Sieving is a simple and low cost process, and has the ability to measure relatively coarse particles up to several centimeters in size, and these are some of the reasons that sieving is still in use throughout the manufacturing industry. However, it has pronounced drawbacks that make it unsuitable for supporting high productivity, modern manufacturing.
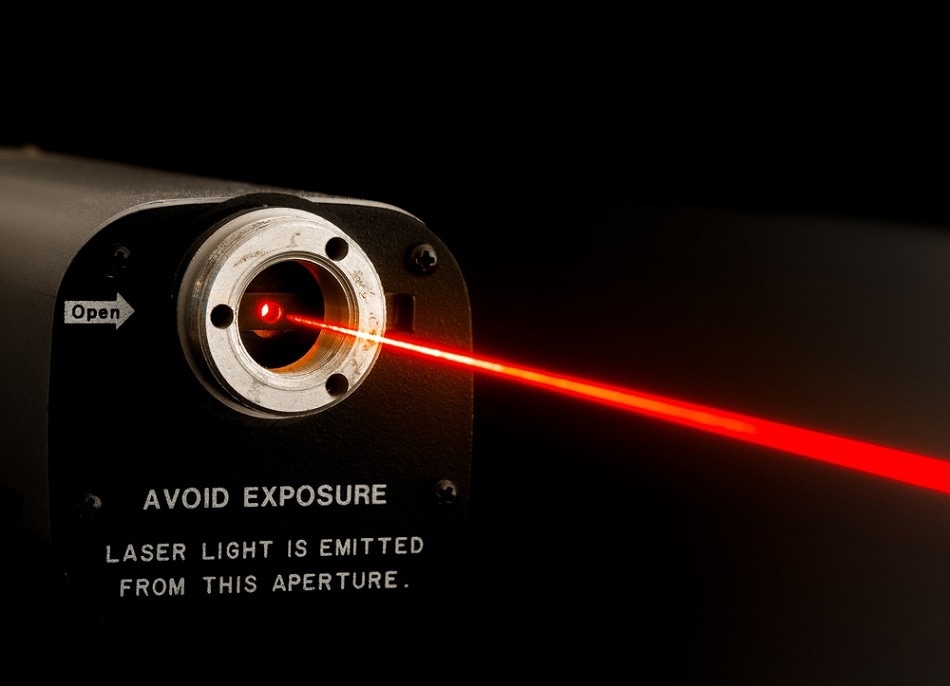
Moving to laser diffraction technology can address these drawbacks, as it not only offers faster, simpler analysis, but also provides a better resolution, wider measurement range, and easier maintenance. This article explains why a shift from sieving to laser diffraction should be a priority for manufacturers looking to improve efficiency and optimize analytical productivity.
Reason 1: Faster Analysis
Typical analysis times: Laser diffraction - under 1 minute; Sieving – 5 - 10 minutes
Faster analysis means more responsive and effective process control, increased throughput/productivity, and faster product release. The preparation required for sieve analysis is time-consuming as each sieve needs to be weighed before the sieve stack is constructed. It is also necessary to weigh the sample before loading into the top sieve.
The stack is then shaken for typically five minutes minimum, however polydisperse samples often require longer. After shaking the stack, each sieve and its contents need to be weighed. These processes often need to be repeated several times as part of method development, or to monitor the ongoing effectiveness of the measurement method.
Laser diffraction is much more automated. After defining a standard operating procedure (SOP), performing routine analysis is as simple as adding the sample and starting the measurement. Sample dispersion and measurement are then carried out without any manual intervention.
Typically, it takes less than a minute to complete the whole measurement, enabling rapid reporting of key quality control data. This results in improved product consistency.
Reason 2: Increased Measurement Range, Including Very Fine Particles
Laser diffraction measures particles from 10 nm to several mm in a single measurement, while sieving fails below 100 µm
A broader measurement range delivers:
- Improved product differentiation, by enabling the development and quality control of materials that benefit from properties associated with finer particle sizes
- Versatility of application, optimizing return on investment for the analytical system
- Future-proofing: broader capabilities can deal with evolving analytical requirements
Fine particles cannot be effectively measured using the sieving method because of the force of adhesion between particles, which increases quickly as the particle size reduces in the sub-100 micron region. During sieving, this can result in particle size changes due to particle agglomeration, causing poor measurement reproducibility and/or sieve blocking. A potential solution is wet sieving, but this requires longer equipment set-up times.
In laser diffraction, it is possible to achieve rapid dry powder dispersion for samples consisting of very fine or even sub-micron particles. The measurement range can be further extended to around 10 nm by liquid-based dispersion, enabling routine analysis of nanomaterials.
Both coarse and fine materials can be measured within a single automated measurement. Consequently, different product grades, including those with very broad particle size distributions, can be reproducibly characterized.
Reason 3: Simpler Analysis
Analytical procedures and manual interventions needed for laser diffraction are fewer and less complex than those for sieving
Simpler analytical procedures reduce the training requirements for new analysts, and minimize the potential for erroneous results. Increasing analytical productivity is another benefit, which helps to free up time for higher value tasks.
Sieve analysis is a multi-step procedure that requires numerous weighing steps and various manual interventions. The sieve and sample weighing data must then be processed to calculate the particle size distribution.
Manual intervention is virtually eliminated when modern laser diffraction systems are used in routine analysis. The light scattering data needed for laser diffraction particle size calculations is automatically collected immediately after the sample enters the laser diffraction measurement zone.
Particle size data and distributions can then be obtained by analyzing this data. As it is possible to follow the measurement process in real time, immediate feedback can be provided on the repeatability of analysis and product quality issues can be instantly identified.
Reason 4: Trouble-Free Maintenance
Routine maintenance of modern laser diffraction systems is minimal compared with that needed to keep sieves ‘fit for purpose’
Routine maintenance requirements have a large impact on analyst productivity, equipment utilization and the need for downtime, and the lifetime cost of ownership. It is necessary to dismantle the sieve stack and carefully clean each sieve with a fine brush after each sieve analysis. This is especially critical for fine powders as they can block the sieve mesh due to their tendency to agglomerate.
The sieves must also be routinely and rigorously examined to identify the damage caused to the sieve mesh, a major source of poor quality analysis.
Following a dry powder laser diffraction measurement, the only routine maintenance required is to remove any residual sample with a brush down. Flushing with clean liquid fulfills the same requirement in the case of a wet measurement.
Automated cleaning procedures incorporated in modern systems quickly return the instrument to operational readiness. These advanced systems are specifically designed to meet the requirement for ‘workhorse’ instruments relied upon by many novice users.
Minimal cleaning requirements enable rapid switching from one type of sample to another, while occasional maintenance tasks are made simpler by increasing the accessibility of key components, such as measurement cell windows.
Reason 5: Better measurement resolution for improved product quality
Laser diffraction reports 100 size classes over the full measurement range, compared to 5–8 size classes reported by sieving analysis
More detailed resolution of a sample provides more informative particle size distribution data, enabling:
- Faster detection and resolution of production issues
- Improved control over product quality, allowing for access to premium markets
- Better understanding of the relationship between particle size and product performance
A sieve stack typically only contains five to eight sieves, principally to ensure that measurement times do not become unmanageable. Therefore, size classes across the measurement range are few and wide, making the technique ineffective in detecting subtle differences in particle size.
This is particularly problematic when there are variations in the amount of material at the extremes of the size distribution – the very coarse or very fine particle fractions.
The laser diffraction method reports 100 size classes over the full measurement range, offering far more precise resolution compared to the sieving technique and detecting even the smallest changes in particle size distribution.
In the manufacturing industry, this capability makes identifying a process change at an early stage easier to take corrective action before a major problem develops. It also enables rapid and sensitive detection of out of specification material for feeds as well as products.
Next Steps
If any of the aforementioned reasons have prompted you to switching from the sieving technique to the laser diffraction technique, or have led to further questions, Malvern Panalytical has have lots of information that can help..
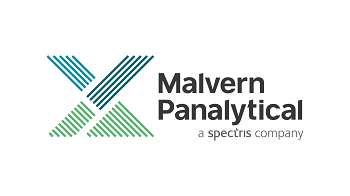
This information has been sourced, reviewed and adapted from materials provided by Malvern Panalytical.
For more information on this source, please visit Malvern Panalytical.