The selection of an appropriate leak detector, which meets the needs of a production leak testing application, is a great challenge for engineers. In general, there are a number of leak detection methods.
However, when the leak rate requirement is between 10-6 and 10-10 atm.cc/s, tracer gas methods are the best choice, delivering repeatable and precise results. Helium leak detection is the right option for leak rate between 10-6 and 10-10 atm.cc/s.
This article covers the key parameters that help in choosing and deploying the appropriate helium leak detector. It further describes the helium hard vacuum method, which can be implemented using an outside-in approach or an inside-out approach. Figure 1 shows the schematic representation of helium hard vacuum method implementation.
.png)
Figure 1. Hard vacuum leak detection methods
Leak Test Process
A helium leak test cycle involves two separate primary phases: the pump down step and the helium measurement step.
The pump down time is the time taken to achieve a specific vacuum level within the test chamber where a pressurized part is located. It is calculated based on the “in-leakage” and “outleakage” approach. The pump down phase is carried out using a vacuum pump for evacuating the test chamber.
Upon reaching the desired test pressure, the helium leak test can be carried out. The amount of helium leaking in or out of the part is then measured using the leak detector analyzer cell, and the values are displayed on the leak detector operator interface.
Pump-Down Time and Inlet Test Pressure Cross Over
When the test chamber is linked with the inlet of a leak detector, the vacuum pump or roughing pump begins to evacuate the chamber, until a vacuum level which changes the leak detector to gross test mode is achieved.
This vacuum level is called the inlet test pressure. The formula given in Figure 2 shows that a specific vacuum level can be more rapidly achieved when the roughing pumping speed of the rough vacuum pump is higher.
A typical leak detector has several test modes such as fine, medium and gross. The gross leak test port is mostly connected to the exhaust of the high vacuum pump. In gross leak mode, the vacuum level maximum inlet test pressure varies between 1 mbar to 25 mbar. The gross leak can be performed at a faster rate when the maximum inlet test cross over test pressure is higher. Figure 3 shows the schematic of inlet cross over test pressure.
.png)
Figure 2. Schematic of pump down time
.png)
Figure 3. Schematic of inlet cross over test pressure
Conductance in Vacuum Regime
In most of the cases, the test chamber is not placed directly at the detector inlet. A vacuum line is used to connect the chamber and the inlet. The type of vacuum line used can influence the pump down time. The property of the vacuum line to allow the passage of gas in the presence of vacuum is known as the conductance. With larger conductance, the gas transfers from the chamber to the leak detector at a faster rate.
Usually, there are four vacuum gas flow regimes of which two are most important: the viscous and the molecular regimes. The viscous regime is encountered during the roughing pump down phase, while the molecular regime is achieved when the leak detector is in fine leak test mode.
The vacuum regime within the vacuum line normally transitions from viscous to molecular regime at the end of the leak test cycle, while the atmospheric pressure reduces to 10-3 mbar.
The corresponding formula for conductance in viscous and the molecular regimes of the vacuum line is shown in the Figures 4 and 5.
.png)
Figure 4. Conductance in viscous regime
.png)
Figure 5. Conductance in molecular regime
The conductance will be greater in a molecular than in a viscous regime, and hence care should be taken while choosing the vacuum line. Conductance for air and helium in molecular regime can be easily measured as they depend on the vacuum line dimensions.
About LACO Technologies, Inc.
LACO Technologies, Inc. is a leading manufacturer of vacuum and leak testing systems. Driven by innovation, service, and quality we strive to be the best provider of standard and custom vacuum and leak testing solutions.
Established in 1975, LACO Technologies is located in Salt Lake City, Utah, and serves customers across the United States and internationally.
Owned by engineers, LACO is uniquely situated to provide innovative solutions for vacuum and leak testing applications. We work with diverse customer applications and are dedicated to creating the right solution to help our customers achieve their goals.
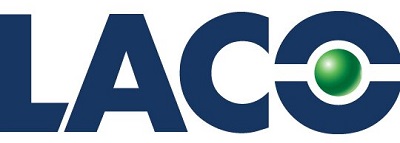
This information has been sourced, reviewed and adapted from materials provided by LACO Technologies, Inc.
For more information on this source, please visit LACO Technologies, Inc.