DePuy Orthopaedic, a subsidiary of the Johnson & Johnson, develops surgical instruments and is in the forefront of new product development processes for medical instruments.
Ogle Models and Prototypes, a company specializing in model making, rapid prototyping and laser sintering, was contacted to oversee the design and development of a novel system to show the critical stages of the surgical procedure performed for total knee arthroplasty, also known as total knee replacement.
Ogle Models and Prototypes had previously worked with DePuy Orthopaedic and produced two new surgical devices for total knee replacement, and thus was selected to handle this latest project.
The goal of the project was to develop a series of six bone models which can be used to practice or demonstrate each step of the total knee replacement procedure (Figure 1). The models also have to be sufficiently strong so that real surgical equipment can be applied at each stage of the procedure. Moreover, the models must reflect the high quality and standards of other products developed by DePuy Orthopaedic.
.jpg)
Figure 1. AAOS bone models
3D CAD Models and Drawings
The project was unique and challenging even by the standards of Ogle Models and Prototypes. As a result, the company contacted Skywide Design, a product design studio, to develop the design process and supply the required 3d CAD models.
During the design process, Skywide Design collaborated with DePuy Orthopaedic to understand its needs and then liaised with Ogle Models and Prototypes to better understand the issues of the development process. According to Andrew Kelly at Skywide Design, working with Ogle Models from the outset of the design process enabled them to customize a design that leveraged processes like rapid prototyping, machining and Vac moulding to deliver a product that was easy to assemble, had minimal part count, and yet was strong and aesthetic.
Printed Test Models, Prototype Rigs and Technical Animations
Right through the development process, important stages of the process were conveyed to the customer by way of prototype rigs, printed test models, and technical animations to demonstrate user interaction. The initial designs were shown to the customer through multimedia presentations and later during the design process certain physical models were developed to verify mechanical interaction of parts.
Ogle Models and Prototypes, on its part, worked closely with Skywide Design's CAD models and drawings and proposed changes where needed. This helped in predicting and resolving issues as early as possible during the process and also assisted in developing the final models quickly and easily.
Ogle Models and Prototypes also created spaces in the models to reflect the operation of real legs so that the joint can be tensioned appropriately.
Skeletal Leg System
A life-sized skeletal leg system was produced by moulding clear silicon onto selective laser sintering (SLS) parts, demonstrating the initial stage of measurement and alignment of the surgical instrument (Figure 2). The end design was a display stand with multiple functions which could change into a training or interactive demonstration aid.
.jpg)
Figure 2. Clear silicon was overmoulded onto SLS parts to create a life sized skeletal leg system.
According to Nick Adams, Project Manager at Ogle Models and Prototypes, working right from the initial stages of the project and prioritizing certain designs due to their longer production cycle helped immensely in successful completion of the project. Skywide’s CAD models and drawings also helped the company in supplying all the parts within the specified time frame.
Conclusion
Development of novel surgical tools and devices is a challenging prospect and can entail a number of processes. The conception of the initial idea through to the design and development phase can take years of testing and dedication, but brings significant benefits to both surgeons and patients and go beyond economic gains. Ogle Models and Prototypes is well-known for applying its expertise to medical device development programs and provides optimum solutions quickly and efficiently in a short lead time.
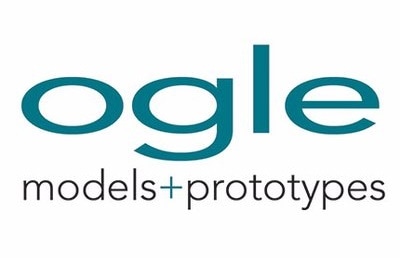
This information has been sourced, reviewed and adapted from materials provided by Ogle Models and Prototypes.
For more information on this source, please visit Ogle Models and Prototypes.