Heat transfer fluids can get degraded in two ways:
- If a hot fluid is exposed to air for a longer period of time, oxidation takes place. The resultant acids have poor thermal stability and get further degraded at comparatively lower operating temperatures, e.g. 400°F. Acute oxidation results in heater buildups, sludge, and exceptionally high viscosity, i.e. fluid becoming thicker, at atmospheric temperature.
- Overheating takes place as a result of heating a fluid above the maximum film temperature specified by the fluid manufacturer. The maximum film temperature is the fluid temperature on the inner wall of the heater tube or on the surface of the electric element. Such extreme temperatures result in breaking apart or cracking of the fluid molecules, thereby decreasing the viscosity, i.e. thinner fluid. Cracking may also lead to pump cavitation. Solid carbon particles are formed as a result of extreme overheating.
Causes and Cures
Degradation of a heat transfer fluid can be effectively checked by performing an annual fluid analysis that includes a distillation range, or boiling point, test for measuring the amount of cracked molecules, i.e. low boilers, and an acid number test for measuring oxidation. As soon as the issue is recognized, the causes and cures are quite straightforward.
Hot Expansion Tank/Reservoir
Oxidation takes place only in the expansion tank, or the reservoir. The tank normally turns hot during the system start-up due to the expansion of the fluid into it. As soon as the system attains the operating temperature, the tank must be cooled such that one can place a hand on it; a temperature of about 140°F is the threshold of pain for most of the people. A popping sound from the inner side and smoke emanating from the vent indicate that the tank is very hot.
Care must be taken to ensure that all the boilout/warmup lines reaching the tank are valved off once the temperature of the heater outlet reaches 250°F. During normal operation, only one line must connect the tank to the main loop. If a combination deaerator/expansion tank is integrated into the system, the manufacturer’s instructions concerning the part to be insulated should be thoroughly followed. If all the measures fail, then a nitrogen blanket should be installed on the tank head space.
Burner Problems
A prevalent source of overheating is flame impingment. In the majority of fired heaters, the area of the radiant zone, i.e. the coil surface actually facing the flame, is less than 30% of the area of the total heated surface but it contributes to about 50%-70% of the total heat transfer. The high heat-to-surface-area ratio is the reason for the high film temperature in the heater. In the case of a corroded flame disperser or a mis-aligned burner, the flame may directly impinge onto the surface of the coil, resulting in extremely high film temperature that can surpass the recommended maximum film temperature for the fluid. If this issue is not fixed promptly, it may lead to heater tube failure.
Low Flow
Another reason for overheating is the decrease in flow rate through the heater. The transfer of heat from the heater tube wall, i.e. the electric element surface, is affected by low flow in the following two ways:
- When the volume of fluid is relatively less to remove the heat, then the overall fluid temperature raises.
- When the turbulent flow is reduced, the mixing of the hot fluid with the cooler fluid at the element surface or the tube wall is reduced, resulting in an increase in temperature of the film.
Yet other common reasons for low flow are improperly set or malfunctioning bypass valves and plugged Y-strainers.
Degradation: Special Case
Invariably, thermal fluid system contamination is mostly self-inflicted. It occurs when a fluid of poor thermal stability, i.e. hydraulic fluid and glycol that are usually stored in drums in the same area, is added mistakenly. An instantaneous consequence may be a “geyser” emanating from the expansion tank vent or pump cavitation. However, mostly the increase in the quantity of carbon solids in the fluid is the only indication for contamination to have taken place.
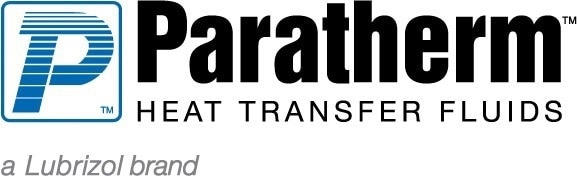
This information has been sourced, reviewed and adapted from materials provided by Paratherm.
For more information on this source, please visit Paratherm.