcher and industrialist, who is looking to use microwave technology for drying, sintering, curing, etc., the only solution is a variable power microwave system. These systems allow accurate and continuous control of power to the load. The ultimate solution is a continuously variable microwave system that incorporates power, temperature or other process variable feedback control. This permits control not only of the power that is applied to the load, but also heat-up rates etc. An additional difficulty is the control of heat-up schedules. As the rate at which the load heats up depends on the rate at which heat is lost from the load heat up is a more complex problem than it sounds. |