Sep 22 2016
Semiconductor circuits (patterns) printed on semiconductor wafers (substrates) are shrinking, while such substrates are becoming larger in physical size. Over the years, the inspection of patterned wafer defects has transformed from a physical operation to a completely automated process.
Equipment meant for automated wafer inspection was often used in engineering environments, however recent developments in inspection technology, together with the well-documented yield enhancements achieved with automation, has made automated wafer inspection an important part of the production manufacturing strategy.
This article describes an optical inspection system employed with a Prior ProScan motorized XY stage, theta (rotation) wafer chuck, ProZ motorized column, and a controller to inspect the surface of a wafer.
Equipment
The following software and hardware was utilized:
- Prior H116 motorized and programmable XY stage with linear encoders
- Prior ZC12 ProZ motorized column with mount for microscope optics
- Prior PS3J100 XYZ joystick control
- Prior H31XYZEF ProScan III controller
- Prior HWCV motorized wafer rotation chuck with vacuum hold down
- MIS Pax-it! Imaging and motion control software package
- MIS PaxCam high-resolution digital camera
- Desktop PC running windows 7 and large format color flat panel monitor
- Olympus UIS BF/DF optics with motorized objective turret and auto focus
ProScan Controller Programming
There is no need for special programming of the ProScan controller. Using Prior Scientific’s standard SDK, the software developer (MIS In this case) controlled all of the hardware to perform inspection-related automated tasks.
Application
Normally, wafer inspection relies on human operators to locate defects in the printed patterns or on the surface of the wafer through a microscope.
However, this process is not only laborious but also creates ergonomic problems for operators. Operator fatigue can also potentially lead to more errors.
In the case of the semi-automated system (Figure 1), all the operator has to do is to mount a wafer on the stage and simply press several buttons.
After this, two critical alignment functions will be initialized by the defect review and motion control software:
- Wafer alignment is done to ensure precise orientation of the wafer in X, Y, and Ø. This is critical to produce the initial map of inspection sites and to asssess the mapped sites in the future
- Mapping of the objective lens parcentration enables the offsets to be saved and helps to compensate any mechanical problems related to the microscope hardware
.jpg)
Figure 1. Semi-automated system
Following the first alignment sequences, the system moves automatically from a programmed location to the next, with sub-micron accuracy, for inspection purposes.
If there is a need to start automatic image capture, and/or initiate a ‘golden part comparison’, operator assistance is not required during system operation. If required, operators can also monitor the operation and disrupt the scan to save a specific field-of-view as a site of concern.
During these scans, digital images can be captured and revisited with the saved X, Y, theta location data, which has been automatically stored for individual images. After completing the inspection process for that particular wafer, the sample is removed from the stage, and the process is repeated as required.
Critical dimension (CD) measurement and detailed image analysis are other functions that can also be carried out. A modular system can be developed using this platform as a building block, and introducing components like automated wafer loading to the microscope stage. This type of system can be used in various inspection steps.
Download the Brochure for More Information
Conclusion
With the help of ProZ Column with other Prior Motorized components equipped with high-quality optics and powerful image analysis, fully or semi-automated wafer inspection can be realized to meet the objectives of wafer engineering, manufacturing, or failure analysis laboratories.
A high-performance inspection system can be created using motion control and image analysis software incorporated with Prior ProScan-3 XY Motorized Stage and ProZ Stand.
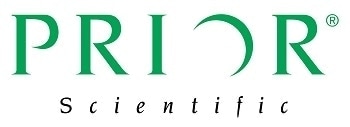
This information has been sourced, reviewed and adapted from materials provided by Prior Scientific Instruments Ltd.
For more information on this source, please visit Prior Scientific Instruments Ltd.