BINDER’s material test chambers have been providing reliable service at UL International's Thermoplastic Testing Center located in Krefeld, Germany, for many years.
The certified testing center uses BINDER units around the clock (Figure 1). It supplies compounding and provides test specimen manufacturing and testing and accreditation of innovative plastics. More than 200 test procedures have been carried out on standard and advanced plastics for use in a variety of applications. The center uses fully automatic injection molding machines for production of 100 different test specimen forms as outlined in the standards, including CAMPUS, UL, ASTM, and ISO.
.jpg)
Figure 1. Testing around the clock
The Requirements
BINDER in close cooperation with UL TTC employees customized the FP 115 -S test chamber to meet the testing center’s requirements that are specific to its customers. It simplified the calibration of the air change rate and temperature, resulting in improved accuracy. The following are the test requirements to be fulfilled:
- Validation and accreditation of advanced plastics (Figure 2)
- Compound testing in reference to continuance and feature
- Accurate temperature inside the test chamber adhering to a set high air exchange rate
- High reliability around the clock
- Storage time as high as 7,000 hours
- Test specifications according to the standards, including CAMPUS, UL, ASTM, and ISO
- User friendly
- Clear documentation of the test results
.jpg)
Figure 2. Testing of innovative plastics
BINDER’s Bespoke Solution
BINDER implemented a unique concept to measure the air change rate to meet these test requirements. The test center successfully addressed these requirements with the help of BINDER’s APT.line™ technology. The combination of APT.line™ technology and mechanical convection enables rapid heat-up and short drying times, facilitating the accurate testing of materials such as high-performance thermoplastics and polyolefins in a qualified manner.
The units typically run around the clock at the test center, requiring material storage for extended periods of up to 7,000 hours. Cost will be increased exponentially in the event of test failures due to the lengthy storage times. Hence, UL TTC demanded high quality, reliable equipment. BINDER provided the following solutions with its FP 115-S test chamber:
- Material test chamber with forced convection FP 115-S
- Adaptable high air exchange rate
- Homogeneous temperature conditions
- Simplified calibration technology that improves accuracy of temperature and air exchange rate
- Digital documentation of temperature, unit status (ON/OFF) and error messages
- Material test chambers that provide uninterrupted service
- User friendly
The user-friendly material test chamber makes the application simpler for users. Digital temperature settings and an integrated weekly program timer enables data to be collected automatically for temperature, provide unit status, and documents error messages. All relevant data is digitally documented at the testing center. Moreover, the ability to continuously monitor several units from workstations allows the testing center staffs to assess the test procedures and respond rapidly in case of emergency. Figures 3 shows the material test chamber FP 53.
.jpg)
Figure 3. Material test chamber FP 53
Advantages and Applications of BINDER’s Material Test Chambers
The following are the advantages of BINDER’s material test chambers:
- Specialist for challenging heating profiles
- Changeable high air exchange rate
- “Made in Germany” quality
The following are the areas of application of BINDER’s material test chambers:
- Surface industry
- Metal industry
- Plastics industry
- Electronics/semiconductor industry
Conclusion
Besides being highly accurate, all BINDER material test chambers feature a broad temperature range and extensive programming options such as tailored processes, profiles, and ramps.
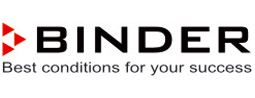
This information has been sourced, reviewed and adapted from materials provided by BINDER GmbH.
For more information on this source, please visit BINDER GmbH.