With the advent of catalytic converters in car exhaust systems, catalytically active metals such as rhodium (Rh), palladium (Pd), and platinum (Pt) were predominately used in the automotive industry. In 2012, about 80% of the total Rh, 74% of the total Pd and 40% of the total Pt were consumed by the auto catalyst industry.
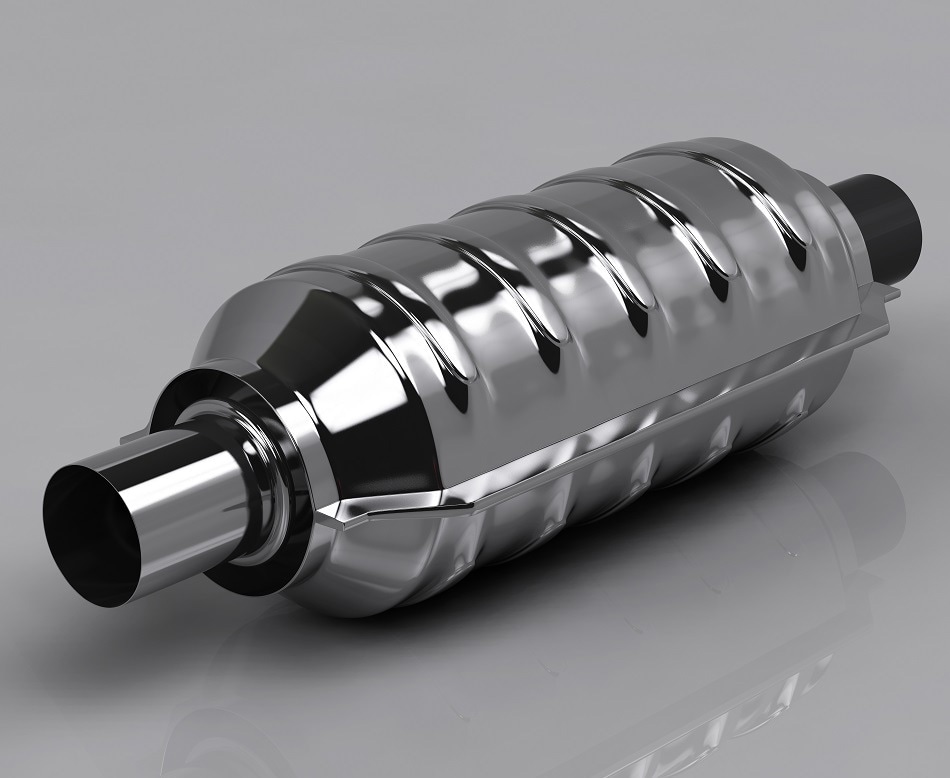
Image Credits: shutterstock.com/Einar Muoni
A catalytic converter typically includes Pt, Pd and Rh that are fused onto a large area of a substrate, such as cordierite or alumina. This is integrated in a metallic case that is connected to the car exhaust system to convert toxic nitrogen oxides (NOx) and carbon monoxide (CO) into water (H2O), carbon dioxide (CO2), nitrogen (N2), and oxygen (O2) that are green and eco-friendly.
The content of Rh, Pd and Pt in an automotive catalytic converter differs depending on the type of fuel utilized and the cubic capacity of the engine and may include only Pt or various ratios of Pd-Rh, Pt-Rh and Pt-Pd-Rh. For CO and hydrocarbon oxidation, platinum and palladium are utilized, while for NOx reduction rhodium is employed.
However, Rh, Pt and Pd are limited natural resources and there is significant amount of costs involved to extract and refine them. Therefore, an alternative way to obtain these metals is by recycling unused or old automotive catalysis converters.
However, some key factors must be taken into account while acquiring and recycling autocatalyst scraps, for instance there would be variable compositions and prices of Rh, Pt and Pd would be highly volatile. In order to prevent these significant costs, it is important to accurately determine the content of Rh, Pt and Pd in the autocatalyst scraps available at the refineries or at the collector's site.
Analytical labs often employ an Aqua Regia digestion process using a microwave digestion system so that the crushed and milled substrates of the catalytic converters are amenable for determining their active metal content by inductively coupled plasma spectrometry. These digestion procedures, however, takes considerable amount of time and do not enable a complete dissolution of samples.
Although concentrated sulfuric (H2SO4) and hydrofluoric (HF) acids could result in complete dissolution of samples, use of such hazardous acids can prove dangerous. Moreover, highly skilled chemists are required to perform these multi-steps digestion procedures, making them impractical for labs handling innumerable samples per year.
Sodium Peroxide Fusion Method
A sodium peroxide fusion method developed by Claisse® enables complete dissolution of samples of automotive catalytic converters substrates. In tandem with a simultaneous ICP-OES, this method provides excellent accuracy for determining the contents of Rh, Pt and Pd in autocatalysts. The Claisse® fusion method is not only fast, but also enables complete sample dissolution; it also removes the use of hazardous acids and shows good recovery for Rh, Pt and Pd metals.
Experimental Method
Sample Preparation by Peroxide Fusion Peroxide
- CLAISSE® Peroxide™ Fluxer (Figure 1)
- Zirconium crucibles and covers (Figure 2)
- 3.0g of sodium peroxide flux
- 0.25g of ground sample
- 3.5 minutes of heating at 600°C temperature
- 4.0 minutes of cooling
- Dissolution in a HNO3 or HCl solution (Figure 3)
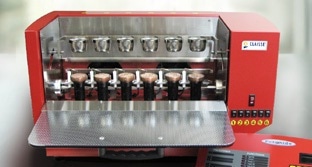
Figure 1. Claisse ' PeroxideTM Fluxer
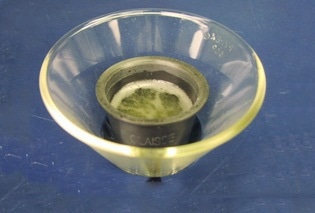
Figure 2. Zirconium crucibles and covers
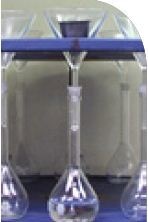
Figure 3. Dissolution in a HCl/HNO3 solution
Analysis by ICP-OES
Figure 4 shows the PerkinElmer® OptimaTM 7300DV and Table 1 gives the operating parameters for the OptimaTM 7300 DV. Table 2 shows the certified reference materials utilized to verify the newly developed method, and Table 3 displays the analytes of interest.
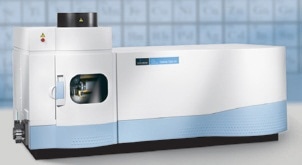
Figure 4. PerkinElmer OptimaTM 7300DV
Table 1. OptimaTM 7300 DV operating parameters
Plasma flow rate (Ar) |
16 L/min |
Auxiliary gas flow rate |
0.4 L/min |
Nebulizer flow rate |
0.8 L/min |
Sample flow rate |
1.0 mL/min |
Rinse |
2.5 mL/min (2 min < 10 ppm;
added 90 sec for > 10 ppm) |
Shear gas pressure |
100 PSI |
RF Power |
1500 W |
Table 2. Certified reference materials used to validate the developed method
Sample |
Supplier |
Certified Reference Material ERM®-EB504 |
BAM |
Certified Reference Material SRM 2556 |
NIST |
Table 3. Analytes of interest with selected wavelengths, method detection limits (MDL) and viewing modes
Element |
Wavelength (nm) |
Viewing mode |
MDL (%) |
Pd |
248.892 |
Axial |
0.001 |
Pt |
193.700 |
Axial |
0.003 |
Rh |
343.489 |
Axial |
0.002 |
Results
Tables 4 and 5 show the accuracy and precision measurements on ERM®-EB504 and NIST SRM 2556 certified reference materials, respectively. Table 6 illustrates the recovery results on pre- fusion spiked CRMs and samples to confirm the method.
Table 4. Accuracy and precision measurements on ERM®-EB504
Element |
Wavelength (nm) |
Average Experimental values (%) n=10 |
Certified values (%) |
Accuracy (%) |
RSD (%) |
Pd |
248.892 |
0.026 |
0.0279 |
93 |
4 |
Pt |
193.700 |
0.17 |
0.1777 |
94 |
3 |
Rh |
343.489 |
0.034 |
0.0338 |
100 |
2 |
Table 5. Accuracy and precision measurements on NIST SRM 2556
Element |
Wavelength (nm) |
Average Experimental values (%) n=10 |
Certified values (%) |
Accuracy (%) |
RSD (%) |
Pd |
248.892 |
0.030 |
0.03326 |
92 |
2 |
Pt |
193.700 |
0.068 |
0.06974 |
98 |
3 |
Rh |
343.489 |
0.003 |
0.00512 |
(62) |
3 |
Table 6. Recovery results on pre-fusion spiked CRMs and samples to validate the method (n = 5)
Element |
Wavelength (nm) |
ERM®-EB504 (%) n=5 |
SRM 2556 (%) n=5 |
Pd |
248.892 |
89 |
105 |
Pt |
193.700 |
89 |
94 |
Rh |
343.489 |
99 |
107 |
Discussion
By using sodium peroxide, samples can be prepared within a matter of minutes with complete dissolution. This method has a very high throughput and provides a number of benefits over other dissolution techniques that are typically brought on by their temperature stability and versatility.
However, sodium peroxide results in higher concentration of salt in the solutions which then have to be diluted so that the salts do not damage the spectrometer. When solutions obtained from alkaline fusion are injected in an optical ICP, the total dissolved salt concentration of these solutions should be 1.5% or less.
Using Cd 226.502 and matrix matching as an internal standard, in addition to rigorous interference management methods, recoveries of 100 ± 11% were obtained for elements in both CRMs, as indicated in Table 6. Tables 4 and 5 show RSDs that are less than 4% for all the elements, and thus demonstrate a good reproducibility throughout the analytical process.
The level of dilution employed in the method did not allow the quantification of Rh in CRM NIST SRM 2556 because its concentration in the diluted sample was less than that of the quantification limit. Nevertheless, for recovery measurements, a spike was introduced to the solutions which facilitated representative recovery measurements, even on Rh.
Conclusion
Microwave acid digestion recipes are not only arduous, but also time-consuming and may not allow complete dissolution of samples, while atocatalysts materials are complex to prepare for analysis by common hot plates and ICP. In contrast, peroxide fusion has shown to be a practical alternative for sample preparation to determine PGM content. Together with a simultaneous ICP-OES, peroxide fusion method has the required analytical capabilities to carry out the analysis of low concentrations of PGM on catalyst supports.
In this experimental study, active metals such as rhodium, platinum and palladium were determined in two automotive reference materials with excellent precision, accuracy, and recovery. Peroxide sample preparation by fusion method offers a number of advantages. For instance, the method is user-friendly over other sample dissolution recipes, enables fast dissolution of samples, and eliminates the use of HF and other hazardous acids.
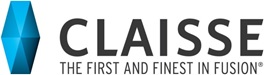
This information has been sourced, reviewed and adapted from materials provided by Claisse.
For more information on this source, please visit Claisse.