Airborne Molecular Contaminants in Cleanroom Air
As consumers demand higher performance from electronic goods, greater demand is placed on precision engineering and the quality of sub-components and silicon-based materials, such as hard disk drives.
.jpg)
However, the presence of semi-volatile organic compounds (SVOCs), known in the industry as airborne molecular contaminants (AMCs), can negatively affect the performance of these components. Challenging AMCs include antioxidants, plasticizers (such as phthalates), amines and amides, siloxanes, flame retardants, and organophosphates.
One of the main sources of AMCs is outgassing from materials, and these may include:
- Computer components
- Construction products used in the cleanroom, including plastics
- Particulate air filters
- Consumables such as tape, garments, gloves, and cleaning materials
- People
As AMCs are in vapor form they can pass through most standard particulate air filters, leading to their presence in the cleanroom environment. As a result, it is important for technology industries, particularly semiconductor manufacturers, to monitor cleanroom air for SVOCs as well as reduce emissions from all materials and products used in cleanrooms.
As a first line of defence, all cleanroom materials are pre-screened by hard disk drive manufacturers for outgassing of specific SVOCs (organics with b.p. >150 °C, called ‘condensables’, and amines).
Standard Methods
In June 2013, a guideline was published called; VDI 2083-17A (Cleanroom technology – Compatibility of materials with the required cleanliness). This defines a standardized approach using microchambers for the classification of cleanroom-suitable materials in accordance with their VOC outgassing properties.
The guideline also contains a database for selection and comparison of materials, and serves as a useful tool to all engineers involved in cleanroom planning and operation to help estimate the predicted level of total volatile organic compounds (TVOC).
In the meantime, formerly used methods such as ASTM F1227 and ASTM F1982 have been withdrawn, and the SEMI International Standards, the global industry association for the micro- and nano-electronics industries, has undertaken the publication of two similar methods:
- SEMI E108-0307: Test method for the assessment of outgassing organic contamination from minienvironments using gas chromatography/mass spectroscopy
- MF1982-1110: Test method for analyzing organic contaminants on silicon wafer surfaces by thermal desorption gas chromatography
Direct and Indirect Outgassing
The following methods are extensively used to assess outgassing:
- Direct outgassing – This includes the assessment of total outgassing from components or materials under fixed conditions (time, temperature, gas flow, etc.). This can be performed by measuring weight loss, or, for qualitative and quantitative identification of compounds released, by direct thermal desorption (TD) with GC–MS
- Indirect outgassing – This involves the analysis of ‘witness wafers’ – blank silicon wafers that are used to collect volatiles present in the cleanroom atmosphere
What Markes can Offer
Equipment for Monitoring of Cleanroom Air
Cleanroom air can be routinely monitored by pumped sampling onto sorbent tubes, followed by analysis by TD–GC–MS.
Equipment for Determining Material Outgassing
In many industries, the outgassing of materials employed in cleanrooms has become increasingly significant, with a maximum allowed level of VOC contamination typically defined in the planning phase of cleanrooms in the aerospace, photovoltaic, and semiconductor industries (in accordance with VDI 2083-17A or ISO 14644-8).
Materials used in the cleanrooms or in the final products can be screened with two sampling methods:
- Assessing the representative vapor profile of bulk materials - This technique uses Markes’ Micro-Chamber/Thermal Extractor and involves placing gram-quantities of a material in one of the microchambers. These microchambers are then heated while a flow of gas is applied and the vapors released are subsequently collected on a sorbent tube for analysis by TD–GC–MS. About six samples can be collected every hour, and the results can be correlated with those of reference methods, making it an ideal tool for quick emissions screening
- Exhaustive extraction of small samples by direct desorption - This technique is quite simple and involves placing a small (milligram) amount of the sample in an empty TD tube. This tube is subsequently heated and the vapors are analyzed by TD–GC–MS (for instance, using UNITY-xr or TD100-xr thermal desorbers from Markes)
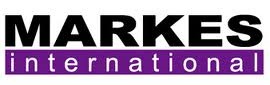
This information has been sourced, reviewed and adapted from materials provided by Markes International Limited.
For more information on this source, please visit Markes International Limited.