A heat transfer fluid’s operating life and performance can be increased by carefully following the shutdown procedures of a thermal oil system. Otherwise, the system can be eventually damaged due to overheating or “bruising” of the fluid. This article presents the consequences of an improper shutdown.
Normal System Operation
During the normal operation of a thermal oil system, the radiant and convective heat provided by the thermal fluid heater to the heater tubing positioned in the firebox is transferred to the film layer of the fluid through the tube wall. As the fluid is in a turbulent state, its film layer constantly mixes with the bulk of the fluid and swiftly transfers the heat. By means of the high flows provided by the circulating pump, the heat is quickly carried to the user by the fluid, which returns at a lesser temperature to carry more heat.
At normal working temperatures, the temperature of the refractory and structural metal parts of the heater may be equal to that of the flame itself. When the thermal oil system is shut down, it takes some time for the heat in these materials to entirely radiate and exit the stack. As certain heaters are equipped with more refractory parts than others, although the firebox temperature may be the same, it takes more time to radiate the additional stored heat.
If the fluid circulates even after the heater is shut down, it continuously carries this BTUs from the heater and distributes them to the entire system.
Improper Shutdown
On the contrary, if the entire thermal oil system is shut down instantaneously, the heater stops firing and the pump does not circulate the fluid. Consequently, the heat stored in the refractory and structural metal parts of the heater is transferred to the firebox.
As the blower is turned off, this heat does not exit the stack immediately, resulting in the experiencing of intense heat by the heater tubing comprising the heat transfer fluid. As the fluid is stagnant, it cannot remove the heat and starts to boil once its skin temperature surpasses the recommended limit. The occurrence of this boiling can be clearly heard when listened carefully.
Film Boiling
Most of the liquid-phase heat transfer fluids possess multiple boiling points. The larger molecules normally boil at higher temperatures and the smaller molecules at lower temperatures. Even when the flame is turned off and natural convection currents start to flow into the firebox, internal temperatures may remain hot enough for the mid-sized and smaller molecules of the fluid to be vaporized. After these molecules are boiled off, larger molecules continue to exist. The higher percentage of large molecules directly corresponds to higher viscosity of the heat transfer fluid.
If the fluid becomes thicker, it does not quickly flow through the thermal oil system. Conversely, more horsepower may be needed to attain the same flow. Thus, system performance is considerably reduced. Moreover, a slowly flowing fluid may continue to remain in contact with the heated surface for a longer period of time, thus getting further overheated and damaged.
Besides, if the flow is significantly reduced, the temperature of the fluid’s film layer can be greatly increased, thus causing fluid degradation and hence, leading to fouling of the thermal oil system with hard baked-on carbon deposits and sludge.
Shutdown Procedures
While shutting down a thermal oil system, the heater should be turned off but the circulating pump should be left running to enable the heat stored in the refractory and structural metal parts to exit the firebox. The heater outlet temperature and the stack temperature should be monitored. Generally, the pump can be safely shut down if the heater outlet temperature is reduced to lower than or equal to 250°F.
While it is a common procedure to retain the pump in operation till the heater outlet temperature decreases, this can lead to wastage of electricity, especially in well-insulated thermal oil systems in which the cool-down may happen over extended periods of time. In such cases, the pump should be left running only until excess heat radiated from the refractory and structural metal parts exits the firebox. This can be achieved by installing a thermostat and relay that can automatically shut down the circulating pump upon reaching preset temperature.
If possible, the heater blower can be kept running. Heat can also be made to more quickly exit the stack by forcing cool air into the firebox.
Paratherm | Heat Transfer Fluids | Hot-Oil Technology Made Easy
Power Failures
While using emergency power in case of occasional power failures, it is better to tie-in the blower and the circulating pump of the thermal oil system. The cost of an emergency power hook-up is much less when compared to the cost of heat transfer fluid replacement and the associated downtime.
Alternatively, the heater manufacturer can be requested to specify the pump run-time needed to completely exhaust the excess heat for that specific heater. The pump run-time can be as short as 30-60min in heaters with better air circulation, less amount of refractory, and better stack draw.
For using the thermostat and the relay, the heater manufacturer can be requested to advise regarding the optimum location of the sensor and temperature set points for the thermostat.
A nevertheless more important word of caution is that the pump should be allowed to run until exhaustion of the stored heat even in thermal oil systems that operate at or close to 250°F. If not, the heat transfer fluid is prone to damage.
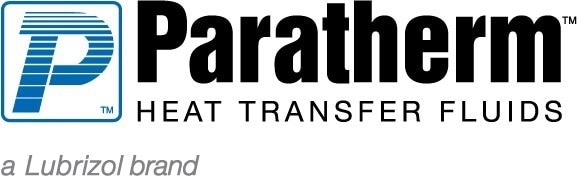
This information has been sourced, reviewed and adapted from materials provided by Paratherm.
For more information on this source, please visit Paratherm.