Stainless steels contain several alloying elements that are in line with the specific composition and grade. The following sections describe the alloying additions and the reasons they are present, and a summary table of each alloying element.
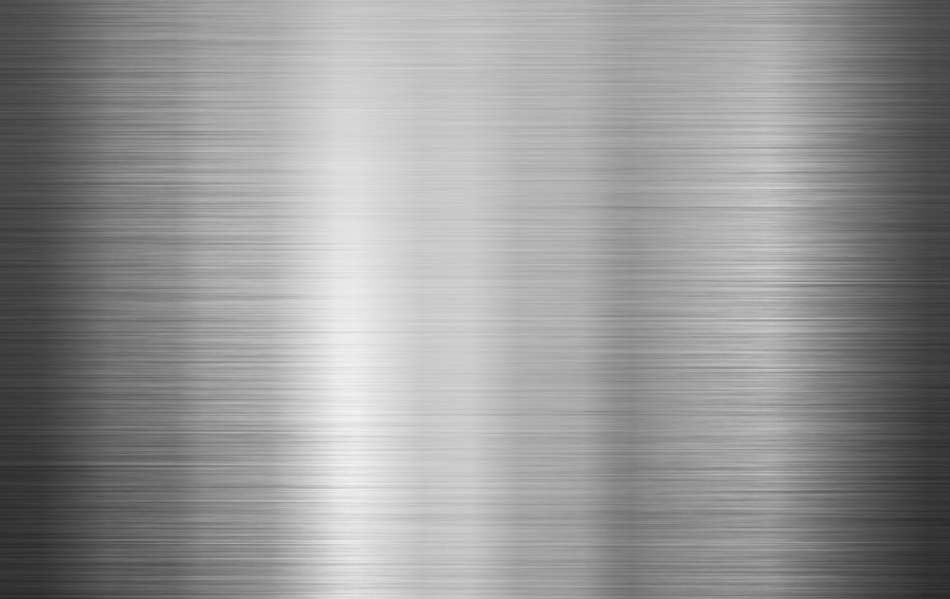
Image Credit: Shutterstock/Nutthpol Kandaj
Carbon
Carbon and iron are alloyed together to form steel. This process boosts the strength and hardness of iron. Heat treatment is not adequate to strengthen and harden pure iron, but when carbon is added, a wide range of strength and hardness is realized.
High carbon content is not preferred in Ferritic and Austenitic stainless steels, specifically for welding purposes, due to the risk of carbide precipitation.
Manganese
The addition of manganese to steel improves hot working properties and boosts toughness, strength, and hardenability. Just like nickel, manganese is an Austenite forming element and has been traditionally used as a replacement for nickel in the AISI200 range of Austenitic stainless steels, for example AISI 202 as a replacement for AISI 304.
Chromium
Chromium is combined with steel to improve it's resistance to oxidation. When more chromium is added, the resistance is improved further.
Stainless steels have at least 10.5% chromium (usually 11 or 12%), which imparts a considerable level of corrosion resistance, compared to steels with a relatively lower percentage of chromium.
The resistance to corrosion is attributed to the formation of a passive, self-repairing layer of chromium oxide on the stainless steel surface.
Nickel
Large amounts of nickel - more than 8% - is added to high chromium stainless steels to produce the most important group of steels that are resistant to both heat and corrosion.
These include the Austenitic stainless steels that are characterized by 18-8 (304/1.4301), where nickel’s tendency to form Austenite contributes to high strength and excellent toughness or impact strength, at both low and high temperatures. Nickel also significantly improves resistance to corrosion and oxidation.
Molybdenum
When mixed with chromium-nickel austenitic steels, molybdenum enhances resistance to crevice and pitting corrosion, particularly in sulphur and chlorides-containing environments.
Nitrogen
Similar to nickel, nitrogen is an Austenite forming element and increases the Austenite stability of stainless steels. When nitrogen is mixed with stainless steels, yield strength is considerably enhanced along with increased resistance to pitting corrosion.
Copper
In stainless steel, copper is often present as a residual element. This element is added to several alloys to create precipitation hardening characteristics or to improve corrosion resistance, predominantly in sulphuric acid and sea water conditions.
Titanium
Titanium is often added to stabilize carbide, particularly when the material has to be welded. Titanium merges with carbon to form titanium carbides that are relatively stable and cannot be easily dissolved in steel, which is likely to reduce the occurrence of inter-granular corrosion.
When around 0.25 / 0.60% titanium is added, it causes the carbon to merge with titanium as opposed to chromium, avoiding a tie-up of corrosion-resistant chromium as inter-granular carbides and the associated loss of corrosion resistance at the grain boundaries.
In the past several years, the use of titanium has considerably reduced because of the ability of steelmakers to supply stainless steels that have extremely low carbon contents. Such steels can be readily welded without any need for stabilization.
Phosphorus
In order to improve machinability, phosphorus is often added with sulphur. While the presence of phosphorus in Austenitic stainless steels boosts strength, it has a detrimental effect on corrosion resistance and increases the material’s tendency to break during welding.
Sulphur
Sulphur improves machinability when it is added in small quantities, but just like phosphorous, it has a negative effect on corrosion resistance and the subsequent weldability.
Selenium
Selenium was previously employed as an addition to enhance machinability.
Niobium/Colombium
Carbon stabilization is achieved by adding niobium to steel, and performs in the same manner as titanium. In addition, niobium strengthens alloys and steels for increased temperature service.
SiIicon
Silicon is typically employed as a deoxidizing (killing) agent in the steel melting process, and a small amount of silicon is used in most steels.
Cobalt
When subjected to strong radiation of nuclear reactors, cobalt becomes highly radioactive and hence, all stainless steels deployed in nuclear service will have certain cobalt limitation, often 0.2% at the most.
This issue is important as some amount of the remaining cobalt will be present in the nickel used to make Austenitic stainless steels.
Calcium
Calcium is added in small amounts to enhance machiniability, without having any detrimental effect on other properties induced by selenium, phosphorus and. sulphur.
The following table shows the effect of alloying elements on properties of stainless steel.
Effect of alloying elements on properties of stainless steel
Property |
C |
Cr |
Ni |
S |
Mn |
Si |
P |
Cu |
Mo |
Se |
Ti or Nb |
Corrosion Resistance |
- |
√ |
√ |
X |
- |
- |
X |
- |
√ |
- |
- |
Mechanical Properties |
√ |
√ |
- |
- |
√ |
√ |
√ |
√ |
√ |
- |
√ |
High Temperature Resistance |
- |
√ |
√ |
X |
- |
- |
- |
- |
√ |
- |
√ |
Machinability |
X |
X |
- |
√ |
- |
- |
√ |
- |
- |
√ |
- |
Weldability |
X |
X |
- |
X |
√ |
- |
X |
- |
√ |
- |
√ |
Cold Workability |
X |
X |
√ |
X |
- |
- |
- |
√ |
- |
- |
- |
Key
√ = Beneficial
X = Detrimental
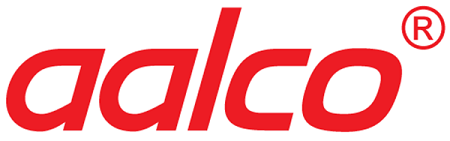
This information has been sourced, reviewed and adapted from materials provided by Aalco - Ferrous and Non-Ferrous Metals Stockist.
For more information on this source, please visit Aalco - Ferrous and Non-Ferrous Metals Stockist.