The removal of particles from a fluid is known as filtration. One of the common uses of liquid particle counters is to evaluate the efficiency of filters to remove particles of various sizes. Some of the common uses include; laboratory testing of filtered fluids, upstream/downstream filter testing, and point-of-use (POU) monitoring. This article focuses on the Entegris AccuSizer, which is used in many industries, for all three purposes.
Significance of Filtration
As stated earlier, filtration is the mechanical or physical removal of solids from fluids (liquid or air). This is achieved when the liquid passes through a filter medium, which reduces the number of particles existing in the liquid. The filter’s fluid upstream is the feed, and the fluid passing through the medium is referred to as the filtrate (Figure 1).
.jpg)
Figure 1. Simple filtration
Various kinds of filter media are available for use, such as filter paper, activated carbon, diatomaceous earth, and cartridges. Since different media have varying efficiencies, at varying size ranges, the user has to select the suitable media for the required particle removal.
Hydraulic fluid power systems separate and lubricate the components moving parts. Solid particulate contamination results in wear, which reduces efficiency and shortens the components life. In a hydraulic filter, the number of particles circulating within the system is controlled to match the level of the desired system reliability. Testing of hydraulic filters is one of the common uses for liquid particle counters, including the Entegris AccuSizer.
In the microelectronics industry, CMP slurries are usually filtered during their production and use. By using a filter, the large particles, which are formed during production, can be removed from the slurry to achieve scratch-less wafers. During some applications, the filter’s life is compromised, and large particles that are formed after filtration cause defects on wafers. Deciding on the exact time to change these filters, according to actual particle count rather than duty cycle or pressure, enhances yield and reduces filtration expense.
The pigments that are formulated into inkjet inks are usually dispersed to smaller particle sizes (between 50 and 200 nm), and have to be made colloidally stable. The pigment particle’s size is crucial, as large particles can plug the channels and jets, and damage the print head. The control of the content of large particles (> 0.5-1.0 µm) needs a technique that is sensitive to a small number of large particles – the tail of the distribution.
Filter Testing
Users and manufacturers of industrial filters test filters during designing, manufacturing, and selection process to identify the filters that match a given application. One of the common approaches to filter test is to measure the upstream and downstream of a filter using two liquid particle counter sensors (Figure 2). Using the Entegris AccuSizer, a customer can select from several sensors that are available, depending on the size and concentration. A common sensor for hydraulic fluid filter testing is the LE-400 sensor that has a range from 0.5-400 µm. The counter has 512 size channels of resolution, much more than the usual user requirements. Automatic dilution can also be enabled in the feed sensor if needed.
.jpg)
Figure 2. Filter test stand
A typical data interpretation of hydraulic filter testing, as specified in ISO 16889, is the filtration ratio (or Beta ratio).
.jpg)
CMP Slurry
The AccuSizer is employed in laboratories and processes around the world to monitor CMP slurry health and optimize filtration to minimize surface defects. AccuSizer particle count data for upstream (blue) and downstream (red) of the filter is shown in Figure 3.
.jpg)
Figure 3. CMP slurry upstream/downstream of filter
Inkjet Inks
The results of a filtration test where inkjet ink is filtered using a 2 µm filter and a 5 µm filter are displayed in Figure 4. The two filters show improvement in the concentration of particles less than 1 µm. The unfiltered sample contained more than 100,000 particles/mL greater than 1 µm while the 5 µm and 2 µm contained ~70,000 and ~20,000 particles/mL respectively.
.jpg)
Figure 4. Inkjet ink unfiltered and filtered at 5 and 2µm
Conclusions
The Entegris AccuSizer is an ideal system to test filters and perform many filtration efficiency experiments. The sensors are based on single particle optical sizing (SPOS), and have the broadest size and concentration ranges.
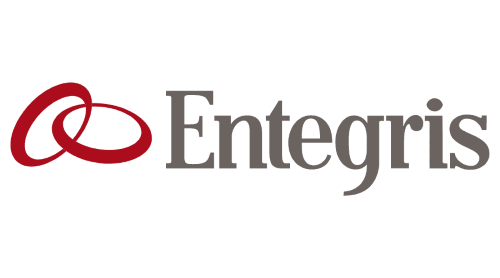
This information has been sourced, reviewed and adapted from materials provided by Entegris
For more information on this source, please visit Entegris