Feb 4 2002
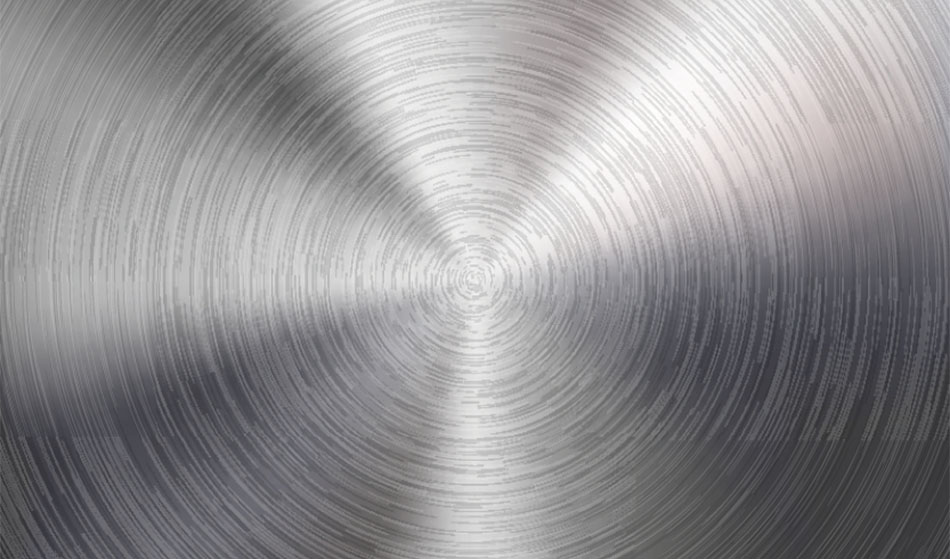
molaruso / Shutterstock
At temperatures greater than 1350 °C, solid-state reaction of titania and alumina leads to the synthesis of aluminum titanate. Depending on its reactivity, the synthesized powder can be sintered at temperatures of 1400 °C–1600 °C in air. The crystal structure of aluminum titanate is pseudobrookite.
Ceramics that are made from aluminum titanate exhibit excellent thermal shock resistance. This is mostly due to its extremely low thermal expansion coefficient caused by the substantial anisotropy in the material’s properties.
Expansion along the a- and b-axes direction is positive, while the same in the c-axis direction is negative. Apart from producing almost zero thermal expansion, this causes microcracks in the sintered material, leading to moderately low material strength. SiO2 and MgO are additives used to prevent strength degradation. Strengths up to 100 MP have been specified for experimental materials.
Key Properties
The key properties of aluminum titanate have been shown in Table 1.
Table 1. Typical physical properties for aluminum titanate
Property |
Density |
3-3.4 g.cm-3 |
Modulus of Rupture @ RT |
30 MPa |
Modulus of Rupture @ 1000 °C |
60 MPa |
Young's modulus |
20 GPa |
Thermal expansion (20-600 °C) |
0-1 x10-6 K-1 |
Thermal expansion (600-1000 °C) |
1-2 x 10-6 K-1 |
Thermal conductivity (RT-1000 °C) |
< 2 W.m.K-1 |
Maximum service temperature |
1000 °C continuous
1100 °C intermittent |
Thermal shock resistance |
Excellent |
Resistance to molten metals |
Good |
Applications
The material has excellent thermal shock resistance, low thermal conductivity, and optimal chemical resistance to molten metals. These properties enable the material (mainly aluminum) to satisfy several metal-contact applications in the foundry sector such as crucibles, plugs, riser tubes, ladles, launders, and pouring spouts.
When compared to competing materials like calcium silicate and fused silica, components manufactured using aluminum titanate have significantly longer service life.
Moreover, aluminum titanate is utilized as an insulating liner in the automotive sector for exhaust manifolds, where there is a need to reduce heat loss before a turbocharger. In this article, the metal exhaust manifold is cast over the molded aluminum titanate liner. The difference in the thermal expansion between the steel and aluminum titanate manifold during cooling maintains the ceramic in compressed state. This helps in resolving the problems associated with its low strength.